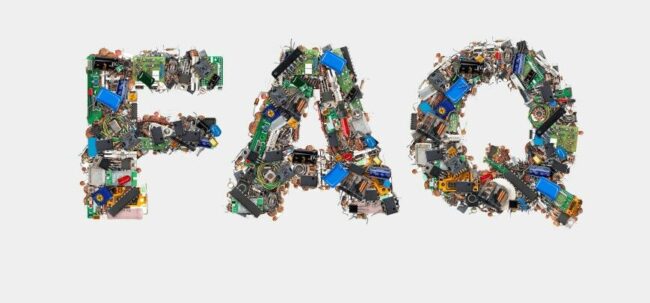
What are the four different modulation formats that fiber optic sensors can be divided into?
Fiber optic sensors are devices that use optical fibers to measure various physical, chemical, or environmental parameters. These sensors can be divided into several modulation formats based on the way they operate and the principles they utilize to measure the target parameter. The four main modulation formats for fiber optic sensors are:
- Intensity Modulation: In this format, the measured parameter affects the intensity of the light propagating through the fiber. The intensity of the light is modulated by changes in the parameter being measured, such as strain, temperature, pressure, or refractive index. The variations in intensity are then correlated with the changes in the parameter. For example, a strain sensor might use a fiber Bragg grating to modulate the light’s intensity based on strain-induced changes in the grating’s periodicity.
- Phase Modulation: In phase modulation, the phase of the light signal traveling through the fiber is modulated by the target parameter. Changes in the measured parameter result in alterations in the phase of the light, which can be detected and correlated to the parameter’s value. Interferometric sensors, such as Mach-Zehnder interferometers or Fabry-Perot interferometers, often employ phase modulation for sensing parameters like pressure or temperature.
- Wavelength Modulation: This format involves changing the wavelength of the light signal in response to variations in the measured parameter. Fiber Bragg gratings are commonly used for wavelength modulation sensors. When strain, temperature, or other environmental factors change, the grating’s spacing or refractive index changes, leading to a shift in the reflected wavelength, which can be used to infer the parameter’s value.
- Polarization Modulation: In polarization modulation sensors, the polarization state of light is modulated based on the parameter being measured. Changes in the parameter alter the polarization of the light signal as it travels through the fiber. These changes can be detected and correlated to the parameter’s value. Polarimetric sensors are a common example of this format, with applications in strain sensing and other environmental measurements.
These different modulation formats offer distinct advantages and disadvantages depending on the specific application and requirements. The choice of modulation format depends on factors such as the sensitivity needed, the measurement range, the accuracy required, and the environmental conditions the sensor will operate in.
What are the characteristics of the Spartan-2E series?
The Spartan-2E series refers to a family of field-programmable gate array (FPGA) devices developed by Xilinx. The Spartan-2E FPGAs are part of the larger Spartan FPGA family and were designed to offer a balance between performance, cost, and power consumption for a range of applications. Please note that my knowledge is based on information available up until September 2021, and I do not have specific details about any updates or developments beyond that date. Here are some general characteristics of the Spartan-2E series:
- Logic Capacity: The Spartan-2E FPGAs are known for their relatively modest logic capacity compared to more advanced FPGA families. They were designed to cater to mid-range applications where moderate logic density is sufficient.
- Configurable Logic Blocks (CLBs): Like other FPGAs, Spartan-2E devices consist of configurable logic blocks (CLBs) that can be programmed to implement various digital logic functions. These CLBs contain lookup tables (LUTs) for logic implementation, flip-flops for storage, and other configurable elements.
- I/O Capabilities: The Spartan-2E series offers a range of I/O pins that can be used to interface with external devices. The number and types of I/O pins available depend on the specific device within the series.
- Clock Management: Spartan-2E FPGAs include clock management resources such as Digital Clock Managers (DCMs) that provide flexible clocking options, phase shifting, and frequency multiplication/division.
- Memory Resources: These FPGAs include block RAM (BRAM) modules that can be used for implementing on-chip memory. The amount of available memory varies depending on the specific device.
- Configuration: Like other FPGAs, Spartan-2E devices are configured using bitstreams that define the functionality of the FPGA’s logic elements and interconnections. These bitstreams are typically generated using design tools provided by Xilinx.
- Power Consumption: The Spartan-2E series aimed to strike a balance between performance and power consumption. While they may not have the lowest power consumption compared to more modern FPGA families, they offered reasonable power efficiency for their time.
- Applications: Spartan-2E FPGAs were used in a variety of applications, including digital signal processing, communication systems, industrial control, and more.
It’s important to note that the Spartan-2E series is older technology, and Xilinx has released more advanced FPGA families since then with greater capabilities and performance. If you’re considering using FPGAs for a project, it’s recommended to check the most recent information available from Xilinx or other FPGA manufacturers to find a series that best suits your requirements.
