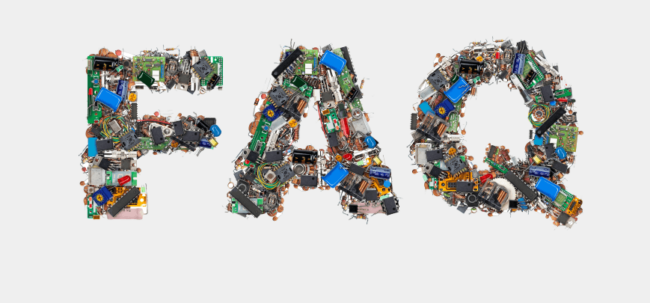
What are the design of the unit circuit in the digital circuit?
The design of a unit circuit in a digital circuit depends on its specific function and purpose within the overall system. A digital circuit typically consists of logic gates, flip-flops, registers, and other digital components that perform specific tasks in processing binary data.
Here are some common unit circuit designs used in digital circuits:
- Logic Gates: Logic gates are the building blocks of digital circuits. They include basic gates like AND, OR, NOT, and more complex gates like XOR, NAND, NOR. These gates perform logical operations on binary inputs to produce binary outputs based on the truth table of each gate.
- Adders and Subtractors: Adders and subtractors are used to perform arithmetic operations in digital circuits. A full-adder circuit can add two binary numbers, while a subtractor circuit can subtract one binary number from another.
- Multiplexers and Demultiplexers: Multiplexers are used to select one of several input signals and forward it to the output, based on a control input. Demultiplexers do the opposite; they take a single input and direct it to one of several output lines.
- Shift Registers: Shift registers are used to store and shift binary data. They are often used for serial-to-parallel or parallel-to-serial data conversion, as well as for time delay applications.
- Counters: Counters are used to generate sequences of binary numbers. They can be designed as up-counters, down-counters, or bidirectional counters, depending on the requirements.
- Decoders and Encoders: Decoders take binary inputs and activate specific output lines based on the binary value of the input. Encoders do the reverse; they take multiple inputs and convert them into a binary code representing the active input.
- Memory Elements: Memory elements like flip-flops and registers are used to store binary data in digital circuits. They are essential for temporary storage and data processing in sequential logic circuits.
- Control Units: Control units are responsible for managing the sequencing and timing of operations in a digital system. They generate control signals to coordinate the activities of other components in the circuit.
The design of each unit circuit involves understanding the required functionality, determining the appropriate combination of logic gates and components, and ensuring proper timing and synchronization in the circuit. In complex digital systems, these unit circuits are combined to create more intricate functionalities, such as CPUs, microcontrollers, and other digital devices.
What is the working principle of solid state relays?
The working principle of solid-state relays (SSRs) is based on the use of semiconductor components, such as thyristors or transistors, to switch and control the flow of electric current. Unlike traditional electromechanical relays, SSRs have no moving parts, which makes them more reliable, durable, and faster in operation.
The basic working principle of an SSR involves using an input control signal to activate the semiconductor switch, which in turn allows current to flow through the output circuit. Here’s a step-by-step explanation of how SSRs work:
- Input Control Signal: SSRs are controlled by low-power input signals, typically from microcontrollers, logic circuits, or digital control systems. The input signal can be a DC voltage or a digital signal, depending on the type of SSR.
- Opto-Isolation (Optional): Many SSRs incorporate opto-isolation, which uses an optocoupler to electrically isolate the input and output circuits. The input signal activates an LED in the optocoupler, which in turn triggers the semiconductor switch in the output circuit.
- Gate Triggering: The semiconductor switch in the SSR can be a thyristor (SCR), a triac, or a power transistor (MOSFET or IGBT). When the appropriate input signal is applied, the gate of the semiconductor switch is triggered, allowing current to flow through the device.
- Conducting State: Once the semiconductor switch is triggered, it enters a conducting state, acting as a closed switch, and allows current to flow through the output circuit. In the case of AC SSRs, the semiconductor switch turns on and off periodically with each zero-crossing of the AC waveform.
- Off State: When the input control signal is removed or changes state, the semiconductor switch turns off, acting as an open switch, and stops the flow of current in the output circuit.
The advantages of SSRs stem from their solid-state nature, which eliminates mechanical wear and tear, provides silent operation, and enables faster response times. Additionally, SSRs have excellent electrical isolation between the input and output circuits, making them ideal for applications where galvanic isolation is required.
Solid-state relays are commonly used in various applications, including industrial automation, motor control, heating and cooling systems, lighting control, power distribution, and in any situation where fast and reliable switching of electrical loads is needed.
What is the working principle of the D/А converter?
