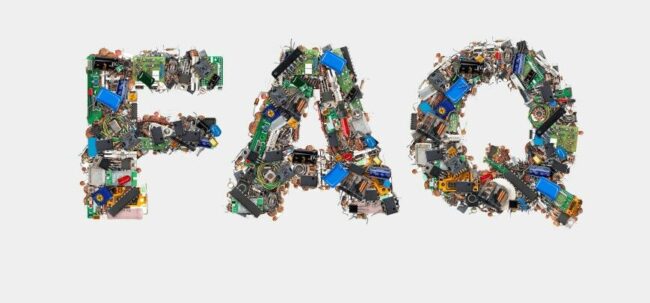
What are the types of flow control statements?
Flow control statements are essential components of programming languages that allow you to control the execution order of instructions in a program. They determine which sections of code are executed under different conditions. The main types of flow control statements are:
- Conditional Statements:
- if statement: Executes a block of code if a given condition is true.
- else statement: Executes a block of code if the preceding if condition(s) is false.
- else if statement: Allows you to check multiple conditions in sequence.
- switch statement: Used for selecting one of many code blocks to be executed.
- Looping Statements (Iteration):
- for loop: Executes a block of code a specific number of times.
- while loop: Repeatedly executes a block of code while a condition is true.
- do-while loop: Similar to the while loop, but ensures that the code block is executed at least once.
- Jump Statements:
- break statement: Terminates the execution of a loop or switch statement.
- continue statement: Skips the rest of the current iteration and moves to the next one in a loop.
- return statement: Terminates the current function and returns a value to the caller.
- Exception Handling Statements:
- try-catch statement: Used to handle exceptions or errors that may occur during program execution.
- throw statement: Generates a user-defined exception or error.
These flow control statements provide the foundation for creating structured and organized programs by controlling the flow of execution based on different conditions and requirements. The specific syntax and usage may vary depending on the programming language you’re working with.
What are the characteristics of photodiodes?
Photodiodes are semiconductor devices that are designed to detect light and convert it into an electrical current. They have several important characteristics that make them suitable for various applications in electronics, communications, sensing, and more. Here are some of the key characteristics of photodiodes:
- Photosensitivity: Photodiodes are highly sensitive to light, even in the presence of low light levels. This sensitivity allows them to detect even small amounts of light energy.
- Reverse Bias Operation: Photodiodes are typically operated under reverse bias, meaning a voltage is applied in the reverse direction across the diode. This creates a depletion region that widens when exposed to light, leading to an increase in the current flow.
- Fast Response Time: Photodiodes have fast response times, enabling them to quickly detect changes in light levels. This characteristic makes them suitable for applications that require rapid detection, such as optical communication systems.
- Low Dark Current: Dark current refers to the current that flows through a photodiode even in the absence of light. High-quality photodiodes have low dark currents, which helps maintain their accuracy and sensitivity.
- Wide Spectral Range: Photodiodes can be designed to detect light across a wide range of wavelengths, from ultraviolet (UV) to infrared (IR), depending on the materials used in their construction.
- Linear Response: In the ideal case, the current generated by a photodiode is directly proportional to the intensity of the incident light. This linearity makes them suitable for applications that require accurate light detection and measurement.
- Low Noise: Photodiodes have low levels of noise in their output signals, which is important for obtaining accurate measurements, especially in low-light conditions.
- Small Size: Photodiodes are typically compact and small in size, allowing them to be integrated into various electronic systems without taking up much space.
- Low Power Consumption: Photodiodes generally consume low amounts of power, making them energy-efficient for battery-powered devices and other applications where power consumption is a concern.
- Temperature Dependence: The performance of photodiodes can be affected by temperature changes. Some photodiodes are designed to have minimal temperature dependence, while others may require temperature compensation circuits.
- Avalanche Photodiodes (APDs): These specialized photodiodes can provide internal signal amplification through avalanche multiplication, leading to higher sensitivity. However, they are more complex to operate and may exhibit higher noise levels.
- Photon-to-Current Conversion: Photodiodes convert incoming photons of light directly into an electrical current, which can then be easily measured and processed by electronic circuits.
Overall, photodiodes offer a range of characteristics that make them versatile devices for light detection and measurement applications in various fields. The choice of a specific photodiode type depends on the requirements of the application, including the desired spectral sensitivity, speed, accuracy, and operating conditions.
Which conditions should UCC28950 meet first before starting?