What is the purpose of the A/D data register?
An A/D (Analog-to-Digital) data register, often simply referred to as an ADC register, is a component found in microcontrollers, microprocessors, and other digital devices that interface with analog sensors or signals. Its primary purpose is to hold the digital representation of the analog voltage or signal that has been converted by an ADC.
Here’s how it works:
- Analog-to-Digital Conversion: Analog sensors and signals produce continuous voltage levels that represent physical quantities such as temperature, pressure, light intensity, etc. However, digital systems, including microcontrollers and processors, operate with discrete digital values. To process analog signals, they need to be converted into digital values using ADCs.
- ADC Conversion: The ADC converts the analog voltage into a digital value that can be processed by the digital circuitry. This conversion involves sampling the analog signal at specific intervals and quantizing the voltage levels into digital bits.
- Storage in the A/D Data Register: After the conversion process, the digital value produced by the ADC is stored in the A/D data register. This register is a specific memory location within the digital device’s memory space dedicated to holding the converted digital value.
- Access and Processing: Once the digital value is in the A/D data register, the digital device’s software can access it. The software can read the value from the register and perform further processing, calculations, decision-making, or any other required actions based on the converted data.
The A/D data register serves as a temporary storage location for the converted analog data before it’s used by the digital system. This separation between the analog world (represented by the sensor’s voltage) and the digital world (where the processing occurs) is a fundamental aspect of interfacing analog and digital systems.
It’s worth noting that the naming and usage of this register might vary depending on the specific microcontroller or microprocessor architecture you are working with. Different manufacturers or architectures might use different terminology or approaches, but the fundamental concept of converting analog signals to digital values and storing them in a register for processing remains consistent.
What are the ways in which message queues work?
Message queues are a form of inter-process communication (IPC) used in computer systems and software applications to enable communication and data exchange between different processes, threads, or components. Message queues operate based on the producer-consumer paradigm, where one process or thread produces data and places it into the queue, and another process or thread consumes the data from the queue. There are various ways in which message queues work, depending on the implementation and the specific features provided by the messaging system. Here are some common ways in which message queues operate:
- Queue-Based Communication:
- In a basic message queue system, a producer process/thread generates messages containing data or instructions.
- The producer places the messages in the message queue, which acts as a buffer or storage for these messages.
- The consumer process/thread retrieves messages from the queue and processes the data or performs the required actions.
- This approach ensures that communication is decoupled, allowing the producer and consumer to work independently and at their own speeds.
- FIFO (First-In-First-Out) Principle:
- Most message queues follow the FIFO principle, meaning that the order in which messages are placed in the queue is the order in which they are consumed.
- The oldest message in the queue is processed first by the consumer.
- Blocking and Non-Blocking Operations:
- Message queue operations can be blocking or non-blocking.
- In blocking operations, if a consumer tries to read from an empty queue, it waits until a message is available. Similarly, if a producer tries to add to a full queue, it waits until space becomes available.
- Non-blocking operations return immediately, even if the queue is empty or full. This can be useful for scenarios where waiting is not desirable.
- Message Priority:
- Some message queue systems support message prioritization.
- Messages with higher priority are processed before messages with lower priority, regardless of their order in the queue.
- Synchronous and Asynchronous Communication:
- Message queues can facilitate both synchronous and asynchronous communication.
- In synchronous communication, the producer waits for the consumer to process the message and potentially respond before continuing.
- In asynchronous communication, the producer doesn’t wait for immediate processing by the consumer and can continue its own work.
- Buffering and Flow Control:
- Message queues provide buffering capabilities, allowing producers and consumers to operate at different rates without causing data loss.
- Buffering helps manage the flow of data between fast and slow processes, preventing data overload or starvation.
- Persistence:
- Some message queue systems offer message persistence, where messages are stored even if the system or application restarts.
- This ensures that important messages are not lost in the event of a failure.
- Message Format and Metadata:
- Messages placed in the queue typically have associated metadata, including identifiers, timestamps, and possibly message types.
- The queue system may also provide serialization and deserialization mechanisms to handle message data in a consistent format.
The specifics of how message queues work can vary based on the messaging system or framework being used. Popular message queue technologies include RabbitMQ, Apache Kafka, Amazon SQS, and various others, each offering different features and trade-offs to meet specific communication requirements.
What is the format of the instruction?
The format of an instruction refers to the structure and organization of a machine-level instruction in a computer’s instruction set architecture (ISA). An instruction is a binary representation of a command that the computer’s central processing unit (CPU) can execute. Different ISAs can have varying instruction formats, but there are several common formats that instructions tend to follow. The format of an instruction typically includes fields that convey information about the operation to be performed and the operands involved. Here are some common instruction formats:
- Single Accumulator Format:
- This format is used by some early computers and microcontrollers.
