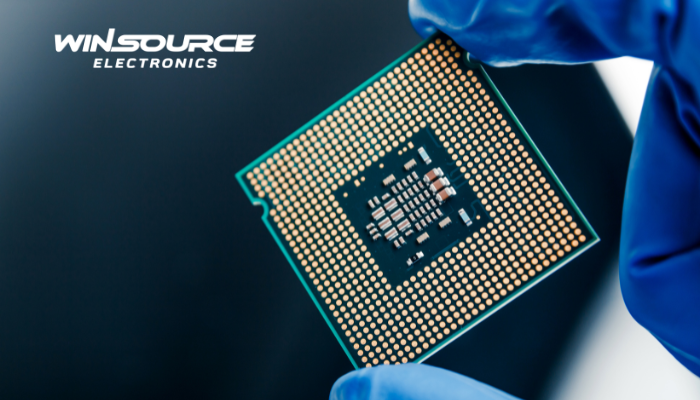
* Question
How to apply single-chip microcomputer in automotive electronic control system?
* Answer
Applying a single-chip microcomputer (also known as a microcontroller or MCU) in automotive electronic control systems involves several steps and considerations. Here’s a general guide on how to implement MCUs in automotive applications:
1. Understand the Application Requirements
Identify the specific functions that the MCU will control, such as engine management, transmission control, braking systems, or infotainment systems.
2. Select an Appropriate MCU
Choose an MCU that meets the requirements of your application. Consider the following factors:
– Processing power and speed
– Memory (RAM and ROM) requirements
– Input/Output (I/O) capabilities
– Communication interfaces (CAN, LIN, Ethernet, etc.)
– Operating temperature range
– Automotive-specific standards (such as AEC-Q100 qualification)
3. Develop the System Architecture
Define the architecture of the electronic control system:
– Determine the sensors and actuators that will interface with the MCU.
– Design the power supply and voltage regulation circuits.
– Plan the communication network within the vehicle (e.g., CAN bus).
4. Design and Prototype the Circuit
Create a schematic and PCB layout for the system:
– Use appropriate EDA tools for circuit design and simulation.
– Ensure proper layout practices to minimize noise and interference.
– Prototype the circuit on a development board or custom PCB.
5. Write the Firmware
Develop the software that will run on the MCU:
– Write drivers for interfacing with sensors, actuators, and communication protocols.
– Implement control algorithms (e.g., PID controllers for engine management).
– Develop safety and diagnostic features (such as fail-safe modes and error detection).
6. Test and Validate the System
Perform rigorous testing to ensure the system meets all functional and safety requirements:
– Conduct bench testing to validate the hardware and firmware.
– Perform in-vehicle testing to evaluate real-world performance.
– Use automated testing tools to verify compliance with automotive standards.
7. Optimize and Finalize the Design
Refine the system based on test results:
– Optimize the firmware for performance and efficiency.
– Make any necessary hardware adjustments to improve reliability and robustness.
– Ensure the system meets all regulatory and compliance standards for automotive applications.
8. Production and Deployment
Prepare the system for mass production:
– Finalize the design and prepare manufacturing documentation.
– Work with suppliers to source components and manufacture PCBs.
– Implement quality control measures to ensure consistent product quality.
Example Application: Engine Control Unit (ECU)
An example of using an MCU in an automotive electronic control system is in an Engine Control Unit (ECU):
– Sensors: The MCU interfaces with various sensors (e.g., temperature, pressure, oxygen) to monitor engine parameters.
– Actuators: The MCU controls actuators such as fuel injectors, ignition coils, and throttle position.
– Control Algorithms: The MCU runs algorithms to optimize engine performance, fuel efficiency, and emissions.
– Communication: The MCU communicates with other ECUs in the vehicle via the CAN bus to ensure coordinated operation.
By following these steps and considerations, you can effectively integrate a single-chip microcomputer into an automotive electronic control system, ensuring reliable and efficient operation.
COMMENTS