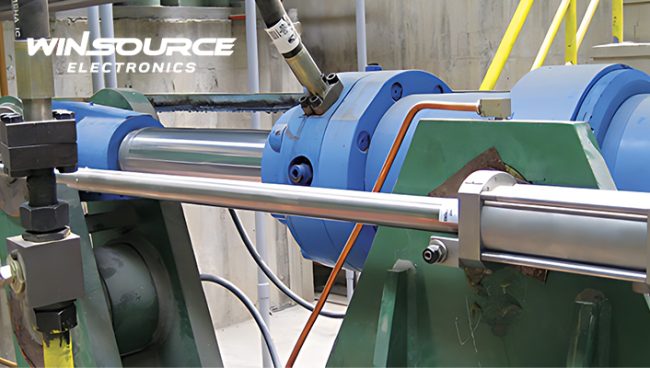
A linear displacement transducer (LDT), also known as a linear position sensor or linear displacement sensor, is a device used to measure an object’s linear movement or position. It provides information about the object’s location along a straight line. Linear displacement transducers are employed in various industrial, automotive, and scientific applications where monitoring and controlling position are crucial.
Different Types of LDTs
There are different linear displacement transducers, each with its own working principle and characteristics. Some common types include:
Potentiometric Transducers
These sensors use the change in resistance of a potentiometer to measure linear displacement. As the object moves, the potentiometer’s wiper changes its position, altering the resistance and providing a voltage output proportional to the displacement.
Linear Variable Differential Transformer or LVDT
LVDT, or linear variable differential transformer, is a non-contact transducer that uses the movement of a ferromagnetic core within a set of coils to generate an output proportional to linear displacement. An example of LDVT is Ametek Gemco Digital Control Pulse LDT, which has product code 953D-CP-3020-XXBX.
Magnetostrictive Transducers
These sensors use the principle of magnetostriction, which measures the change in the magnetic properties of a material (usually a wire) due to mechanical stress. As the object moves, it alters the magnetic field in the wire, allowing displacement measurement.
Capacitive Transducers
Capacitive sensors measure changes in capacitance as the distance between plates changes. These are often used in microscale applications and situations requiring high precision.
Optical Encoders
These sensors use optical principles to measure linear displacement. Light sources and sensors are arranged so that the interruption or reflection of light provides information about the object’s position.
Linear displacement transducers are chosen based on an application’s specific requirements, including factors such as precision, environmental conditions, and the nature of the measured object’s movement. They play a critical role in applications ranging from manufacturing and automation to robotics and scientific research.
How Do LDTs Work?
The way linear displacement transducers operate depends on their specific type, as listed above. Here are three different ways on how LDTs work:
Potentiometric LDTs
These LDTs utilize the change in resistance of a potentiometer in response to linear motion. As the object moves, the potentiometer’s wiper changes its position, causing a variation in resistance. The output voltage is proportional to the linear displacement.
LVDT (Linear Variable Differential Transformer)
LVDTs are non-contact transducers that rely on electromagnetic induction. One specific example is Ametek Gemco’s 953D-CP-3020-XXBX. Here is how LVDTs like XXBX work:
An LVDT like the XXBX typically consists of a primary coil and two secondary coils wound in opposite directions.
A ferromagnetic core is positioned within the coil assembly.
When an AC voltage is applied to the primary coil, it induces voltages in the two secondary coils.
The position of the core within the coil assembly changes with linear displacement, causing a variation in the amplitude and phase of the induced voltages.
By measuring these changes, the linear displacement of the core (and, by extension, the measured object) can be determined.
Magnetostrictive LDTs
Magnetostrictive LDTs rely on the change in magnetic properties of a material (often a wire) due to mechanical stress. Here is how they work:
A magnetostrictive waveguide is typically used, consisting of a magnetostrictive wire surrounded by a non-magnetic sheath.
An electrical pulse is sent along the wire, generating a magnetic field around it.
When the pulse encounters the position of a magnet attached to the moving object, it creates a torsional stress in the wire.
The time it takes for the torsional stress to return to the sensor is measured, and this time delay is directly related to the linear displacement.
Exploring Ametek Gemco’s Digital Control Pulse LDT (953D-CP-3020-XXBX)
Introducing the Ametek Gemco 953D VMAX (with product code 953D CP 3020 XXBX), a cutting-edge programmable non-contact linear displacement transducer meticulously designed for precise and reliable performance in a rod-style package. Leveraging the proven magnetostrictive technology, this transducer delivers absolute position accuracy with an impressive precision of 0.01% of the sensing distance.
Key Features of 953D VMAX (with product code 953D CP 3020 XXBX)
Wide Power Range: The 953D VMAX operates efficiently within a broad power range from 7 to 30 VDC @ 1 watt. This ensures versatility and compatibility with various power setups, contributing to its adaptability in diverse applications.
Auto-Tuning Capability: Setting itself apart, the 953D CP 3020 XXBX LTD boasts an intelligent auto-tuning capability. It can effortlessly adapt to sense magnets other than the standard ring magnet, adjusting its signal strength accordingly. This feature enhances flexibility and ease of integration, catering to unique application requirements.
Diagnostic LED: The 953D VMAX is equipped with a diagnostic LED, a valuable tool for real-time status monitoring. The LED remains green when detecting a good magnet signal, providing instant visual feedback. In the absence of a magnet or if it is positioned outside the sensing area, the LED turns red, facilitating quick identification of potential issues.
Customizable Span Lengths: Addressing diverse measurement needs, the unit can be conveniently ordered in span lengths ranging from 1″ to an expansive 300″, allowing for tailored solutions in increments as acceptable as 0.1″.
Precision, adaptability, and user-friendly diagnostics converge in the Ametek Gemco 953D VMAX (with product code 953D CP 3020 XXBX), making it an unparalleled choice for applications demanding non-contact linear displacement sensing with absolute accuracy.
Are you looking for a reliable supplier of LDTs such as 953D CP 3020 XXBX? Look no further because WIN SOURCE carries a vast collection of electronic parts and components. Directly sourced from our extensive product lines range from sensors and transducers to integrated circuits, resistors, isolators, and more. Get the best deals from WIN SOURCE.
COMMENTS