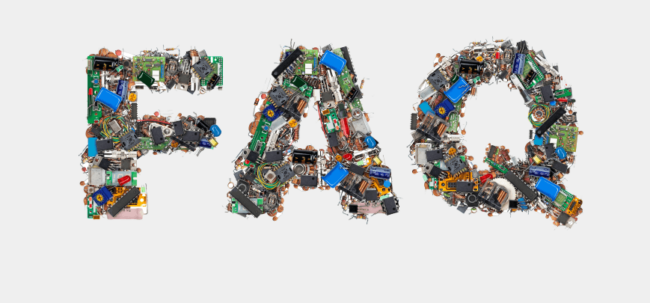
An example of a representative embedded system?
One representative example of an embedded system is a “Smart Thermostat.” A smart thermostat is a device used to control and regulate the temperature of heating, ventilation, and air conditioning (HVAC) systems in homes or commercial buildings. It is an embedded system because it incorporates a microcontroller or microprocessor along with various sensors and actuators to perform its intended functions. Here’s an overview of the key features and components of a smart thermostat as an embedded system:
- Microcontroller/Microprocessor: The heart of the smart thermostat is a microcontroller or microprocessor that serves as the central processing unit. It executes the embedded software and manages the overall operation of the thermostat.
- Temperature Sensors: Smart thermostats typically include built-in temperature sensors or external sensors to monitor the ambient temperature of the room or the building.
- Humidity Sensor: Some smart thermostats also incorporate a humidity sensor to measure the moisture level in the air.
- User Interface: A user interface is provided for users to interact with the smart thermostat. This can be in the form of buttons, touchscreens, or even smartphone apps that allow users to set temperature preferences, schedule heating/cooling periods, and access other features.
- Communication Interface: Embedded systems like smart thermostats often have communication interfaces like Wi-Fi, Bluetooth, Zigbee, or others to connect to home automation systems or the internet for remote control and monitoring.
- Connectivity: Smart thermostats can connect to the home Wi-Fi network to enable remote control and access through smartphone apps or web portals.
- Memory: The embedded system requires memory to store the program code, settings, and user preferences.
- Real-Time Clock (RTC): An RTC is often included to keep track of the current time and date, which is essential for scheduling heating/cooling periods and automation.
- Actuators: Smart thermostats use relays or other actuators to control the heating and cooling systems, turning them on or off as needed to maintain the desired temperature.
- Energy Efficiency and Learning Algorithms: Many modern smart thermostats incorporate advanced algorithms to learn user preferences and optimize heating and cooling patterns for energy efficiency.
- Security: As smart thermostats are connected devices, security features like encryption and authentication are essential to protect user data and prevent unauthorized access.
Smart thermostats are just one example of the wide range of embedded systems found in various applications, including consumer electronics, automotive systems, industrial automation, medical devices, and more. These embedded systems bring intelligence and functionality to devices and products, making them more capable, efficient, and user-friendly.
What are the functions of the AD603 pin?
The AD603 is an operational amplifier (op-amp) with a high-performance, low-noise, and wideband variable gain amplifier (VGA) function. It is designed by Analog Devices for a variety of applications, including communication systems, instrumentation, and signal processing. The AD603 IC has several pins, each serving specific functions. Here are the functions of some key pins on the AD603:
- VPOS (Pin 1): VPOS is the positive power supply pin for the AD603. It provides the positive power voltage required for the IC’s operation.
- VNEG (Pin 2): VNEG is the negative power supply pin for the AD603. It provides the negative power voltage required for the IC’s operation.
- GND (Pin 3): The GND pin is connected to the ground reference of the circuit.
- INHI (Pin 4): INHI is the high-level differential input pin for the op-amp. It is one of the inputs to the variable gain amplifier.
- INLO (Pin 5): INLO is the low-level differential input pin for the op-amp. It is the other input to the variable gain amplifier.
- VSET (Pin 6): VSET is the gain-setting control voltage input for the variable gain amplifier. By applying a voltage to this pin, the user can control the gain of the amplifier.
- GAIN (Pin 7): The GAIN pin is used to set the overall gain mode of the AD603. By tying this pin to the supply voltage or ground, the user can select between a high-gain mode or low-gain mode.
