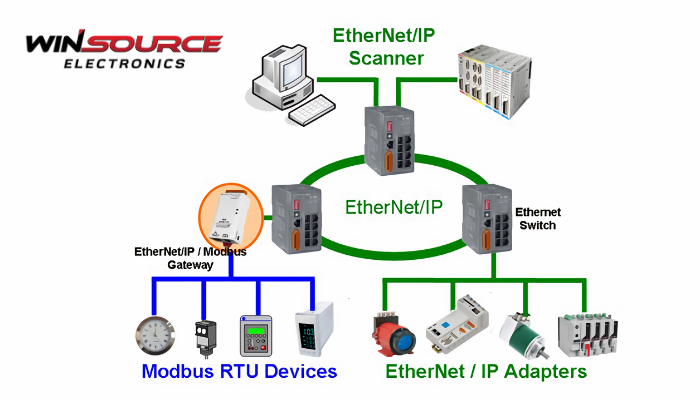
* Question
What are the common fieldbuses?
* Answer
Fieldbuses are industrial communication systems that connect field devices, such as sensors, actuators, and controllers, in an automation or control system. They are designed for real-time, deterministic communication and are widely used in industries such as manufacturing, process control, and power systems. Here are some of the most common fieldbuses:
1. PROFIBUS
– Description: Widely used in factory and process automation. Developed by Siemens and the PROFIBUS user organization.
– Variants:
– PROFIBUS DP: High-speed communication for factory automation.
– PROFIBUS PA: Focused on process automation, including hazardous environments.
– Key Features:
– Supports cyclic and acyclic communication.
– Robust and reliable in industrial environments.
2. Modbus
– Description: A simple and open protocol used for industrial devices, developed by Modicon.
– Variants:
– Modbus RTU: Uses serial communication (RS-485 or RS-232).
– Modbus TCP: Operates over Ethernet networks.
– Key Features:
– Easy to implement and widely adopted.
– Master/slave architecture.
3. CANopen
– Description: A higher-layer protocol based on the Controller Area Network (CAN), often used in embedded systems and industrial automation.
– Key Features:
– Real-time data exchange.
– Supports distributed control systems.
– Flexible and highly configurable.
4. DeviceNet
– Description: Based on CAN technology and used for industrial automation and control systems.
– Key Features:
– Low-cost network solution.
– Supports plug-and-play device interoperability.
5. Foundation Fieldbus
– Description: Focuses on process automation and control, enabling distributed control at the field device level.
– Variants:
– H1: Operates at lower speeds (31.25 kbps) for process control.
– HSE (High-Speed Ethernet): Operates at Ethernet speeds.
– Key Features:
– True distributed control architecture.
– Interoperability between devices from different manufacturers.
6. EtherCAT
– Description: An Ethernet-based fieldbus designed for high-speed and real-time communication, primarily used in motion control.
– Key Features:
– Extremely low latency.
– High synchronization accuracy.
– Scalable network topology.
7. Profinet
– Description: An Ethernet-based protocol that extends the PROFIBUS functionality for industrial Ethernet applications.
– Key Features:
– High performance and flexibility.
– Integrated safety and motion control features.
8. Interbus
– Description: A fieldbus system developed by Phoenix Contact, focused on cyclic data exchange in industrial automation.
– Key Features:
– Simple and fast setup.
– Supports long cable distances.
9. AS-Interface (AS-i)
– Description: A simple, low-cost bus system for connecting actuators and sensors.
– Key Features:
– Simplified wiring with a flat two-wire cable.
– Used in safety applications.
10. BACnet
– Description: Commonly used in building automation for HVAC, lighting, and access control.
– Key Features:
– Open standard.
– Supports a variety of transport layers, including Ethernet, IP, and MS/TP.
11. HART (Highway Addressable Remote Transducer)
– Description: Combines analog and digital communication over a standard 4–20 mA current loop.
– Key Features:
– Compatible with existing analog systems.
– Bi-directional communication.
12. LonWorks
– Description: Primarily used in building automation and control applications.
– Key Features:
– Peer-to-peer communication.
– Supports distributed intelligence.
13. SERCOS
– Description: A high-speed fieldbus designed for motion control applications.
– Key Features:
– Real-time deterministic communication.
– High synchronization for motion devices.
Summary:
Each fieldbus protocol has its strengths and is suited for specific applications. The choice of fieldbus depends on factors like:
– Speed and latency requirements.
– Application domain (e.g., factory automation, process control, or building automation).
– Cost and complexity.
– Device compatibility.
COMMENTS