The working principle of a Digital-to-Analog Converter (D/A or DAC) is to convert digital data into analog signals. In digital systems, data is represented in discrete binary values (0s and 1s), whereas analog signals are continuous and vary smoothly with time. The D/A converter bridges this gap by translating digital data into a corresponding analog voltage or current level.
Here’s a step-by-step explanation of how a typical D/A converter works:
- Digital Input: The D/A converter receives a digital input, which is a binary representation of the desired analog signal. The digital input can be in the form of binary numbers or digital codes, with each bit representing a different amplitude level.
- Reference Voltage or Current: The D/A converter requires a reference voltage or current against which the digital input will be compared. This reference voltage or current sets the maximum range of the analog output that the D/A converter can produce.
- Binary Weighting: Each bit of the digital input has a different binary weighting, determined by its position in the binary number. The most significant bit (MSB) has the highest weighting, followed by the next bit, and so on. The binary weighting represents the analog value corresponding to each bit position.
- Digital-to-Analog Conversion: The D/A converter uses the binary weighting of each bit to generate an analog voltage or current. It does this by controlling a set of switches or resistors based on the state of each bit. When a bit is “1,” the corresponding switch or resistor is activated, contributing its binary weighting to the final analog output. When a bit is “0,” the switch or resistor is deactivated, and its contribution is ignored.
- Summation: The analog values from each bit are summed together to produce the final analog output. The analog output represents the continuous voltage or current level that corresponds to the digital input.
- Output Buffering: The analog output may go through an output buffer or amplifier to provide the required current or voltage levels to drive the external load or interface with other components in the system.
The accuracy and performance of a D/A converter depend on factors such as the resolution (the number of bits in the digital input), the accuracy of the reference voltage/current, and the quality of the analog output circuitry.
D/A converters find extensive use in various applications, including audio systems, communication systems, instrumentation, control systems, and any situation where digital data needs to be converted into analog signals for processing, monitoring, or actuation purposes.
What aspects should be considered in the overall design of the automotive electronic control unit?
The overall design of an automotive Electronic Control Unit (ECU) is a crucial and complex process that requires careful consideration of various aspects to ensure the functionality, reliability, and safety of the system. Here are some important aspects that should be considered in the overall design of the automotive ECU:
- System Requirements: Clearly define the system requirements and functionalities of the ECU. Understand the intended purpose and performance specifications to meet the specific needs of the automotive application.
- Safety and Reliability: Automotive ECUs play critical roles in safety-critical systems such as engine control, braking, and airbag deployment. Implement redundant and fail-safe design techniques to ensure high reliability and safety compliance.
- Environmental Considerations: Automotive ECUs must be designed to withstand harsh environmental conditions, including temperature variations, vibration, humidity, and exposure to chemicals and fluids.
- Electromagnetic Compatibility (EMC): Ensure the ECU’s design is immune to electromagnetic interference and does not emit excessive electromagnetic radiation that could interfere with other vehicle systems.
What are the types of dipole UHF RFID tag antennas?
UHF RFID tag antennas are essential components in radio frequency identification (RFID) systems that operate in the ultra-high frequency (UHF) range. Dipole antennas are a common type of UHF RFID tag antennas due to their simplicity, cost-effectiveness, and good performance characteristics. There are two main types of dipole UHF RFID tag antennas:
- Linear Polarized Dipole Antennas: Linear polarized dipole antennas are the most commonly used type in UHF RFID applications. They consist of two straight conductive elements (arms) placed parallel to each other, with a small gap between them. The length of each arm is typically half of the wavelength of the UHF frequency used. These antennas emit radio waves in a single plane, creating a directional radiation pattern with a strong signal in one direction and weaker signal levels in other directions. Linear polarized antennas are suitable for applications where the orientation of the tag and reader relative to each other can be controlled or predicted.
Advantages:
- Longer read range compared to some other types of UHF RFID tag antennas.
- Provides better performance in line-of-sight conditions.
Disadvantages:
- Sensitivity to tag orientation, which may lead to reduced performance when tags are not optimally aligned with the reader.
- Circular Polarized Dipole Antennas: Circular polarized dipole antennas are designed to emit radio waves in a circular pattern, which allows for greater flexibility in tag orientation compared to linear polarized antennas. They use additional circuitry to generate circular polarization, usually through the addition of a phase-shifting network. Circular polarization helps improve read rates and tag readability in situations where the tag orientation cannot be controlled, such as in retail environments where tags may be randomly oriented on products.
Advantages:
- More tolerant to tag orientation, allowing for better performance in environments with multiple tags or where tag orientation is unpredictable.
- Improved read rates and coverage in multipath and dense tag environments.
Disadvantages:
- Slightly reduced read range compared to linear polarized antennas.