- AGC (Pin 8): AGC stands for Automatic Gain Control. The AGC pin is used to enable or disable the automatic gain control feature of the AD603. When AGC is disabled, the gain is set based on the voltage applied to the VSET pin.
- VFILT (Pin 9): VFILT is the filter control pin for the output filter. It is used to select the filter bandwidth based on the application requirements.
- NC (Pin 10): NC stands for No Connection. The NC pin is not internally connected and is left unconnected during circuit implementation.
- VOUT (Pin 11): VOUT is the output pin of the AD603. The amplified signal appears at this pin.
- VS (Pin 12): VS is the supply voltage pin for the output buffer amplifier.
It’s essential to consult the datasheet of the AD603 for a complete understanding of the pin functions, electrical characteristics, and application circuit examples for proper usage of the IC in specific designs.
What are the main resource configurations of the OK6410 evaluation board?
As of my last knowledge update in September 2021, the OK6410 evaluation board is an ARM-based development board designed by FriendlyARM for evaluating and prototyping with Samsung’s S3C6410 processor. The OK6410 board features various resources and interfaces to support a wide range of applications. The main resource configurations of the OK6410 evaluation board include:
- Samsung S3C6410 Processor: The board is built around the Samsung S3C6410 ARM11 processor, which is a powerful and versatile system-on-chip (SoC) with various integrated peripherals.
- RAM: The OK6410 evaluation board typically comes with onboard DDR RAM, providing a decent amount of memory for running applications and storing data.
- Flash Memory: The board usually includes a NOR flash for storing the bootloader and other essential system code.
- Connectivity: The OK6410 board supports various connectivity options, including USB 2.0 Host and USB 2.0 OTG ports for connecting USB devices and acting as a USB host, respectively. It may also include Ethernet (RJ45) for networking capabilities.
- Display and Multimedia: The board is equipped with an LCD connector for connecting TFT-LCD displays, allowing developers to work with graphical user interfaces. It also has TV-out (composite video) for displaying content on a TV or monitor.
- Touchscreen: The OK6410 evaluation board often includes a touchscreen controller interface, enabling the use of touch-enabled displays.
- Audio: The board has audio input and output interfaces, supporting audio playback and recording capabilities.
- Expansion Headers: The OK6410 board features various expansion headers, allowing access to the GPIO (General Purpose Input/Output) pins for connecting additional peripherals and custom circuitry.
- UART and Debugging: The board typically has UART (serial communication) interfaces for debugging and communication with other devices.
- Power Supply: The board is powered through a standard DC power supply or USB power, providing the required voltages to the components on the board.
- User Interface: The OK6410 board may include buttons, LEDs, and other user interface elements for easy interaction and testing of hardware and software functionalities.
- Operating System Support: The OK6410 board supports various operating systems, including Linux and Windows CE, providing flexibility for developers to choose their preferred OS for application development.
It’s important to note that hardware configurations and specifications may vary depending on the specific version or revision of the OK6410 evaluation board. For the most up-to-date and detailed information, I recommend consulting the official documentation or datasheets provided by FriendlyARM for the OK6410 board.
What are the system functions of μC/OS-II?
μC/OS-II (MicroC/OS-II) is a real-time operating system (RTOS) kernel developed by Jean J. Labrosse and maintained by Micrium Inc. It is designed to provide preemptive multitasking, inter-process communication, and other essential services for embedded systems and real-time applications. The system functions of μC/OS-II include:
- Task Management: μC/OS-II allows the creation, deletion, and management of multiple tasks. Tasks are independent threads of execution, each with its own stack and priority. The kernel provides mechanisms for task scheduling, context switching, and time slicing to ensure proper execution of tasks.
- Task Synchronization: μC/OS-II supports various synchronization mechanisms to coordinate the execution of tasks. This includes semaphores, mutexes, and event flags, which are used to manage access to shared resources, prevent race conditions, and implement mutual exclusion.
- Task Communication: The RTOS kernel offers inter-process communication mechanisms like message queues and mailboxes, enabling tasks to exchange data and messages in a synchronized and thread-safe manner.
