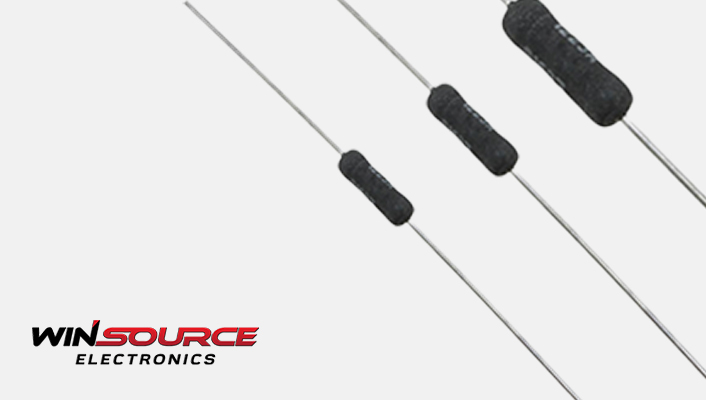
In the design and manufacturing of electronic components, precision wirewound resistors like the RWR80S2000FR play an essential role. These resistors offer irreplaceable solutions that ensure accuracy and reliability in circuit design. Applications demanding high environmental stability and consistent performance, such as military, aerospace, and precision measurement devices, rely heavily on them. This article explores technological advancements in this field, focusing particularly on material selection, manufacturing techniques, and performance evaluation.
Material Innovation and Performance Enhancement
Engineers developed the RWR80S2000FR using advanced material science. They chose copper-nickel alloys for their excellent resistance stability and low temperature coefficients. These alloys also offer strong mechanical strength and resist corrosion. As a result, the RWR80S2000FR performs reliably even in harsh environments.
They ensured accuracy by focusing on the resistance wire. The team carefully controlled the wire’s diameter and winding density. They used advanced automation to keep the winding process precise. This control helps the RWR80S2000FR deliver consistent resistance values.
To improve stability, engineers applied micro-alloying techniques. They used thermal treatments to refine the wire’s crystal structure. These steps increased both electrical and thermal stability. The RWR80S2000FR benefits from these improvements, especially in high-precision applications.
They also optimized the winding process. This gave the RWR80S2000FR better long-term reliability. The resistor maintains its performance over time, making it ideal for demanding, accuracy-critical systems.
Application of Precision Engineering Techniques
Use of High-Precision Automated Winding Machinery
Automated winding machinery with precise control systems is used in producing the RWR80S2000FRRSL. These systems maintain high-speed production while controlling the tension and precise alignment of the wire accurately. Advanced programming and mechanical synchronization ensure each winding complies with predefined specifications.
Implementation of Real-Time Monitoring Technologies
Real-time monitoring systems track key parameters during the production process, such as wire tension, speed, and winding angle. The system immediately identifies any deviations from set parameters, automatically adjusting or alerting operators to intervene. This real-time feedback mechanism is crucial for ensuring product quality and reducing waste.
Integration of Computer Vision Systems
Computer vision systems play a crucial role in the production of the RWR80S2000FRRSL. High-resolution cameras continuously scan the winding process, and image processing software analyzes the quality of the windings. The system detects minute defects or inconsistencies, such as uneven winding density or slight misalignments. Upon detecting issues, it automatically adjusts the mechanical parameters or alerts operators to ensure each coil meets strict quality standards.
Application of Advanced Sensors and Feedback Systems
Integrated sensors and feedback systems in the production equipment monitor and adjust various production parameters. They respond to changes in environmental conditions or material batch variations. For example, if ambient temperature or humidity changes affect material properties, the system automatically adjusts processing parameters to accommodate these changes. This intelligent adjustment ensures products maintain high-quality standards even under varying production conditions.
These advanced precision engineering technologies not only optimize the production process but also significantly enhance the reliability and performance of the RWR80S2000FRRSL resistors. They meet and exceed market demands for high-precision electronic components. The application of these technologies marks a trend toward higher automation and intelligence in electronics manufacturing.
RWR80S2000FR Quality Assurance
Evaluating high-precision wirewound resistors involves sophisticated testing equipment and stringent quality control systems. Each batch of RWR80S2000FRRSL resistors undergoes multiple stages of testing. Tests include initial electrical performance, long-term stability, and environmental stress screening. These tests ensure each product operates within specified tolerances and assesses its performance under extreme conditions. Laser 3D scanning and resistance imaging techniques are used for deeper inspection, identifying any potential defects that could lead to performance degradation. These advanced testing methods ensure resistors meet the highest quality standards before reaching the market.
Future Application Prospects
As technology advances and new applications emerge, demand for high-precision wirewound resistors is increasing. RWR80S2000FRRSL and similar products are expected to play a significant role in wireless communication, automated control systems, and renewable energy technology. The proliferation of the Internet of Things (IoT) and smart devices will further increase the importance of these precision components, particularly in ensuring system reliability and optimizing performance.
These resistors will also find new applications in cutting-edge technologies like autonomous vehicles, high-speed communication networks, and smart manufacturing. In these applications, component accuracy and reliability are critical. They must maintain performance under extreme conditions to ensure system stability.
As a leading distributor of electronic components, WIN SOURCE specialises in providing high quality electronic assemblies and technical services. We cater for the needs of engineers and manufacturers, supporting them from prototyping to final production. We provide resistor solutions to ensure that our customers meet the technological challenges of the future. When you choose WIN SOURCE, you are choosing to work with a leading supplier of components.
© 2024 Win Source Electronics. All rights reserved. This content is protected by copyright and may not be reproduced, distributed, transmitted, cached or otherwise used, except with the prior written permission of Win Source Electronics
COMMENTS