Both types of dipole UHF RFID tag antennas have their unique advantages and are selected based on the specific application requirements. Linear polarized antennas are commonly used in applications where tag orientation can be controlled, such as in manufacturing or logistics. On the other hand, circular polarized antennas are preferred in applications with complex tag orientations or environments with a high density of tags, such as in retail inventory management or race timing systems.
What are the features of the MC9S08DZ60 series?
The MC9S08DZ60 series is a family of 8-bit microcontrollers (MCUs) from NXP Semiconductor (formerly Freescale Semiconductor, now part of NXP). These microcontrollers are part of the S08D family and are designed for various embedded control applications. The MC9S08DZ60 series offers a range of features suitable for a wide range of applications. Here are some key features of the MC9S08DZ60 series:
- 8-bit S08 CPU Core: The MC9S08DZ60 series is built around an 8-bit S08 central processing unit (CPU), which offers a good balance of performance and power efficiency for embedded applications.
- Low Power Operation: The MC9S08DZ60 series is designed for low-power operation, making it suitable for battery-powered or energy-efficient applications.
- On-Chip Memory: The MC9S08DZ60 series features on-chip Flash memory for program storage and on-chip RAM for data storage, enabling efficient code execution and data manipulation.
- Peripherals: The series includes a variety of on-chip peripherals, such as timers, analog-to-digital converters (ADCs), serial communication interfaces (UART, SPI, I2C), and general-purpose input/output (GPIO) ports, providing flexibility for interfacing with external devices.
- Interrupt Controller: The MC9S08DZ60 series has an interrupt controller that supports various interrupt sources, allowing efficient handling of real-time events.
- Clock and Reset Circuitry: The series includes an internal clock generator and reset circuitry to provide precise timing and reliable system startup.
- Watchdog Timer: The MC9S08DZ60 series includes a watchdog timer that provides a safety mechanism to reset the MCU in case of system faults.
- Multiple Package Options: The MC9S08DZ60 series is available in various package options, providing flexibility in board design and integration.
- Development Support: The MC9S08DZ60 series is supported by a range of development tools, including integrated development environments (IDEs), compilers, and debuggers, making it easier for developers to design and test applications.
- Robust Ecosystem: Being part of the S08 family, the MC9S08DZ60 series benefits from a rich ecosystem of software libraries, application notes, and community support.
These features make the MC9S08DZ60 series suitable for a wide range of applications, including industrial control, automotive, consumer electronics, medical devices, and more. With its balance of performance, low power, and on-chip peripherals, the MC9S08DZ60 series provides a cost-effective solution for various embedded control needs.
The three basic properties of the connector:
The three basic properties of a connector are:
- Mechanical Properties: The mechanical properties of a connector refer to its physical characteristics and how it physically connects and disconnects with another device or component. Key aspects of the mechanical properties include:
- Mating and Unmating: The ease and reliability of connecting and disconnecting the connector’s mating halves without causing damage or wear.
- Durability: The connector’s ability to withstand repeated mating and unmating cycles without compromising its performance.
- Mechanical Strength: The connector’s ability to withstand mechanical forces, such as vibration, shock, and pulling forces, without failing.
- Insertion and Extraction Force: The force required to insert and remove a connector from its mating counterpart.
- Size and Form Factor: The physical dimensions and shape of the connector, which determine its compatibility with specific applications and devices.
- Electrical Properties: The electrical properties of a connector refer to its ability to transmit electrical signals with minimal loss or interference. Key aspects of the electrical properties include:
- Contact Resistance: The resistance of the electrical contacts in the connector, which should be as low as possible to minimize voltage drop and signal loss.
- Insulation Resistance: The ability of the connector to maintain electrical isolation between adjacent contacts and prevent leakage currents.
- Dielectric Withstanding Voltage: The maximum voltage that the connector can withstand without breaking down and causing electrical arcing.
- Signal Integrity: The ability of the connector to preserve the integrity of transmitted signals, avoiding signal degradation or distortion.
- Current and Voltage Rating: The maximum current and voltage levels that the connector can safely handle.
- Environmental Properties: The environmental properties of a connector relate to its ability to withstand various environmental conditions without performance degradation or damage. Key aspects of the environmental properties include:
- Temperature Range: The operating temperature range in which the connector can function reliably without issues.
- Environmental Sealing: The level of protection against moisture, dust, and other contaminants, often specified using IP (Ingress Protection) ratings.
- Chemical Resistance: The ability to resist damage from exposure to certain chemicals or solvents.
- Shock and Vibration Resistance: The ability to withstand mechanical shocks and vibrations without failure.
- Corrosion Resistance: The ability to resist corrosion from environmental factors, such as humidity or salty atmospheres.