- Time Management: μC/OS-II provides time-related services, including support for software timers and time delay functions. Software timers allow tasks to be scheduled at specific intervals, while time delay functions enable tasks to suspend their execution for a specified period.
- Memory Management: The RTOS kernel includes memory management services to allocate and deallocate memory dynamically during the runtime of the system. It provides memory pool management and memory partitioning, which allows tasks to request and release memory blocks efficiently.
- Event Handling: μC/OS-II supports event-driven programming through the use of event flags and event groups. Tasks can wait for specific events to occur and respond accordingly when signaled.
- Interrupt Management: The RTOS kernel offers services to manage interrupts in real-time systems. It allows critical sections of code to be protected from interruption, ensuring data integrity and preventing race conditions.
- Error Handling and Debugging: μC/OS-II provides facilities for error handling and debugging, including error codes and hooks that developers can use to customize error handling behavior.
- Resource Management: The RTOS kernel allows tasks to manage and control access to shared resources, preventing conflicts and ensuring resource utilization efficiency.
- CPU and System Management: μC/OS-II includes services to manage the CPU and system clocks, power management, and other low-level system functions.
- Preemption and Time Slicing: μC/OS-II supports preemption, allowing higher-priority tasks to preempt lower-priority tasks, ensuring critical tasks get executed in a timely manner. Time slicing allows tasks of equal priority to share the CPU in a round-robin manner.
Overall, μC/OS-II offers a comprehensive set of system functions that facilitate the development of robust and efficient real-time embedded applications. It has been widely used in various industries for many years and has a strong track record in the field of embedded systems development.
What is the correspondence between the register organization in the Thumb state and the register organization in the ARM state?
In ARM architecture, the processor can operate in two states: ARM state and Thumb state. In the ARM state, the processor executes ARM instructions, which are 32 bits in length. In the Thumb state, the processor executes Thumb instructions, which are 16 bits in length and provide a more compact code size, suitable for memory-constrained environments.
The correspondence between the register organization in the Thumb state and the register organization in the ARM state is as follows:
- General-Purpose Registers (R0-R15):
- In ARM state, there are 16 general-purpose registers, R0 to R15, each 32 bits in size.
- In Thumb state, there are only 8 general-purpose registers, R0 to R7. These registers are still 32 bits in size and have the same functionality as the lower half of the ARM state’s R0 to R7.
- Stack Pointer (SP) and Link Register (LR):
- The Stack Pointer (SP) and Link Register (LR) have the same functionality and usage in both ARM and Thumb states. They are used for managing the stack and subroutine calls.
- Program Counter (PC):
- The Program Counter (PC) in ARM state is 32 bits wide and holds the memory address of the current instruction being executed.
- In Thumb state, the PC is a 32-bit register as well, but it is automatically adjusted to hold the address of the next Thumb instruction after each 16-bit instruction is executed. This automatic adjustment allows seamless switching between ARM and Thumb states during code execution.
- Saved Program Status Register (SPSR):
- The SPSR is a special-purpose register that is only available in the ARM state. It is used to store the CPSR (Current Program Status Register) when an exception (interrupt or subroutine call) occurs. The Thumb state does not have an equivalent SPSR.
- CPSR and APSR:
- The CPSR (Current Program Status Register) is a 32-bit register that holds various flags and status bits that indicate the current processor state in the ARM state.
- In Thumb state, the CPSR is replaced by the APSR (Application Program Status Register). The APSR is a 32-bit register that stores status flags specifically related to the current application state in Thumb mode.
It’s important to note that while the register organization changes in Thumb mode to accommodate the narrower Thumb instructions, the core architectural features and capabilities of the processor remain consistent between the ARM and Thumb states. The processor can switch between these two states seamlessly during code execution, allowing for more efficient and compact code in memory-constrained environments without sacrificing the overall performance and flexibility of the ARM architecture.
What is the role of the dual state symbol IO field?
The dual state symbol IO field uses a bit variable to switch between two different texts.The symbolic IO field in the figure is connected to the bit change scene “Auto/Manual Switch” for displaying the operating mode of the system.Compared to the multi-state symbol IO field, the dual-state symbol IO field does not require a text list configuration and the configuration is very simple.
What is the principle of a pyroelectric sensor?
