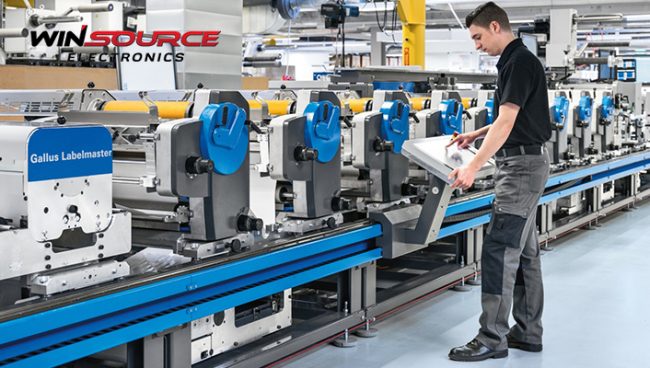
Label Master is a leader in providing comprehensive labeling, compliance, and safety solutions in various industries. With a dedicated focus on regulatory adherence and risk mitigation, Label Master has established itself as a reliable partner for businesses navigating complex compliance landscapes.
Understanding Compliance Challenges
Compliance remains crucial across industries in today’s ever-evolving regulatory environment. Label Master recognizes businesses’ multifaceted challenges in ensuring adherence to safety regulations, transportation guidelines, and hazardous material handling protocols.
Comprehensive Solutions Portfolio
Label Main suite of solutions encompasses diverse facets of compliance and safety. From offering customizable labeling solutions tailored to specific industry standards to providing comprehensive training modules on safety protocols, their expertise spans a broad spectrum. Their offerings often include:
- Labelling Solutions: Tailored labeling products and software designed to meet stringent regulatory requirements. These encompass GHS labeling, hazardous material identification, and specialized labeling for transportation.
- Regulatory Compliance Support: Expert consultation and guidance on navigating complex regulatory frameworks, ensuring businesses stay updated and compliant with the latest mandates.
- Safety Training Programs: Educational resources and training modules aimed at promoting safety awareness and best practices in handling hazardous materials and compliance-related matters.
- Advisory Services: Customized advisory services designed to assist businesses in streamlining their compliance processes and minimizing risk exposure.
Customer-Centric Approach
Label Master prioritizes customer satisfaction and efficacy in their solutions. Their approach involves understanding unique client needs and delivering tailored, practical, and efficient solutions. Whether for small enterprises or large corporations, Label Master aims to be a trusted partner in their journey towards compliance and safety excellence.
Embracing Technological Advancements
In an era of rapid technological evolution, Label Master stays ahead by embracing innovation. This involves leveraging cutting-edge software, automation, and digitization to enhance the efficiency and accuracy of compliance processes.
Commitment to Quality and Reliability
Label Master’s commitment to quality is evident in its product offerings, services, and customer support. Their dedication to reliability, accuracy, and timely delivery of solutions fosters enduring relationships with clients.
What is a Q64 Elapsed Time Meter?
The Q64 Elapsed Time Meter is an electronic part used to measure and display the elapsed time of an operation or process. Specifically designed for industrial applications, this meter tracks an event’s duration, such as a machine’s running time, a process cycle, or the course of a specific task.
Key features of an elapsed time meter like the Q64 may include:
- Accuracy: Precise measurement and display of time elapsed.
- Versatility: Ability to measure time in various units (seconds, minutes, hours).
- Durability: Designed to withstand industrial environments, including resistance to vibration, temperature variations, and other challenging conditions.
- Installation: Typically panel-mounted or installed within control systems for monitoring purposes.
- Configurability: Some models may offer configurable settings for start/stop functions, reset options, or different display formats.
These meters are essential in industries where tracking time is crucial for operational efficiency, maintenance scheduling, process optimization, or compliance with specific timing requirements. They provide a reliable means to monitor how long a system or process has been in operation. They aid in maintenance scheduling or troubleshooting by identifying trends or irregularities in operation duration.
Benefits of using Q64 Elapsed Time Meter
Siemens’ Q64 Elapsed Time Meter, like similar devices, is a reliable tool for industrial settings where accurate time tracking is essential for monitoring and managing various processes or machinery.
- Maintenance Scheduling: Time meters help schedule regular maintenance tasks based on the running duration of machinery or equipment. Routine maintenance prevents breakdowns and ensures optimal performance.
- Monitoring Equipment Usage: They track how long machinery or devices have been in operation, allowing for better management of their usage and lifecycle.
- Efficiency Tracking: Time meters help analyze and improve operational efficiency by measuring the time taken for specific processes, identifying bottlenecks, and optimizing workflows.
- Billing and Cost Calculation: Time meters might be used for billing purposes in some instances, especially in services where usage duration determines costs, like rental equipment or services.
- Compliance and Regulation: Some industries have regulations or standards that require tracking the duration of specific operations. Time meters help in ensuring compliance with these standards.
- Process Optimization: Analyzing the time taken for various stages of a process helps identify areas for improvement, reduce cycle times, and enhance productivity.
- Diagnostic and Troubleshooting: Monitoring the elapsed time can help identify irregularities or unexpected changes in equipment behavior, facilitating troubleshooting and diagnostics.
Time meters provide valuable data for better management, optimization, and maintenance of equipment and processes across various industries, contributing significantly to operational efficiency, cost-effectiveness, and compliance.
How to Install Elapsed Time Meter?
Install the meter in a suitable location to be easily viewed and accessed for monitoring purposes. This might involve panel mounting or integration into existing control systems. Connect the meter to a power source and the system or equipment whose operation duration you want to measure. Follow the manufacturer’s wiring instructions and ensure proper connections for accurate readings.
Configuration:
Settings: Configure the meter based on the units of time you want to measure (e.g., seconds, minutes, hours). Some meters may have grounds for start/stop functions, reset options, or different display formats.
Operation:
Start Function: Activate the elapsed time meter to begin recording time. This might involve pressing a start button or initiating the meter through the system it’s connected to.
Monitoring: Once activated, the meter will start counting and displaying the elapsed time. Continuously monitor the display to track the duration of the operation or process.
Reset and Maintenance:
Resetting: If the meter has a reset function, use it when necessary. This is typically done when starting a new cycle or after completing a specific task to reset the timer to zero.
Maintenance: Ensure the elapsed time meter is maintained periodically per the manufacturer’s recommendations. Check for accuracy, clean the display, and inspect the connections to ensure proper functioning.
Troubleshooting:
Diagnostic Use: The meter might aid in troubleshooting by providing information on the duration of operations. Any irregularities or unexpected changes in elapsed time could indicate issues that need attention.
WIN SOURCE emerges as a leading distributor of electronic components. Committed to eradicating fraud, they present over 1M quality parts with a three-year guarantee from their AS9120B certification.
Since 1999, they have focused on efficient supply management, cost-effective procurement, and rapid sourcing and delivery. Understanding the challenges in sourcing obsolete components, they optimize inventory and global supplier networks, reducing procurement cycles by up to 60%.
COMMENTS