- UV Resistance: The ability to withstand exposure to ultraviolet (UV) radiation from the sun without degradation.
These three fundamental properties are essential considerations in the selection and application of connectors, as they impact the connector’s performance, reliability, and suitability for specific use cases and environments.
What is the principle of zero temperature compensation?
The principle of zero temperature compensation is a technique used to minimize the effects of temperature variations on certain electronic devices or systems, particularly those involving precision measurements or critical control applications. The goal of zero temperature compensation is to maintain stable and accurate performance across a wide range of temperatures.
In many electronic devices, components, or sensors, the electrical characteristics, such as resistance, capacitance, or voltage, can change with fluctuations in temperature. These temperature-induced variations can lead to errors or inaccuracies in the operation of the device or system. Zero temperature compensation aims to eliminate or minimize these temperature-related effects to maintain precise and consistent performance.
The principle behind zero temperature compensation involves the use of additional circuitry or algorithms to offset the temperature-induced variations. Here’s how it typically works:
- Temperature Sensing: The first step is to measure the temperature of the device or its critical components. This can be achieved using a dedicated temperature sensor or by using temperature-sensitive elements within the device itself.
- Error Characterization: Next, the system quantifies the impact of temperature on the device’s performance. Through calibration or characterization, the system determines how the device’s output or behavior changes with temperature variations.
- Compensation Circuitry or Algorithms: Based on the temperature measurements and error characterization, compensation circuitry or algorithms are implemented to counteract the temperature effects. The compensation circuitry may include resistors, capacitors, or active components, depending on the specific device and its temperature-dependent characteristics.
- Feedback Control: In some cases, a feedback control loop is used to continuously adjust the compensation circuitry based on real-time temperature measurements. This ensures that the device remains accurately compensated as the temperature changes.
- Testing and Validation: The compensated device or system is rigorously tested and validated over a range of temperatures to verify its performance and accuracy. Fine-tuning may be required during this process to achieve optimal compensation.
Zero temperature compensation is commonly used in various applications, including precision sensors (e.g., pressure sensors, temperature sensors), voltage references, frequency oscillators, and other critical components or systems where temperature stability is essential. By minimizing the impact of temperature variations, zero temperature compensation helps maintain consistent performance and accuracy, making the device or system more reliable and suitable for challenging operating environments.
What are the main features of MB3884?
1 The rise time and fall time of the output voltage of the three DC C converters are not freely controlled by the magnitude of the load, and therefore, it is not necessary to control the turn-on and turn-off sequence between the respective power sources by the timing control circuit.
2 No current detecting Resistors is used in the synchronous rectification mode.The power supply voltage of the B3884 itself, the input supply voltage of the switching regulator, and the input supply voltage of the LD0 can be connected simultaneously or separately, regardless of the order between the three input voltages.
3 The drive capability of the switching regulator main FET for the movement and the FET drive circuit for synchronous rectification.
What is a host controller?
A host controller, in the context of computer systems and electronics, refers to a hardware or software component responsible for managing and controlling communication between a host system (such as a computer or embedded device) and one or more peripheral devices.
Host controllers play a crucial role in enabling the interaction between the host system and various peripherals, such as USB devices, disk drives, printers, and other external hardware. They provide the necessary interfaces, protocols, and drivers to facilitate data transfer and communication.
Here are a few examples of host controllers in different contexts:
- USB Host Controller: In the case of Universal Serial Bus (USB) technology, a USB host controller is responsible for managing USB devices connected to a computer or other host system. It initiates data transfers, handles device enumeration, manages power delivery to USB devices, and provides the necessary drivers to interact with various USB peripherals.
- SATA Host Controller: For Serial ATA (SATA) storage devices, a SATA host controller is responsible for managing the communication between the host system and SATA hard drives or SSDs. It provides the necessary interfaces and drivers to read and write data to the storage devices.
- PCI Host Controller: In a computer’s architecture, a PCI (Peripheral Component Interconnect) host controller manages the communication between the host system and PCI devices, such as graphics cards, network cards, and sound cards. It handles the configuration, data transfer, and control of these PCI devices.
- Ethernet Host Controller: An Ethernet host controller facilitates the connection between a host system and Ethernet networks. It manages the transmission and reception of data packets over the Ethernet interface.
- Bluetooth Host Controller: For Bluetooth-enabled devices, a Bluetooth host controller manages the Bluetooth communication between the host system and Bluetooth peripherals, such as keyboards, mice, and headphones.
In each case, the host controller acts as an intermediary between the host system and the peripheral devices, abstracting the complexities of device communication and providing a standardized interface for seamless interaction. The host controller is an essential component in modern computer systems and embedded devices that rely on multiple peripherals to extend functionality and usability.
COMMENTS