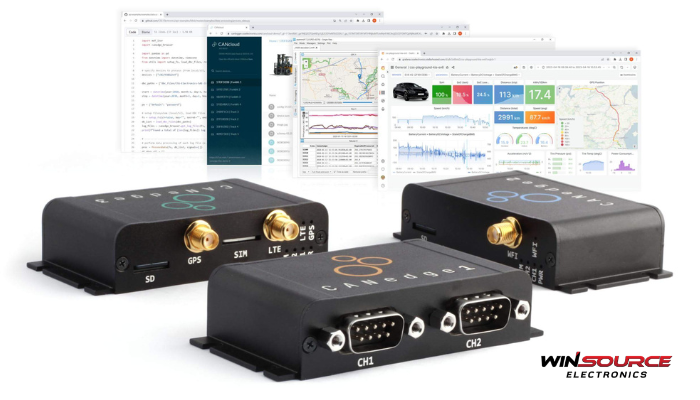
* Question
What control functions can the CAN bus data acquisition communication node software design implement?
* Answer
The CAN (Controller Area Network) bus is a robust vehicle bus standard designed to allow microcontrollers and devices to communicate with each other within a vehicle without a central host computer. The software design for a CAN bus data acquisition communication node can implement various control functions, which are pivotal in automotive and industrial applications. Here are some of the key control functions that can be implemented:
1. Data Collection and Monitoring:
– Continuously monitor and collect data from various sensors and devices on the CAN network such as temperature sensors, pressure sensors, speed sensors, and engine performance metrics.
– Process and filter the data for noise and errors to ensure accurate readings are available for analysis.
2. Real-Time Diagnostics:
– Implement diagnostic protocols to detect and report faults or anomalies in the network or connected devices.
– Provide real-time feedback on system performance and alert operators or other systems to potential issues.
3. Error Handling and Fault Isolation:
– Detect, log, and isolate errors on the CAN bus to prevent them from affecting the entire network.
– Automatically reset or reconfigure nodes that are showing continuous errors to maintain network stability.
4. Event-Driven Actions:
– Trigger actions based on specific events or conditions detected on the network. For example, adjusting engine parameters based on temperature readings or activating safety features under certain conditions.
5. Message Filtering and Prioritization:
– Manage the flow of messages by filtering and prioritizing them based on predefined rules, ensuring critical data is transmitted and processed first.
– Reduce network congestion and improve the efficiency of data communication by controlling the rate and priority of messages.
6. Control Command Execution:
– Execute specific control commands received from other nodes or controllers, such as starting/stopping a motor, opening/closing valves, or adjusting light settings.
– Ensure that these commands are executed within safe operating parameters and provide feedback on their status.
7. Synchronization of Multiple Nodes:
– Coordinate activities and data sharing among multiple nodes on the CAN network to perform complex operations synchronously.
– Ensure all nodes operate in harmony, particularly in systems where timing and sequence of operations are critical.
8. Data Logging and Storage:
– Store data collected on the network for later analysis and record-keeping.
– Implement efficient data management practices to handle large volumes of data over time.
9. Security Measures:
– Implement security protocols to safeguard the communication on the CAN network against unauthorized access and data tampering.
– Use encryption, authentication, and secure key management to protect sensitive data.
By integrating these control functions, the CAN bus data acquisition communication node can effectively manage and monitor complex systems, enhance operational efficiency, and ensure safety and reliability in automotive or industrial environments.
COMMENTS