The UCC28950 is a controller IC designed for high-performance, active power factor correction (PFC) converters. Before starting its operation, there are several conditions that the UCC28950 typically needs to meet to ensure proper and safe functionality. These conditions help ensure that the power factor correction circuit operates correctly and efficiently. The specific conditions may vary depending on the application and design, but here are some general conditions that the UCC28950 might need to meet before starting:
- Power Supply Voltage: The UCC28950 requires a stable and appropriate power supply voltage to operate. This voltage should be within the specified operating range of the IC. It’s crucial to ensure that the voltage supplied to the UCC28950 is within its recommended limits to prevent damage and ensure reliable operation.
- Startup Circuitry: Many PFC controllers, including the UCC28950, might require an external startup circuit or a specific startup sequence to initiate their operation. This might involve providing an initial voltage to specific pins or components to trigger the startup process.
- Undervoltage Lockout (UVLO): The UCC28950 might have an undervoltage lockout (UVLO) feature, which ensures that the controller doesn’t start operating until the input voltage reaches a certain threshold. This helps prevent erratic operation during low input voltage conditions.
- Stable Feedback Loop: Proper feedback from the output of the PFC circuit to the UCC28950 is crucial for accurate regulation. Before starting, the feedback loop should be stable and properly connected to ensure that the output voltage is controlled effectively.
- External Components: The UCC28950 might require certain external components, such as resistors, capacitors, and inductors, to be properly connected and within their specified values. These components play a role in the operation and regulation of the PFC circuit.
- Protection Circuits: Depending on the design and application, the UCC28950 might incorporate various protection circuits, such as overvoltage protection, overcurrent protection, and thermal protection. These circuits ensure that the controller and the power stage are protected from abnormal operating conditions.
- External Circuitry: If the UCC28950 is part of a larger power conversion circuit, other components, such as switching transistors, diodes, and transformers, should be correctly connected and functioning as intended.
- Stable Environment: The UCC28950 might operate more reliably in a stable environment. Rapid changes in input voltage or load conditions could potentially impact its performance, so the circuit’s stability should be ensured.
It’s important to refer to the UCC28950’s datasheet and application notes provided by the manufacturer for specific guidelines on how to meet these conditions and ensure successful startup. Designing and implementing power factor correction circuits requires careful consideration of these conditions to achieve efficient and safe operation.
What is the difference between an inductor and a magnetic bead?
Inductors and magnetic beads are both passive electronic components that utilize magnetic properties, but they serve different purposes and have distinct characteristics. Here’s a comparison of the two:
Inductor:
- Function: An inductor is a passive component that stores energy in the form of a magnetic field when current flows through it. It resists changes in current, creating a self-induced voltage that opposes any change in the current. Inductors are commonly used in circuits for energy storage, filtering, and creating reactive components in analog and digital applications.
- Construction: Inductors are typically constructed by winding a wire (or coil) around a core, which can be made of various materials like iron, ferrite, or air. The number of turns in the coil and the core material influence the inductance value.
- Symbol: In circuit diagrams, inductors are represented by a symbol that resembles a coil or solenoid.
- Applications: Inductors are used in a variety of applications such as filtering out high-frequency noise, energy storage in switching power supplies, creating resonant circuits, and impedance matching.
- Impedance: Inductors have a frequency-dependent impedance. Their impedance increases with frequency, making them useful for filtering high-frequency noise.
Magnetic Bead:
- Function: A magnetic bead, also known as a ferrite bead or choke, is primarily used for noise suppression and EMI (electromagnetic interference) filtering. It is designed to suppress high-frequency noise by converting the noise energy into heat through hysteresis losses in the ferrite material.
- Construction: Magnetic beads consist of a ferrite core wrapped with wire, similar to an inductor. However, the primary purpose of the bead is to absorb and dissipate high-frequency noise rather than store energy.
- Symbol: The symbol for a magnetic bead is often represented by a circle with a vertical line passing through it, resembling the core of the bead.
- Applications: Magnetic beads are used in circuits where electromagnetic interference needs to be reduced or filtered out. They can be found in power supply lines, signal lines, and other paths susceptible to noise.
- Impedance: Magnetic beads have a high impedance at high frequencies, allowing them to effectively attenuate and suppress high-frequency noise.
In summary, while both inductors and magnetic beads utilize magnetic properties, their primary functions and applications differ. Inductors store energy and create reactive components in circuits, while magnetic beads are designed to suppress electromagnetic interference and filter out high-frequency noise. The choice between the two depends on the specific requirements of the circuit and the desired filtering or energy storage characteristics.
What constitutes the ignition control circuit?
