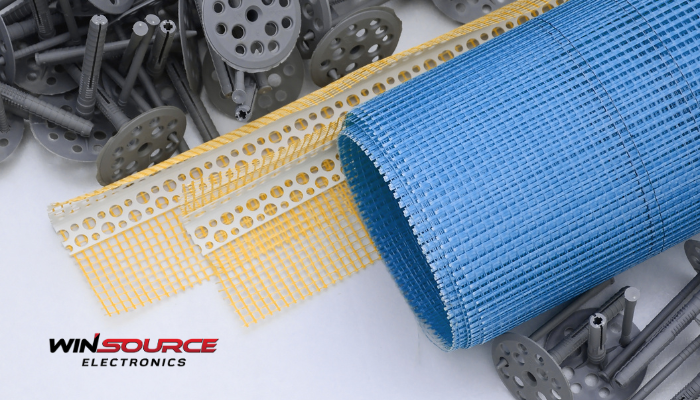
* Question
What properties should the material of the protective sleeve have?
* Answer
When selecting a material for a protective sleeve, several key properties should be considered to ensure that the sleeve performs effectively in protecting the underlying components or wires. Here are the primary properties that the material should have:
1. Durability:
– Mechanical Strength: The material should be able to withstand physical wear and tear, including abrasion, impact, and tension.
– Tear Resistance: It should resist tearing under stress and maintain its integrity over time.
2. Flexibility:
– Bendability: The material should be flexible enough to bend and conform to various shapes and contours without cracking or breaking.
– Elasticity: It should return to its original shape after bending or stretching.
3. Thermal Resistance:
– Heat Resistance: The material should withstand high temperatures without degrading or melting, especially if used in environments with significant heat exposure.
– Cold Resistance: It should also maintain flexibility and performance at low temperatures without becoming brittle.
4. Chemical Resistance:
– Corrosion Resistance: The material should resist corrosion and degradation from exposure to chemicals, oils, solvents, and other corrosive substances.
– UV Resistance: If used outdoors, the material should be resistant to ultraviolet (UV) radiation to prevent degradation from sun exposure.
5. Electrical Insulation:
– Dielectric Strength: The material should have good insulating properties to prevent electrical shorts and protect against electrical shocks.
– Non-conductivity: It should not conduct electricity to ensure the safety of the wires or components it is protecting.
6. Water and Moisture Resistance:
– Waterproofing: The material should be impermeable to water and moisture to protect the underlying components from corrosion and short circuits.
– Moisture Barrier: It should prevent moisture from penetrating and affecting the protected components.
7. Flame Retardancy:
– Fire Resistance: The material should be flame-retardant to prevent it from catching fire and to provide an additional layer of safety in case of exposure to sparks or flames.
8. Environmental Resistance:
– Weather Resistance: The material should withstand various environmental conditions, including rain, snow, wind, and sun, without degrading.
– Fungus and Mold Resistance: It should resist growth of fungus and mold, which can be important in humid or damp environments.
9. Ease of Installation and Maintenance:
– Ease of Application: The material should be easy to apply, remove, and replace if necessary.
– Maintenance: It should require minimal maintenance and be easy to clean if needed.
10. Cost-effectiveness:
– Affordability: The material should be cost-effective, providing the necessary protection without being prohibitively expensive.
– Availability: It should be readily available in the required quantities and sizes.
Materials commonly used for protective sleeves that meet these criteria include nylon, polyester, silicone, rubber, and polyethylene, among others. Each material has its specific advantages and is chosen based on the particular application requirements.
COMMENTS