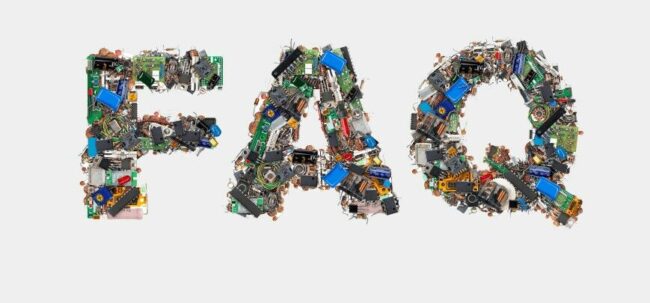
What are the three important parts of SNMP?
SNMP (Simple Network Management Protocol) is a protocol used for managing and monitoring network devices and systems. It consists of three important parts:
- Managed Devices: These are the network devices or systems that are being monitored and managed using SNMP. Managed devices can include routers, switches, servers, printers, and more. These devices have SNMP agents running on them, which collect and store information about the device’s performance, status, and other relevant data.
- SNMP Agents: An SNMP agent is software that runs on managed devices and collects information about the device’s various parameters and characteristics. It responds to requests for information from SNMP management systems (also known as Network Management Systems or NMS). The agent stores this information in a Management Information Base (MIB), which is a hierarchical database containing organized information about the device’s configuration and performance.
- Network Management Systems (NMS): NMS are software applications or systems used by network administrators to monitor and manage the devices on a network. These systems communicate with SNMP agents on managed devices to gather data and send commands. NMS provide a user interface through which administrators can view the collected data, configure devices, set alerts, and perform various management tasks. NMS use SNMP queries and traps to retrieve information from SNMP agents and to receive notifications about events occurring on the network.
In summary, the three important parts of SNMP are the managed devices, SNMP agents that run on these devices, and the Network Management Systems (NMS) used to monitor and manage the devices through SNMP communication.
What are the clock sources for the AVR?
AVR microcontrollers (such as those from Atmel, which is now a part of Microchip Technology) typically have various clock sources that can be used to drive the CPU and other parts of the microcontroller. The available clock sources can vary depending on the specific AVR model, but here are some common clock sources you might find in AVR microcontrollers:
- Internal RC Oscillator (RC oscillator): This is an internal oscillator that generates a clock signal using a resistor-capacitor (RC) network. It’s relatively simple and provides a moderate level of accuracy but may not be as precise as other clock sources. It’s often used in low-power applications or when precise timing is not critical.
- Internal Crystal Oscillator: Some AVRs have an internal oscillator circuit that can be connected to an external crystal. This provides a more accurate and stable clock signal compared to the RC oscillator. It’s commonly used when moderate accuracy is required.
- External Crystal Oscillator: AVRs can be connected to an external crystal oscillator for even higher accuracy and stability. This is often used in applications where precise timing is essential, such as communication interfaces.
- Internal PLL (Phase-Locked Loop): Some AVRs have a built-in PLL that can multiply the frequency of an existing clock source. This can be useful when higher clock speeds are needed without relying solely on external crystal oscillators.
- Calibrated Internal RC Oscillator: Some newer AVRs come with calibrated internal RC oscillators. These oscillators are factory-calibrated for improved accuracy, making them suitable for applications where moderate accuracy is required without the need for an external crystal.
- External Clock Source: AVRs can also be driven by an external clock signal provided by an external source, such as another microcontroller or an external oscillator module.
- Watchdog Oscillator: The Watchdog Timer in AVRs can also be used as a clock source. While not typically used as the main clock source for the CPU, it can be utilized for specific purposes.
- Low-Frequency Crystal Oscillator: Some AVRs support low-frequency crystal oscillators, which are used for applications requiring low power consumption and lower clock speeds.
The availability of these clock sources and their specific features can vary from one AVR model to another. It’s essential to refer to the datasheet or technical documentation of the specific AVR microcontroller you are using to understand the clock source options available and their characteristics.
What is the detection method for the gaze sensor?
