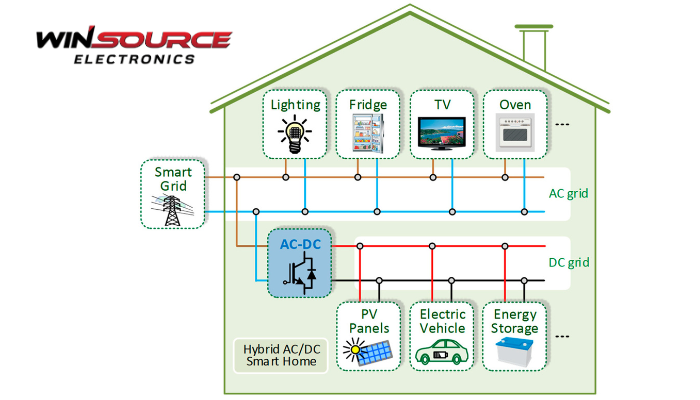
* Question
In essence, what are the potential voltage and current conditions at the front end of the power conversion system?
* Answer
In the context of the front end of a power conversion system, the voltage and current conditions refer to the input parameters that will be processed by the power supply or converter before converting them to the desired output voltage and current. These conditions can vary depending on the type of system, application, and specific power requirements, but typically include the following:
1. Voltage Conditions:
– Input Voltage Range: The front-end of a power conversion system typically handles a wide input voltage range to accommodate various power sources. This could be:
– AC Input Voltage: Often in the range of 100V to 240V AC for general-purpose systems, or higher for industrial systems (e.g., 380V AC).
– DC Input Voltage: For systems using DC sources (e.g., batteries, solar panels), the input voltage might range from 12V DC to 48V DC, or even higher depending on the application.
– AC Line Variability: The AC voltage may vary due to grid fluctuations, typically between ±10% of the nominal value, and power conversion systems must handle this variability.
– Voltage Surges and Transients: The input voltage may experience surges, spikes, or transients (e.g., due to lightning strikes or switching events), so front-end circuits must protect against these, typically using surge suppressors or varistors.
2. Current Conditions:
– Input Current: The current drawn at the front end is based on the input voltage and the power demand of the system. The current can vary widely, and factors to consider include:
– For AC-powered systems, the rms current is determined by the input power and voltage.
– For DC-powered systems, the input current is related to the load power and input voltage, following the formula:
I = P/V
where P is power and V is voltage.
– Startup Inrush Current: When the power system is powered on, there may be a significant inrush current due to charging capacitors, magnetizing transformers, or other components. This inrush must be limited using NTC thermistors, soft-start circuits, or other techniques.
– Current Ripple: The input current may contain ripple or harmonic content, especially in systems with switching regulators (e.g., buck converters). High ripple can affect the overall efficiency and stability of the power conversion system.
3. Power Factor (for AC Input):
– Power Factor Correction (PFC): For AC input systems, particularly in high-power or industrial applications, power factor correction is used to ensure that the system operates efficiently and minimizes the reactive power. A poor power factor can result in higher losses and voltage instability.
– Power factor is a measure of how effectively the system uses the input power and is typically corrected to be near 1 (ideal).
4. Impedance Matching (for DC Systems):
– Source Impedance: In DC-powered systems, the impedance of the power source (e.g., battery, solar panel) influences the voltage and current at the front end. The converter may need to adjust for source impedance variations to ensure stable operation.
5. Power Quality:
– The quality of the input power (especially AC) is critical. Front-end circuits must handle voltage sags, dips, and harmonics to maintain stable conversion performance.
Summary of Conditions:
– Input Voltage: Can range from 100V AC to 240V AC for standard systems, or 12V DC to 48V DC for DC-powered systems, with tolerance for surges and fluctuations.
– Input Current: Varies based on the input power demand; may include startup inrush and current ripple.
– Power Factor: AC systems often employ PFC to correct for reactive power.
– Impedance: DC systems need to manage source impedance to ensure stable operation.
In essence, the front-end of a power conversion system must accommodate varying input voltages, handle transient conditions, manage current ripple, and ensure efficient power conversion through techniques like PFC and protection mechanisms.
COMMENTS