- It has a single accumulator register that is implicitly used for operations.
- The instruction only needs an opcode field to specify the operation to be performed.
- Example: ADD, SUB, MUL
- Memory-Register Format:
- This format involves an opcode field, one or more register fields, and a memory address field.
- The registers specified in the instruction participate in the operation.
- Example: MOV R1, [A]
- Register-Register Format:
- In this format, an opcode field and multiple register fields are present.
- The operation is performed between two registers specified in the instruction.
- Example: ADD R1, R2, R3
- Immediate Format:
- This format includes an opcode field, a register field, and an immediate value field.
- The immediate value is a constant that is used in the operation.
- Example: ADD R1, R2, #5
- Jump Format:
- Jump instructions have an opcode field and a target address field.
- They are used for branching and altering the program flow.
- Example: JMP LABEL
- Complex Format:
- Some ISAs have more complex instruction formats with multiple opcode fields, multiple register fields, immediate values, and memory address fields.
- These formats allow for a wide range of operations and operand types.
- Example: ARM Thumb instruction set
- Variable-Length Format:
- Some ISAs use variable-length instructions, where the length of the instruction can vary depending on the operation and operands.
- This allows for a more compact encoding but can complicate instruction fetching.
- Example: x86 instruction set
- Vector Format:
- Modern processors often support SIMD (Single Instruction, Multiple Data) operations.
- Vector instructions operate on multiple data elements in parallel.
- These instructions have special formats to handle vector registers and data.
It’s important to note that the actual binary structure of instructions can vary significantly between different architectures and instruction sets. The format of an instruction is defined by the ISA and dictates how the CPU interprets and executes the instruction. Understanding the instruction format is essential for software developers and hardware designers working with low-level programming and computer architecture.
What are the parts for contact IC cards?
Contact Integrated Circuit (IC) cards, commonly known as smart cards, are a type of plastic card embedded with an integrated circuit chip. These cards are widely used for various applications, including identification, authentication, payment systems, access control, and more. A contact IC card consists of several essential components that work together to enable communication and data exchange between the card and external devices. The main components of a contact IC card are as follows:
- Plastic Card Body: The physical body of the smart card is typically made of plastic, providing durability and protection for the embedded components.
- Integrated Circuit (IC) Chip: The heart of the contact IC card is the integrated circuit chip. This chip contains a microprocessor or microcontroller, memory, and other circuitry for processing data and executing instructions. The chip is responsible for executing commands, storing data, and performing cryptographic operations.
- Contact Pads: These are metallic contacts on the surface of the card that establish a physical connection between the IC chip and external devices. When the card is inserted into a card reader, these contact pads provide the electrical interface for communication.
- Memory: The IC chip includes various types of memory, such as Read-Only Memory (ROM), Random-Access Memory (RAM), and Electrically Erasable Programmable Read-Only Memory (EEPROM). ROM contains the card’s operating system and application code, while RAM is used for temporary data storage during card operations. EEPROM is non-volatile memory that stores user data, cryptographic keys, and other persistent information.
- Microprocessor/Microcontroller: The microprocessor or microcontroller on the IC chip is responsible for executing commands, processing data, and controlling the card’s operations. It acts as the card’s “brain.”
- Clock and Oscillator: A clock circuit generates the necessary timing signals for the IC chip’s operations. This ensures that operations occur at the correct timing and synchronization.
- Security Features: Many contact IC cards include security features to protect the stored data and prevent unauthorized access. These features can include hardware-based encryption, secure storage for cryptographic keys, and secure execution environments.
- Application-Specific Data: Contact IC cards can store various types of application-specific data, depending on their intended use. For example, a payment card may store account information, while an access control card may store user credentials.
- Operating System: The card’s operating system manages the execution of commands, memory access, and communication with external devices. It provides a standardized interface for accessing the card’s capabilities.
- Electrical Protection: Contact IC cards may include components to protect against electrical surges, electromagnetic interference, and other external factors that could damage the IC chip.
When a contact IC card is inserted into a card reader, the contact pads establish an electrical connection, allowing the card reader to communicate with the IC chip. The reader sends commands to the card, and the card responds by executing the requested operations or providing the requested data. The communication follows specific protocols defined by the card’s operating system and supported by the reader.
What are the three steps that the control process of a computer control system usually comes down to?
The control process of a computer-based control system typically involves three fundamental steps: measurement, comparison, and action. These steps are part of a feedback control loop that continuously monitors a system’s performance, compares it to a desired state, and makes adjustments as necessary to maintain or achieve the desired outcome. Here’s a breakdown of each step:
- Measurement: In the measurement step, the control system acquires data from sensors or measurements that provide information about the current state or performance of the controlled system. These sensors capture relevant parameters such as temperature, pressure, position, velocity, or any other relevant variables.