Gaze sensors, also known as eye-tracking sensors, are devices that can detect and track a person’s eye movements and gaze direction. These sensors are used in various applications, including human-computer interaction, virtual reality, medical research, and more. There are different methods for detecting gaze using gaze sensors, and here are some common techniques:
- Pupil-Corneal Reflection (P-C-R) Method: This method involves emitting infrared light toward the eye and capturing the reflections from both the cornea (the outermost layer of the eye) and the pupil. By analyzing the positions of these reflections, the sensor can determine the direction of gaze. The distance between the corneal and pupil reflections provides information about the gaze vector.
- Bright Pupil and Dark Pupil Methods: In these methods, infrared light is used to illuminate the eye. In the bright pupil method, the infrared light reflects off the retina, creating a bright spot in the pupil’s center when the eye is aligned with the sensor. In the dark pupil method, the light source is placed near the camera, causing the pupil to appear dark when the eye is aligned with the sensor. By tracking the movement of the bright or dark pupil, the sensor can estimate the gaze direction.
- Video-Based Tracking: This method involves using cameras to capture video of the user’s eyes. Computer vision algorithms analyze the images to detect features such as the position of the pupil, iris, and eye corners. By tracking the movement of these features over time, the sensor can determine the gaze direction.
- Electrooculography (EOG): EOG measures the electrical potential difference between the front and back of the eyeball, which changes as the eye rotates. EOG sensors are often placed around the eye to detect these changes and infer gaze direction based on the electrical signals produced.
- Infrared Gaze Point Estimation: In this approach, multiple infrared light sources are positioned around the screen, and an infrared camera captures the reflections from the user’s eyes. By triangulating the positions of these reflections, the sensor can estimate the gaze point on the screen.
- Corneal Reflection Tracking: This method involves detecting the position of the corneal reflection by analyzing the highlights that appear on the cornea due to external light sources or displays. By tracking the movement of the corneal reflection, the gaze direction can be determined.
The choice of detection method depends on factors such as accuracy requirements, application context, and the specific technology used in the gaze sensor. Many modern gaze sensors use a combination of these techniques to achieve accurate and reliable gaze tracking. The field of gaze tracking technology is evolving rapidly, leading to continuous improvements in accuracy, robustness, and usability.
How do I configure the PLL when I actually use it?
Configuring the PLL (Phase-Locked Loop) in a microcontroller involves setting up its parameters to generate a desired clock frequency from an available reference clock source. The specific steps and registers involved can vary based on the microcontroller’s architecture and manufacturer. Below, I’ll provide a general guide on how to configure a PLL in a microcontroller. Please note that this is a high-level overview, and you should always refer to your microcontroller’s datasheet or reference manual for precise information.
Here’s a general process for configuring a PLL:
- Understand PLL Parameters: First, you need to know the PLL parameters that you can configure:
- Reference Clock (f_ref): The input clock frequency that the PLL uses as a reference.
- Desired Output Clock (f_out): The frequency you want the PLL to generate.
- Multiplier (N): The factor by which the reference clock is multiplied to achieve the output frequency.
- Divider (M): The optional division factor applied to the output frequency.
- Prescaler (P): Some microcontrollers have a prescaler before the PLL, which divides the reference clock before it enters the PLL.
- Set PLL Registers: Access the registers associated with the PLL configuration. These registers can control various PLL settings, including the multiplier, divider, and prescaler (if applicable). Consult your microcontroller’s datasheet or reference manual to identify the specific registers for PLL configuration.
- Configure Multiplier and Divider: Set the values for the multiplier (N) and divider (M) to achieve the desired output frequency:
- Calculate the required multiplier: N = f_out / f_ref
- Calculate the effective output frequency after the divider: f_pll_out = f_ref * N / M
- Set Prescaler (if applicable): If your microcontroller has a prescaler before the PLL, set its value to achieve the desired reference frequency (f_ref).
- Configure PLL Control Bits: PLL configuration registers might also have control bits for enabling/disabling the PLL, selecting the reference source, and other settings. Configure these bits as needed.