The ignition control circuit is a crucial part of an internal combustion engine’s ignition system. It’s responsible for generating and delivering the high-voltage electrical spark that ignites the fuel-air mixture in the engine’s cylinders, resulting in the combustion process that powers the engine. The main components that constitute the ignition control circuit include:
- Ignition Switch: The ignition switch is typically located on the steering column or dashboard. It’s used to turn the ignition system on and off. When turned to the “ON” position, it activates various components in the ignition control circuit.
- Ignition Coil: The ignition coil is a transformer that converts the low-voltage electrical power from the battery into a high-voltage electrical pulse. This high-voltage pulse is needed to create a spark across the spark plugs.
- Distributor (if equipped): In older ignition systems, a distributor was used to distribute high-voltage current to the correct spark plug at the appropriate cylinder. Modern engines often use distributorless ignition systems (DIS) or coil-on-plug (COP) systems, where each spark plug has its own dedicated ignition coil.
- Spark Plug Wires (if equipped): In systems with a distributor, spark plug wires connect the distributor to the spark plugs, delivering the high-voltage pulse to the spark plugs at the right time. In DIS or COP systems, individual coils are directly connected to each spark plug.
- Spark Plugs: Spark plugs are essential components that generate the actual spark that ignites the air-fuel mixture in the engine’s cylinders.
- Engine Control Module (ECM) or Ignition Control Module (ICM): Modern engines often rely on an ECM or ICM to control the ignition timing and other parameters. These modules use sensors to determine the optimal time to trigger the spark plug and adjust ignition timing based on factors like engine speed, load, and temperature.
- Crankshaft Position Sensor: This sensor detects the position and speed of the engine’s crankshaft. The information from this sensor is used by the ECM or ICM to determine the correct timing for ignition.
- Camshaft Position Sensor (if equipped): Some engines also use a camshaft position sensor to provide information about the position of the engine’s camshaft. This information helps the ECM or ICM adjust ignition timing and other engine parameters.
- Knock Sensor (if equipped): Some advanced systems include a knock sensor that detects engine knocking or pinging. The ECM can adjust ignition timing to prevent knocking, which can be damaging to the engine.
- Control Logic and Wiring: The ignition control circuit relies on wiring and control logic to ensure that the spark plugs fire in the correct order and at the right time in the engine’s four-stroke cycle (intake, compression, power, exhaust).
- Power Source: The ignition control circuit requires a power source, often provided by the vehicle’s battery. The ignition switch controls the flow of power to the ignition components.
These components work together to generate the high-voltage spark necessary for combustion in internal combustion engines. The timing and coordination of these components are critical for the engine to run smoothly and efficiently.
How does the interrupt control register change?
Interrupt control registers are a part of microcontrollers and CPUs and are used to manage interrupts, which are signals generated by hardware or software events that interrupt the normal execution flow of a program. The exact behavior of an interrupt control register can vary depending on the specific microcontroller or CPU architecture you are referring to. However, I can provide a general overview of how interrupt control registers might change and how they are used:
- Configuration: Before interrupts can be used, the microcontroller or CPU needs to be configured. This typically involves setting up the interrupt control register(s) to specify which events or conditions should trigger interrupts, as well as configuring the priority of different interrupts if the system supports interrupt prioritization.
- Setting the Interrupt Enable Bit: Most interrupt control registers have individual bits that correspond to different interrupt sources. To enable a specific interrupt source, you would set the corresponding bit in the interrupt control register. This indicates that the microcontroller should respond to that specific interrupt source.
- Generating an Interrupt: When the condition associated with an enabled interrupt source occurs, the hardware raises an interrupt signal. This could be due to an external event (e.g., a button press) or an internal event (e.g., completion of a timer countdown). The microcontroller’s hardware checks the status of the interrupt control register to see which interrupts are enabled and which conditions have been met.
- Interrupt Service Routine (ISR): Once an interrupt is triggered, the microcontroller stops executing its current instructions and transfers control to a predefined piece of code known as the Interrupt Service Routine (ISR). The ISR handles the specific task related to the interrupt. This could involve saving the current state of the processor, performing some operations, and then restoring the state before the interrupt occurred.
- Clearing the Interrupt Flag: After the ISR has executed, the interrupt control register might need to be cleared or reset. This is usually done to acknowledge that the interrupt has been handled and to prepare for the next occurrence of the same interrupt source.
- Disabling Interrupts: In some cases, you might want to temporarily disable certain interrupts. This can be done by clearing the corresponding interrupt enable bit in the interrupt control register. This is often done to prevent certain interrupts from interrupting critical sections of code.
- Interrupt Prioritization: Many microcontrollers and CPUs support interrupt prioritization. In this case, the interrupt control register might include bits or fields that determine the priority of different interrupts. Higher priority interrupts will be serviced before lower priority ones.
