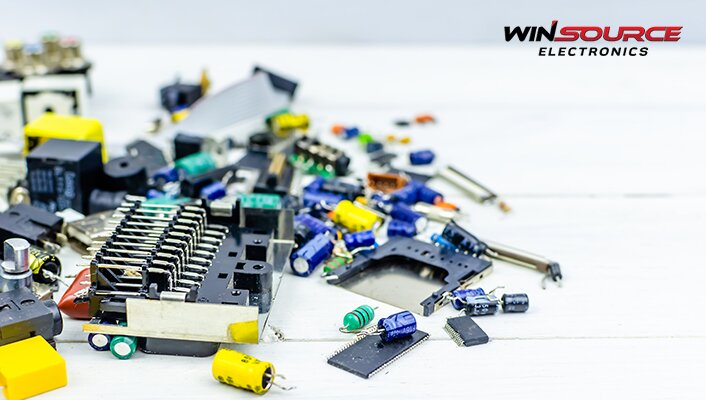
If you are the hardware design engineer of an NPI (=New product introduction) team, or you are part of the project team, such as an NPI buyer – and you are creating great new products for your company:
From this point, part obsolescence is soooo far away, that you usually not spending a second on thinking about component obsolescence, or at least lifecycle, right? (be honest to yourself…)
Well, the components are not old at the moment of release, but they will get old. Promised.
So, what to do, and how to do it right?
Perform a BOM check:
It is crucial that your new bill of material is looked at and examined in deep detail by the sourcing people.
When:
1 second after pulling a new component into your electronic design entry system. Not kidding! Read more below on this.
Table of Contents
ToggleCheck 1: Check for lifecycle
Goes without saying, that the components you have selected will be on the market for a while. How long? This is depending on your products: Are you producing a “one-off” Christmas geek or industrial products being in production for 20 years.
By the way: Consider professional solutions helping you to check all your components like AMSYS, doing this permanently and reliably.
Check 2: Qualify second sources
How often did you hear this statement: “well, we are under time pressure. We have qualified one single capacitor only, and we will qualify second sources later”. If you are honest to yourself, “later” is a nice word for “never”. It is never so easy and feasible to qualify more sources for one CPN (=company part number) than in design phase – you have all the test setup handy, so in best case, it is just a “exchange the cap and press the start-test button again”. Put yourself into the shoes of your buyers: You do the work only once, but your buyers have to purchase the components over and over again the next 20 years. Plus: It is also less work for you over time: If a sole sourced component gets obsolete: you have work ☹. If you gave procurement a plan B and plan C, means: more manufacturer parts released under one CPN: no work for you 😊
Check 3: Check for preferred parts
Do not think about new components never been used in your company here. Think about the 80-90% of components in your BOM, existing in your company already – it is usually a good idea to re-use. BUT: A big company might have 10.000’s of company part numbers, linked in the AMPL (approved manufacturer part list) to another 20.000’s of manufacturer part numbers. Your production and procurement might like some of them, and they might want to get rid of some others as soon as possible.
If your company is really professional, each single CPN is rated as PARDO(n):
- Preferred
- Accepted
- Restricted
- Do not use
- Not rated (should not be the case)
The choice to make is a team sport between all functions:
- Engineering or quality: might rate a part down because it is not reliable
- Sourcing: might like cheap parts with good availability. By the way: Do you know WIN-SOURCE.net ?
- Production: surely likes parts being trouble-free in the manufacturing process, likes to kick out components that don’t solder well, that are “doubles” occupying lots of feeders at the pick & place machine, like MiniMelf versus 1206 versus 0805 versus… you know the story.
It is almost impossible to kick out “do not use” parts as a separate project, as you have to touch up too many existing designs. So, the only way to improve your set of components is to select them very carefully for a new design. In other words: cleaning your parts portfolio is not a sprint, it is a marathon. And it takes place at the moment of design-in.
Having that said, new designs must contain only preferred parts, do you agree? What preferred means: Ask your different business functions, it will be an interesting discussion hopefully leading to a solid and company wide definition.
Check 4: short time part availability
Make sure you are getting enough sample components to finish your design work PLUS to ramp up without delays into mass production.
As long as the product is not released yet, and you are in design phase still: Honestly, the most important thing is lead time. Do not let your NPI people wait for a component, delaying the entire project just because one single operational amplifier is missing. My recommendation: Check out for win-source.net
When I said: A hardware design engineer should know one second after placing it into the new schematic if it is a good or bad one, I meant this seriously. The earlier it is clear: This specific component will cause trouble in sourcing, in function, in second sourcing or whatever: The better.
Once the printed circuit board was layouted and the first test begun, it is far too late. Each NPI engineer might agree, that changing a selected component later than at the moment of first entry into schematics, would be a delay in the project by weeks or even months and so impossible to exchange, even if the part is a real bad one.
Conclusion: Your design entry system must be digitally connected to your AMPL, your PARO rating system and in close contact to your other functions. This is a longer story and worth another article.
Takeaway
The moment in which the NPI engineer picks a component first time is crucial. Examine the part in this moment, not later! Check for lifecycle, obsolescence, multiple sources instantaneously. It will be too later afterwards.
Have a good distributor in place which avoids delays in NPI projects and production ramp up, such as Win-Source.net
Last not least: Let me help you. Just call. Volker from VECE-consulting.com
COMMENTS