- Apply Configuration and Wait for Lock: Write the configured values to the PLL registers. After configuring the PLL, the PLL needs some time to stabilize and “lock” onto the desired frequency. Refer to your microcontroller’s documentation for information on how to monitor the PLL lock status. You might need to wait until the PLL is locked before proceeding.
- Update System Clock Source: If your microcontroller allows the system clock source to be selected, update it to use the PLL-generated clock.
- Check and Validate: Verify that the system is running at the expected frequency. You might use timers or other methods to confirm the clock frequency.
Remember that this is a general guide, and the specific steps and registers can vary based on your microcontroller model. It’s crucial to refer to the datasheet and reference manual provided by the microcontroller manufacturer for accurate and detailed instructions on configuring the PLL. Making incorrect changes to clock settings can impact the microcontroller’s performance and stability.
What are the representative products of DSP processors?
Digital Signal Processors (DSPs) are specialized microprocessors designed for efficiently performing digital signal processing tasks, such as audio and video processing, communications, control systems, and more. There are several manufacturers that produce DSP processors, each offering a range of products with varying capabilities. As of my last knowledge update in September 2021, here are some representative DSP processor products from well-known manufacturers:
- Texas Instruments (TI):
- TMS320C6000 series: These are high-performance DSPs used in applications like telecommunications, audio processing, and industrial control.
- TMS320C5000 series: Designed for low-power applications, these DSPs find use in portable devices, audio processing, and control systems.
- Analog Devices:
- SHARC processors: These processors are designed for high-performance real-time processing in audio, communications, and industrial applications.
- Blackfin processors: Combining DSP and microcontroller features, these processors are used in applications like audio processing, motor control, and multimedia systems.
- NXP Semiconductors:
- i.MX RT series: While these are technically microcontrollers, they integrate powerful DSP capabilities and are used in applications like audio processing, motor control, and real-time control systems.
- STMicroelectronics:
- STM32F4xx series: Similar to NXP’s i.MX RT series, these are microcontrollers with DSP capabilities, suitable for audio, motor control, and digital signal processing.
- Qualcomm:
- Hexagon DSPs: Found in Qualcomm’s Snapdragon processors, these DSPs excel in multimedia processing, audio, and wireless communication tasks.
- Xilinx:
- Zynq UltraScale+ MPSoC: Combining FPGA and ARM Cortex-A9 cores with real-time processing units, this platform is used in high-performance signal processing, communications, and control applications.
- Intel (formerly Altera):
- Intel FPGA DSP blocks: Intel’s FPGAs offer customizable DSP blocks that can be used for a wide range of signal processing applications, including communications, multimedia, and more.
- Renesas:
- RX DSP cores: These cores, integrated into Renesas’ microcontrollers, offer DSP capabilities for motor control, audio processing, and other tasks.
Please note that the DSP processor landscape is continually evolving, and new products might have been introduced since my last update. When considering a DSP processor for your project, it’s important to review the latest offerings from manufacturers, compare their features, performance, and power consumption, and choose the one that best fits your application’s requirements.
What is the definition of the physical layer?
The physical layer is a fundamental concept in networking and telecommunications that refers to the first layer of the OSI (Open Systems Interconnection) model. The OSI model is a conceptual framework used to standardize the functions of a networking or communication system into seven distinct layers, each responsible for specific tasks. The physical layer is the lowest layer in this model and deals with the actual physical transmission and reception of raw data bits over a physical medium, such as cables or wireless signals.
In essence, the physical layer is responsible for:
- Transmission of Raw Data: It involves converting binary data (0s and 1s) from the data link layer or higher layers into electrical, optical, or electromagnetic signals suitable for transmission over a physical medium.
- Physical Medium: It encompasses the actual physical infrastructure used for communication, including cables, connectors, switches, routers, wireless transmitters, antennas, and other devices that facilitate the transmission of signals.
- Physical Signaling: The physical layer defines the characteristics of the signals themselves, such as their voltage levels, modulation methods, encoding schemes, and transmission rates (baud rate or bit rate).
- Transmission Modes: It specifies whether data is transmitted in simplex (one-way), half-duplex (both directions but not simultaneously), or full-duplex (both directions simultaneously) mode.