- Masking Interrupts: In addition to enabling and disabling interrupts, some systems allow you to mask (ignore) specific interrupt sources temporarily, even if they are enabled. This can be useful when certain conditions should be ignored for a specific period.
Keep in mind that the specific behavior and configuration of interrupt control registers can vary significantly between different microcontroller architectures and CPU designs. Always refer to the documentation provided by the manufacturer or the microcontroller’s datasheet to understand how interrupt control registers work for a particular system.
How to create more value for the vast majority of end users in non-portable and battery-powered applications?
Creating more value for the vast majority of end users in non-portable and battery-powered applications involves understanding their needs, improving efficiency, and enhancing the user experience. Here are some strategies to achieve this:
- Energy Efficiency and Longevity:
- Focus on optimizing energy consumption to extend battery life. Implement power-saving modes and techniques.
- Use energy-efficient components, such as low-power microcontrollers, sensors, and display technologies.
- Provide energy usage insights to users, so they can make informed decisions about power consumption.
- Performance and Responsiveness:
- Optimize software and hardware for fast boot times and responsiveness.
- Ensure consistent performance across various usage scenarios to enhance user satisfaction.
- Reliability and Durability:
- Design robust and reliable systems that can withstand environmental conditions, temperature variations, and mechanical stress.
- Implement proper error handling and recovery mechanisms to minimize downtime.
- User-Friendly Interfaces:
- Design intuitive user interfaces that are easy to navigate and require minimal user training.
- Use clear, informative, and context-sensitive displays and indicators.
- Remote Monitoring and Control:
- Provide remote monitoring and control options using wireless connectivity. This allows users to access and manage the application from a distance.
- Predictive Maintenance:
- Implement predictive maintenance features that monitor system health and provide users with alerts or recommendations before issues arise.
- Data Analytics and Insights:
- Collect and analyze usage data to gain insights into user behavior and application performance.
- Use this data to make informed decisions about product improvements and updates.
- Customization and Flexibility:
- Provide options for user customization and configuration to cater to various preferences and needs.
- Allow users to adjust settings, thresholds, and parameters to match their specific requirements.
- Reduced Total Cost of Ownership:
- Focus on solutions that not only provide value upfront but also minimize ongoing maintenance and support costs.
- Offer cost-effective solutions that balance initial investment with long-term savings.
- Support and Documentation:
- Provide comprehensive user manuals, guides, and online resources to help users understand and use the application effectively.
- Offer responsive customer support to address user inquiries and concerns promptly.
- Sustainability and Environmental Impact:
- Consider the environmental impact of the product’s lifecycle, from manufacturing to disposal.
- Design products with recyclable materials and minimize energy consumption during operation.
- Future-Proofing:
- Anticipate technological advancements and design products that can adapt to new features and capabilities through software updates.
- Collaboration and User Feedback:
- Collaborate with users to understand their needs and challenges.
- Incorporate user feedback into product updates and enhancements.
By focusing on these strategies, you can create non-portable, battery-powered applications that offer substantial value to a broad range of users and contribute to their overall satisfaction and success.
Leaky cable systems have four major drawbacks. What is it?
Leaky cable systems, also known as radiating cable systems, are used for various communication and signal distribution applications, such as providing wireless coverage in tunnels, mines, and other underground environments. However, leaky cable systems have some drawbacks and limitations, including the following four major issues:
- Signal Loss and Attenuation: Leaky cable systems are designed to radiate electromagnetic energy along their length to provide wireless coverage. This radiation leads to signal loss and attenuation along the cable’s length. As the signal propagates, it weakens, which can limit the coverage distance and effectiveness of the system.
- Uneven Coverage: Achieving uniform and consistent coverage with leaky cable systems can be challenging. Due to signal loss and the radiation pattern of the cable, there can be areas with strong signal coverage and areas with weaker or no coverage. This non-uniform distribution can result in communication dead spots or areas with reduced signal quality.
- Interference: Leaky cable systems radiate electromagnetic energy into the surrounding environment to provide coverage. However, this radiation can interfere with other wireless systems operating in the same frequency bands. Interference can degrade the performance of both the leaky cable system itself and other nearby wireless systems.
- Installation and Maintenance Complexity: Installing and maintaining leaky cable systems can be complex and labor-intensive. The cable needs to be properly installed along the desired coverage area, which can involve challenges in tunnels, mines, and other confined spaces. Additionally, maintenance and troubleshooting can be difficult, especially if the cable is located in hard-to-reach locations.