A pyroelectric sensor is a type of infrared (IR) sensor that detects changes in infrared radiation. It operates based on the principle of pyroelectric effect, which is the ability of certain materials to generate an electric charge when exposed to variations in temperature.
The key principle of a pyroelectric sensor can be summarized as follows:
- Pyroelectric Effect: Certain materials, such as certain crystals and ceramics, exhibit the pyroelectric effect. When these materials experience a change in temperature, their internal polarization changes, resulting in the redistribution of positive and negative charges within the material.
- Sensing Infrared Radiation: Pyroelectric sensors are designed to be sensitive to infrared radiation emitted by objects in their surroundings. When an object emits infrared radiation, it interacts with the pyroelectric material of the sensor, causing a change in temperature on the sensor’s surface.
- Charge Generation: As the temperature of the pyroelectric material changes due to the incident infrared radiation, it causes a shift in the internal polarization of the material, resulting in the generation of electric charges on the surface of the material.
- Sensing Circuit: The generated electric charges are collected by the sensing circuitry integrated with the pyroelectric sensor. The sensing circuit converts the charge into a measurable voltage signal proportional to the incident infrared radiation’s intensity and frequency.
- Output Signal: The voltage signal from the sensing circuit serves as the output of the pyroelectric sensor. This output can be used to detect and measure changes in infrared radiation, such as those caused by the movement or presence of objects or living beings in the sensor’s field of view.
Pyroelectric sensors are commonly used in various applications, including motion detectors, occupancy sensors, security systems, and non-contact temperature measurements. They offer advantages such as fast response times, low power consumption, and immunity to visible light interference. Their ability to detect changes in temperature without the need for a continuous power source makes them well-suited for battery-operated and energy-efficient applications.
What are the basic steps of the VHDL language design of the combined circuit?
Designing a combined circuit using the VHDL (VHSIC Hardware Description Language) involves several steps to describe the behavior and structure of the circuit. The basic steps of VHDL language design for a combined circuit are as follows:
- Specification and Requirements:
- Define the specifications and requirements of the combined circuit. Understand the functionality and behavior that the circuit needs to exhibit.
- Architecture Design:
- Start by creating an entity declaration that defines the interface of the combined circuit. The entity declaration specifies the inputs, outputs, and any generic parameters of the circuit.
- Next, design the architecture of the circuit. The architecture describes the internal behavior of the circuit and how it processes the inputs to produce the desired outputs.
- Select the appropriate architecture style, such as behavioral, dataflow, or structural, depending on the complexity and requirements of the circuit.
- Behavioral Description:
- Use behavioral VHDL constructs to describe the functional behavior of the combined circuit. Behavioral description focuses on what the circuit does, rather than how it is implemented.
- Use processes, if-else statements, loops, and other control structures to describe the circuit’s operation based on the given specifications.
- Dataflow Description:
- For some circuits, dataflow modeling may be more appropriate. Dataflow modeling describes how data flows through the circuit from input to output.
- Use concurrent signal assignment statements to model the flow of data through different logic elements.
- Structural Description:
- For complex circuits, structural modeling may be necessary. Structural modeling describes how the circuit is composed of interconnected sub-components.
- Instantiate other entities or components inside the main entity to represent the various building blocks of the circuit.
- Simulation and Verification:
- Write testbenches to simulate and verify the functionality of the combined circuit. Testbenches are modules that provide stimulus to the circuit and check the correctness of the outputs.
- Run the simulation to ensure that the circuit meets the specified requirements and operates as expected.
- Synthesis and Implementation:
- After successful simulation and verification, synthesize the VHDL code to convert it into a hardware description language that can be used to program FPGAs or ASICs.
- Implement the circuit on the target hardware, such as an FPGA, to create the physical combined circuit.
- Post-Synthesis Simulation and Testing:
- Conduct post-synthesis simulation and testing to verify that the circuit’s behavior matches the design specifications after synthesis and implementation.
- Timing Analysis:
- Perform timing analysis to ensure that the circuit meets the timing constraints and operates within the desired clock frequency.
Throughout the design process, it is essential to use clear and well-structured VHDL code with proper comments and documentation to enhance readability and maintainability.