- Bit Synchronization: It ensures that the sender and receiver are synchronized in terms of the timing of signal transitions.
- Data Link Establishment and Termination: It deals with how devices establish and terminate connections, including processes such as handshaking and error detection.
- Physical Topology: It describes how devices are physically connected in a network, such as star, bus, ring, or mesh topologies.
- Noise and Interference Handling: The physical layer must consider noise and interference that can degrade the quality of the transmitted signals and take measures to minimize their impact.
Examples of physical layer components include Ethernet cables, fiber-optic cables, wireless antennas, voltage levels used to represent binary data, modulation techniques like amplitude modulation (AM) or frequency modulation (FM), and various electrical characteristics of transmission lines.
In summary, the physical layer is responsible for the tangible transmission of digital data across physical media, focusing on the specifics of signaling, encoding, and the physical infrastructure itself. It plays a crucial role in ensuring that the bits sent by the sender are accurately received by the receiver, laying the foundation for higher-layer protocols and data communication in networking systems.
What is weak feed line current differential protection?
Weak-feed line current differential protection is a type of protection scheme used in electrical power systems to safeguard power transmission or distribution lines from faults and abnormalities. It’s designed to detect and quickly isolate faults along the protected line, improving the reliability and stability of the power grid.
In a power system, a feed line carries electrical power from a source, such as a substation, to load centers or distribution points. A “weak-feed” line typically refers to a line with relatively low fault current levels compared to other lines in the network. This might be due to factors like the line’s length, impedance, or connection to lower-capacity sources.
Current differential protection operates based on the principle that the sum of currents entering a protected section of the power line should be equal to the sum of currents leaving it under normal operating conditions. However, in the event of a fault, the current entering and leaving the protected section becomes imbalanced due to the fault current flowing into the line from one direction and returning from the other direction.
Here’s how weak-feed line current differential protection works:
- Current Transformers (CTs): Current transformers are installed at both ends of the protected line section. These CTs measure the current entering and leaving the section.
- Current Comparison: The currents measured by the CTs are compared. In a fault-free scenario, the sum of the currents entering the section should equal the sum of the currents leaving the section.
- Differential Relay: A differential relay is used to compare the currents. If the relay detects a significant difference between the currents (indicating a fault), it initiates a trip signal.
- Tripping: The trip signal is sent to the circuit breakers at both ends of the protected line section. These circuit breakers are then commanded to open, isolating the faulty section from the rest of the power system. This action helps prevent damage to equipment and ensures the safety and stability of the network.
Weak-feed line current differential protection offers advantages in scenarios where traditional overcurrent protection might not be as effective due to the low fault current levels. By comparing currents at both ends of the protected section, this protection scheme can detect even small imbalances caused by faults, thus providing accurate and reliable fault detection.
It’s important to note that the implementation and settings of protection schemes, including weak-feed line current differential protection, can vary based on the specific characteristics of the power system and the requirements of the application. Protection engineers and experts design and configure protection schemes to ensure the best performance and reliability for the given power system.
What are the advantages of the 1588v2 protocol?
The Precision Time Protocol (PTP), also known as IEEE 1588, is a protocol used for synchronizing clocks in networked systems. The IEEE 1588v2, the second version of the protocol, brings several advantages and improvements over the original version. Here are some of the key advantages of the IEEE 1588v2 protocol:
- High Precision Time Synchronization: IEEE 1588v2 is designed to provide extremely precise time synchronization, making it suitable for applications where accurate timing is critical, such as industrial automation, telecommunications, and financial trading systems.
- Sub-Microsecond Synchronization: IEEE 1588v2 is capable of achieving sub-microsecond synchronization accuracy, which is essential for applications requiring very tight synchronization tolerances.
- Hardware Timestamping Support: IEEE 1588v2 supports hardware timestamping, allowing network interface cards (NICs) and other hardware components to directly capture and timestamp packet arrival times. This reduces the variability introduced by software-based timestamping and improves synchronization accuracy.
- Fault Tolerance and Redundancy: IEEE 1588v2 includes mechanisms for dealing with network topology changes, failures, and redundancy scenarios. This helps maintain synchronization even when network paths change or components fail.
