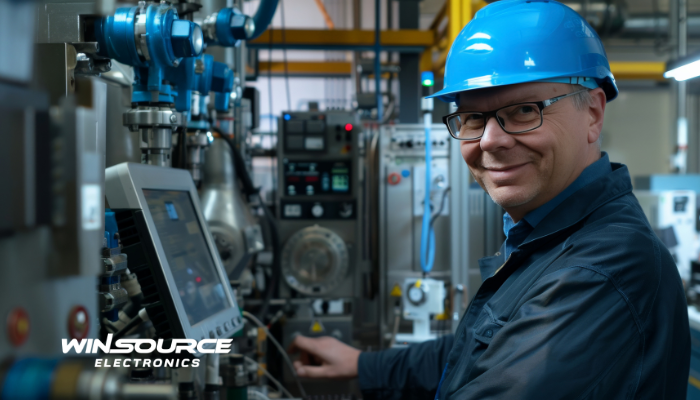
* Question
What are the components of the PLC’s power-on observation and what are the functions?
* Answer
A Programmable Logic Controller (PLC) is a robust computer used in industrial automation systems. Its primary role is to monitor inputs, make decisions based on its program, and control outputs to automate a process or machine. During the power-on sequence, observing certain components and their functions is crucial for ensuring the PLC operates correctly and safely. Here are the key components typically involved in a PLC’s power-on sequence, along with their functions:
1. Power Supply
– Function: Converts AC (alternating current) or DC (direct current) input into the voltages necessary to power the PLC and its components. It typically provides isolated power to different sections like the CPU, I/O modules, and communication modules.
2. CPU (Central Processing Unit)
– Function: Acts as the brain of the PLC, executing control instructions contained in the user program. Upon power-on, the CPU starts by performing a self-diagnosis, checking its own status and the integrity of its memory and firmware.
3. Memory
– Types and Functions:
– RAM (Random Access Memory): Volatile memory used for temporary storage of the user program, data, and intermediate calculations during operation.
– ROM (Read-Only Memory): Non-volatile memory that stores the PLC’s firmware and possibly the user program if it is intended to be immutable.
– EEPROM (Electrically Erasable Programmable Read-Only Memory): Used for storing and retrieving the user program and certain parameters that need to persist through power cycles.
4. I/O Modules
– Function: Interface the PLC to the external world. Input modules receive signals from sensors or human-machine interfaces, while output modules send signals to actuators or other devices. During power-on, these modules are checked for connectivity and functionality.
5. Communication Interfaces
– Function: Allow the PLC to communicate with other PLCs, computers, or network systems. Typical interfaces include Ethernet, RS-232, RS-485, and proprietary industrial networks. Initial communication tests may be conducted to ensure network interfaces are operational.
6. LED Indicators
– Function: Provide immediate visual feedback on the status of the PLC. Common indicators show power status, CPU status (error, running, halted), and communication status. Observing these indicators during power-on helps quickly diagnose problems.
7. Watchdog Timer
– Function: Monitors the PLC operation to ensure it is running correctly. If the CPU fails to reset the watchdog periodically, it indicates a malfunction, causing the watchdog to initiate a corrective action, such as a CPU reset.
8. Backup Battery
– Function: Maintains the power supply to the memory components (especially RAM) to prevent data loss during power failures. Checks during power-on ensure the battery is charged and functional.
During the power-on sequence, these components are typically checked systematically to confirm that all systems are operational, and the PLC is ready to execute its program reliably. This sequence is critical not only for the start-up but also for ensuring long-term reliability and safety of the PLC system in industrial applications.
COMMENTS