What are the types of electronic steering system sensors?
Electronic steering systems, also known as electric power steering (EPS) systems, use various sensors to measure important parameters and provide feedback for precise steering control. The types of sensors commonly used in electronic steering systems include:
- Torque Sensor:
- Torque sensors measure the steering input or torque applied by the driver to the steering wheel. They provide feedback to the EPS controller, allowing it to adjust the steering assistance accordingly.
- Angular Position Sensor:
- Angular position sensors, such as potentiometers or Hall effect sensors, measure the rotational position of the steering wheel. They provide information about the steering wheel’s angle to the EPS controller, enabling it to determine the intended direction of the vehicle.
- Steering Angle Sensor (SAS):
- The SAS is a combination of angular position sensors that precisely measures the steering wheel’s angle and rate of rotation. It provides accurate information about the vehicle’s steering angle, allowing the EPS system to adjust the steering assistance based on the steering wheel’s position.
- Steering Torque Feedback Sensor:
- This sensor measures the torque or force applied to the steering column by the road, providing feedback on road conditions and steering effort to the EPS system. It helps enhance the driver’s steering feel and responsiveness.
- Vehicle Speed Sensor (VSS):
- The VSS measures the vehicle’s speed and provides this information to the EPS controller. The EPS system can use this data to adjust steering assistance at different speeds, improving stability and comfort during high-speed driving or parking maneuvers.
- Yaw Rate Sensor:
- Yaw rate sensors measure the rotational movement around the vertical axis (yaw) of the vehicle. The EPS controller uses this information to understand the vehicle’s lateral dynamics and make steering adjustments for stability control.
- Lateral Acceleration Sensor:
- Lateral acceleration sensors measure the vehicle’s side-to-side acceleration. This data is used by the EPS system to adjust steering assistance and stabilize the vehicle during cornering or sudden maneuvers.
- Steering Speed Sensor:
- The steering speed sensor measures how quickly the steering wheel is being turned. It provides feedback to the EPS system, allowing it to adapt the steering assistance based on the driver’s steering speed.
These sensors work together to provide valuable data to the EPS controller, enabling it to determine the appropriate level of steering assistance based on driving conditions, vehicle speed, steering inputs, and other factors. The integration of these sensors in electronic steering systems helps enhance vehicle safety, responsiveness, and comfort while reducing the driver’s effort required for steering.
What is DPM?
DPM stands for “Digital Panel Meter.” It is an electronic device used to measure and display various electrical parameters, such as voltage, current, resistance, frequency, and other analog signals. DPMs have largely replaced traditional analog panel meters in many applications due to their higher accuracy, versatility, and ease of use.
Key features and characteristics of Digital Panel Meters (DPMs) include:
- Digital Display: DPMs feature a digital display, usually an LED (Light Emitting Diode) or LCD (Liquid Crystal Display), that shows the measured value in numeric form. The digital display provides clear and precise readings compared to the moving needle of analog meters.
- Measurement Accuracy: DPMs offer higher accuracy and resolution than analog meters, making them suitable for precise measurements in various applications.
- Auto-Ranging or Manual Range Selection: Some DPMs have auto-ranging capabilities, where they automatically select the appropriate measurement range based on the input signal. Others require manual range selection for specific applications.
- Multiple Measurement Parameters: DPMs can measure various parameters such as voltage (AC and DC), current, resistance, frequency, temperature, and more, depending on the model and configuration.
- Compact Size: DPMs come in compact form factors, making them suitable for use in tight spaces and panel installations.
- Additional Features: Some DPMs may have additional features like data logging, data hold, peak/minimum/maximum value capture, and communication interfaces for remote monitoring and control.
- Power Supply: DPMs are typically powered by an external power source, often derived from the same circuit they are measuring.
DPMs find applications in a wide range of industries, including electronics, automation, power distribution, process control, and test and measurement. They are commonly used in control panels, industrial equipment, laboratory instruments, and other systems that require accurate and real-time monitoring of electrical parameters.
Overall, DPMs play a vital role in modern electronics and industrial settings, providing engineers, technicians, and operators with essential information about electrical parameters for efficient operation, troubleshooting, and maintenance.
COMMENTS