Despite these drawbacks, leaky cable systems can still be valuable solutions in certain situations where traditional wireless coverage methods are not practical or effective. It’s essential to carefully assess the specific needs, constraints, and challenges of the environment in which the leaky cable system will be deployed. Additionally, advancements in technology and installation techniques may help mitigate some of these drawbacks over time.
IC card applications are quite extensive, what is the application field?
IC (Integrated Circuit) card applications are indeed extensive and span across various industries and sectors. These cards, commonly known as “smart cards,” contain a microprocessor or memory chip that enables them to store and process data. Here are some of the diverse application fields of IC cards:
- Payment and Financial Services:
- Credit and debit cards: IC cards offer secure and convenient transactions, often with added authentication methods like PIN or biometrics.
- Contactless payment cards: These allow users to make payments by simply tapping the card on a reader.
- Identification and Authentication:
- Government ID cards: Used for driver’s licenses, national IDs, and passports to enhance security and combat fraud.
- Employee access cards: Used for secure entry to buildings and facilities.
- Health insurance cards: Store medical information and enable efficient healthcare services.
- Transportation and Ticketing:
- Transit cards: Used for paying fares on public transportation systems.
- Toll collection cards: Used for automatic toll payment on highways.
- Mobile Communication:
- SIM cards: Essential for mobile phones, storing subscriber identity and network information.
- Secure Access and Data Protection:
- Secure entry cards: Used for controlled access to restricted areas or computer systems.
- Authentication tokens: Used in two-factor authentication systems for added security.
- Loyalty and Membership Programs:
- Loyalty cards: Offer discounts and rewards for repeat customers.
- Membership cards: Grant access to special privileges and services.
- Healthcare and Medical Applications:
- Health insurance cards: Store patient information and facilitate medical services.
- Prescription cards: Store prescription details and medication history.
- Retail and Inventory Management:
- Inventory control cards: Help track and manage inventory levels efficiently.
- Customer loyalty and gift cards: Used for incentivizing purchases and gifting.
- Education:
- Student ID cards: Used for access control and identification on campuses.
- Library cards: Enable borrowing and access to library resources.
- Entertainment:
- Event tickets: Store event details and facilitate entry to concerts, sports events, and more.
- Gaming cards: Used in arcade games and gaming consoles.
- Government and Civic Services:
- Social welfare cards: Provide access to government assistance programs.
- Voter ID cards: Used for voter registration and identification in elections.
- Hotel and Hospitality:
- Room key cards: Used for access to hotel rooms and amenities.
- Guest cards: Store guest information and preferences for personalized service.
IC card applications continue to evolve as technology advances, with increasing emphasis on security, convenience, and interoperability. The versatility of IC cards makes them a cornerstone of modern identity and transaction systems across a wide range of sectors.
According to the direction of the increase or decrease of the stack pointer and whether the storage unit pointed to by the pointer is empty, what kind of stacking methods are there?
Stacking methods in computer science refer to the ways in which data is organized and accessed in a stack data structure. The stack data structure follows the Last-In-First-Out (LIFO) principle, where the last element added is the first to be removed. Stacking methods can be categorized based on the direction of the increase or decrease of the stack pointer and whether the storage unit pointed to by the pointer is empty. Here are the common stacking methods:
- Ascending Stack:
- In an ascending stack, the stack pointer starts from a lower memory address and increases as elements are pushed onto the stack.
- Elements are added at higher memory addresses, and the stack pointer moves toward higher addresses with each push operation.
- This method is commonly used in hardware architectures where memory addresses increase as stack depth increases.
- Descending Stack:
- In a descending stack, the stack pointer starts from a higher memory address and decreases as elements are pushed onto the stack.
- Elements are added at lower memory addresses, and the stack pointer moves toward lower addresses with each push operation.
- This method is commonly used in many programming languages and software implementations of stacks.
- Full Descending Stack:
- In a full descending stack, the stack pointer initially points to an empty location below the stack’s allocated memory.
- As elements are pushed, the stack pointer increments and points to the top element in the stack.
- This method helps identify an empty stack when the stack pointer points to the lowest memory location.
- Empty Descending Stack:
- In an empty descending stack, the stack pointer initially points to the first location in the stack’s allocated memory.
- As elements are pushed, the stack pointer increments and points to the next available location.
- This method helps identify an empty stack when the stack pointer points to the first memory location.
The choice of stacking method depends on the hardware architecture, programming language conventions, and the specific use case. Descending stacks are more common in software implementations, while ascending stacks are seen in specific hardware architectures. The full and empty descending stack methods are used to determine whether the stack is empty based on the initial position of the stack pointer.
COMMENTS