- Transparent Clocks: IEEE 1588v2 introduces the concept of “transparent clocks,” which are intermediate network devices that measure and compensate for the time delay introduced by the device itself. This is particularly useful in large-scale networks where accurate synchronization is needed across various network segments.
- Enhanced Best Master Clock Algorithm (BMCA): The BMCA in IEEE 1588v2 has been enhanced to better handle scenarios with multiple clocks vying for the role of the “best master clock.” This improves the accuracy and stability of the clock hierarchy in a network.
- Improved Security: IEEE 1588v2 includes security features to protect against unauthorized access and tampering of synchronization information. This is crucial in modern networked environments where security is a top concern.
- Management and Monitoring: IEEE 1588v2 defines mechanisms for management and monitoring of synchronization performance, allowing administrators to assess the health and accuracy of the synchronization system.
- Profile Extensions: IEEE 1588v2 includes profile extensions that tailor the protocol’s behavior to specific application requirements. This ensures that the protocol is adaptable and scalable across various use cases.
- Wide Applicability: IEEE 1588v2 can be applied to various industries, including industrial automation, telecommunications, broadcasting, financial services, and more, due to its high accuracy and adaptability.
Overall, IEEE 1588v2 addresses many of the limitations of the original protocol, providing enhanced accuracy, robustness, and features to meet the stringent synchronization requirements of modern networked systems.
Which of the following basic components does a typical wirelessHART network include?
A typical WirelessHART network includes the following basic components:
- WirelessHART Field Devices: These are the wireless sensors and actuators that collect data from the field, such as temperature, pressure, flow, and other process variables. These devices are equipped with wireless communication capabilities and follow the WirelessHART standard for communication.
- WirelessHART Gateway: The gateway serves as a bridge between the WirelessHART field devices and the central control system or monitoring station. It collects data from the field devices and relays it to the higher-level systems using wired communication protocols.
- WirelessHART Network Manager: The network manager is responsible for managing the overall operation of the WirelessHART network. It coordinates communication between the field devices, gateway, and other components. The network manager also handles tasks such as device configuration, network optimization, and security management.
- Central Control System or Monitoring Station: This is the main system where operators and engineers can view and analyze the data collected from the field devices. It provides a user interface for monitoring the process variables, configuring devices, setting alarms, and making decisions based on the collected data.
- Infrastructure: The infrastructure includes the physical components necessary to support the WirelessHART network, such as power supplies for field devices, power sources for the gateway, and the necessary networking equipment for connecting the gateway to the central control system.
- Security Mechanisms: WirelessHART networks incorporate security features to protect the communication and data exchanged between devices. This includes encryption, authentication, and other mechanisms to ensure the integrity and confidentiality of the transmitted data.
- Battery Management Systems (BMS): Since many field devices in WirelessHART networks are battery-powered, battery management systems may be included to monitor and manage the battery life of these devices. This helps ensure that the devices operate reliably over an extended period.
- Device Configuration Tools: These software tools are used to configure and manage the settings of the field devices in the network. They allow operators to set measurement ranges, update firmware, and configure communication parameters.
- Signal Conditioning and Processing: Depending on the specific application, signal conditioning and processing components may be included to ensure that the data collected from the field devices is accurate and useful for control and analysis.
These components work together to create a WirelessHART network that enables remote monitoring and control of industrial processes. The network’s wireless nature makes it suitable for scenarios where running wires is difficult or costly, and it provides the benefits of flexibility, scalability, and reduced installation time compared to traditional wired solutions.
What is the reset response process for an asynchronous IC card?
An asynchronous IC (Integrated Circuit) card, often referred to as a smart card or chip card, is a type of card with embedded integrated circuits that can store and process data. The reset response process for an asynchronous IC card refers to the sequence of actions that occur when the card’s microcontroller or processor receives a reset command. This reset process initializes the card and prepares it for communication with an external device, such as a card reader or terminal. Here’s a general outline of the reset response process for an asynchronous IC card:
- External Reset Request: The process begins when an external device, such as a card reader or terminal, sends a reset command to the IC card. This command informs the card’s microcontroller that it should reset itself and prepare for communication.