- Comparison: Once the measurement data is obtained, the control system compares the actual measured values to a reference or desired setpoint. The reference value represents the desired state or behavior that the system should achieve. The comparison determines the error, which is the difference between the measured value and the desired setpoint.
- Action: Based on the comparison between the measured value and the desired setpoint, the control system takes corrective action to minimize the error and bring the system closer to the desired state. This action involves applying control signals or commands to actuators, devices that manipulate the system’s behavior. Actuators can change system parameters such as speed, position, temperature, or any other controlled variables.
The control loop continuously iterates through these three steps to maintain the controlled system’s performance within acceptable limits and to achieve the desired outcomes. The goal is to regulate the system’s behavior, correct deviations from the desired state, and adapt to changes in operating conditions.
This feedback control process is a fundamental concept in various fields, including engineering, automation, robotics, process control, and more. It enables precise and efficient control of systems in various applications, from temperature regulation in HVAC systems to the autonomous control of vehicles.
What function blocks are each macro unit made up of?
Each macrocell consists of three functional blocks: a logic array, a product term selection matrix, and a programmable flip-flop.
What are the characteristics of Altera’s MAX II?
- Logic Capacity: MAX II devices come in various sizes, offering a range of logic capacity to accommodate different levels of complexity in digital designs.
- Low Power Consumption: One of the key features of MAX II devices is their low power consumption. They are designed to be power-efficient, making them suitable for battery-powered or power-sensitive applications.
- Flash-Based Configuration: MAX II devices use non-volatile flash memory for configuration storage. This means that the configuration data is retained even when the device loses power, allowing for “instant-on” operation when power is restored.
- I/O Flexibility: MAX II devices offer a variety of I/O standards and options, allowing designers to interface with different types of external devices and systems.
- Embedded Memory: Some MAX II devices include on-chip memory resources such as M9K memory blocks, which can be used for implementing memory elements in your design.
- MultiVolt I/O: Some members of the MAX II family offer support for multi-voltage I/O standards, which allows interfacing with devices operating at different voltage levels.
- In-System Programming (ISP): MAX II devices support in-system programming, enabling users to reconfigure the devices while they are in the application circuit, without the need for external programmers.
- Hierarchical Design Support: MAX II devices support hierarchical design methodologies, allowing designers to break down complex designs into manageable modules.
- Design Security: Some MAX II devices offer security features like JTAG security and user-level security to protect your intellectual property and sensitive data.
- Development Tools: Altera provides design software tools, such as Quartus II, that allow designers to compile, simulate, and program MAX II devices.
- Applications: MAX II devices are used in a variety of applications including consumer electronics, industrial control systems, communications equipment, automotive electronics, and more.
Keep in mind that the specific features and characteristics of MAX II devices may vary based on the particular model and package you are considering. If you’re considering using MAX II devices for a project, it’s recommended to consult the latest documentation and resources from Altera (now part of Intel) to get the most up-to-date and accurate information.
What are the two methods of oscillating frequency versus noise reduction?
The two methods for reducing noise in an oscillating frequency are dithering and spread spectrum modulation. These methods are often used in electronic circuits to mitigate the effects of electromagnetic interference (EMI) and improve the overall performance of oscillators, particularly in applications where low noise and stable frequency are essential.
- Dithering: Dithering involves intentionally introducing a small, random noise signal to the control input of an oscillator. This noise disrupts the regular frequency oscillation of the oscillator, causing its frequency to fluctuate slightly around the desired frequency. The advantage of dithering is that it helps spread the energy of the oscillator’s signal over a wider frequency range, making it less susceptible to interference from narrowband noise sources. However, the output frequency distribution becomes broader due to the noise injection. This technique is commonly used in applications where reducing phase noise is critical.
- Spread Spectrum Modulation: Spread spectrum modulation is a technique where the frequency of the oscillator is modulated by a pseudorandom sequence. This modulation spreads the energy of the oscillator’s output signal across a broader frequency band. There are two main types of spread spectrum modulation: direct sequence spread spectrum (DSSS) and frequency hopping spread spectrum (FHSS).
- DSSS: In DSSS, the carrier frequency of the oscillator is modulated directly by a pseudo-noise sequence. This technique increases the bandwidth of the signal, which helps in reducing the effects of interference and noise. DSSS is often used in wireless communication systems.
- FHSS: In FHSS, the carrier frequency of the oscillator is rapidly changed over a sequence of predefined frequencies. This hopping behavior makes it difficult for external sources of interference to affect the communication link consistently. FHSS is used in applications where robustness against interference is crucial, such as wireless networks and Bluetooth.
Both dithering and spread spectrum modulation can be effective in reducing the impact of noise and interference on oscillating frequencies. The choice between these methods depends on the specific requirements of the application and the trade-offs between frequency stability, noise reduction, and signal bandwidth.
COMMENTS