- Power-Up Phase: Upon receiving the reset command, the microcontroller within the IC card goes through a power-up phase. During this phase, the internal circuits are initialized, and the microcontroller’s internal components are powered up and set to their default states.
- Clock Generation: The microcontroller generates its internal clock signal to control the timing of its operations. The clock signal ensures that different components of the microcontroller work in synchronization.
- Identification and Initialization: The microcontroller then proceeds with the identification and initialization phase. It identifies the type of card it is (e.g., memory card, microprocessor card), and it may perform self-tests to ensure that its internal components are functioning correctly. The microcontroller may also establish communication protocols, such as protocols for data exchange and security features.
- Answer-to-Reset (ATR) Transmission: As part of the initialization process, the IC card generates an Answer-to-Reset (ATR) message. The ATR is a standardized response that contains information about the card, including its protocol, historical data, and status. The card sends this ATR message back to the external device, allowing the device to understand the card’s capabilities and characteristics.
- Protocol Negotiation: After sending the ATR, the card and the external device may engage in protocol negotiation. They determine the communication protocols they will use for subsequent interactions, such as the protocols for transmitting and receiving data.
- Ready State: Once the card completes its initialization and protocol negotiation, it enters a ready state. In this state, the card is prepared to respond to commands from the external device. The external device can now send various commands to read data from or write data to the card, perform authentication, and carry out other operations.
The specific steps and details of the reset response process can vary depending on the type of IC card, its microcontroller’s architecture, and the communication protocols it supports. It’s essential to refer to the card’s technical documentation to understand the exact behavior and processes involved in its reset response mechanism.
What are the advantages of the Karman scroll air flow sensor?
The Karman vortex street flow sensor, also known as the Karman vortex flow sensor, is a type of flow meter used to measure the flow rate of a fluid (usually a gas or a liquid) based on the generation and detection of vortex patterns behind an obstruction in the flow path. This technology offers several advantages:
- Non-Intrusive Design: Karman vortex flow sensors are non-intrusive, meaning they don’t obstruct the flow path or introduce pressure drops that can affect the flow characteristics. This is especially advantageous for applications where minimal disruption to the flow is crucial.
- Wide Range of Applications: These sensors can be used to measure the flow rates of various fluids, including gases and liquids, making them versatile for different industries and applications.
- Durable and Reliable: Karman vortex flow sensors have no moving parts, which enhances their durability and reduces maintenance requirements. This makes them suitable for applications where reliability is a top priority.
- Wide Range of Flow Rates: They are capable of measuring a wide range of flow rates, from low to high, without requiring significant recalibration.
- Accurate and Repeatable: Karman vortex flow sensors can provide accurate and repeatable flow measurements, especially when calibrated correctly.
- Insensitive to Fluid Properties: These sensors are relatively insensitive to fluid properties such as viscosity, temperature, and density, making them suitable for applications where fluid characteristics may vary.
- No Wear and Tear: Since there are no moving parts that come in contact with the fluid, wear and tear are minimal, contributing to the sensor’s long-term stability.
- Cost-Effective: Karman vortex flow sensors are often considered cost-effective compared to some other flow measurement technologies, especially for applications that require accurate measurements without high capital costs.
- Simple Installation: Installing Karman vortex flow sensors can be straightforward, especially when compared to more complex flow measurement technologies.
- Digital Output: Some modern Karman vortex flow sensors offer digital output options, making it easier to integrate them into digital control and monitoring systems.
- Low Maintenance: The lack of moving parts and minimal wear and tear contribute to low maintenance requirements, saving time and resources over the sensor’s lifespan.
- Suitable for Harsh Environments: Karman vortex flow sensors can be designed to withstand harsh environmental conditions, such as extreme temperatures or corrosive fluids.
While Karman vortex flow sensors have many advantages, they may also have limitations depending on the specific application. Factors such as pipe size, fluid type, and desired accuracy should be considered when choosing a flow measurement technology. It’s important to evaluate the suitability of the technology for your specific requirements and consult with experts if needed.
COMMENTS