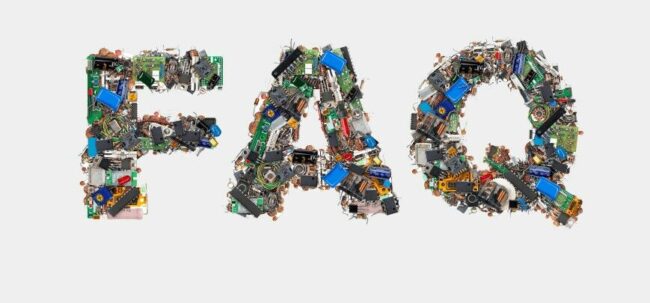
What is the protection scheme for the charging circuit of portable devices?
The protection scheme for the charging circuit of portable devices typically involves several key components and strategies to ensure safe and efficient charging. Here are some common elements of such a protection scheme:
- Overvoltage Protection: Circuitry is in place to prevent the voltage from exceeding safe limits during charging, which could damage the device or pose a safety risk.
- Overcurrent Protection: This safeguards against excessive current flowing through the circuit, preventing overheating or damage to the device’s battery and components.
- Temperature Monitoring: Sensors monitor the temperature of the battery and charging components to prevent overheating and potential thermal runaway.
- Short-Circuit Protection: The circuit includes measures to detect and prevent short circuits that could lead to damage or even fires.
- Voltage and Current Regulation: Charging circuitry regulates both voltage and current to ensure a steady and safe charging process, adapting to the device’s needs and capabilities.
- Battery Management System (BMS): In more advanced systems, a BMS might be employed to monitor and manage the battery’s state, ensuring optimal charging and preventing overcharging or undercharging.
- Charge Termination: The charging circuit detects when the battery is fully charged and terminates the charging process to prevent overcharging, which can degrade the battery over time.
- Reverse Polarity Protection: Measures are in place to prevent damage if the charging cable is connected with reverse polarity.
- EMI/EMC Filtering: To prevent electromagnetic interference and ensure compliance with regulatory standards, electromagnetic interference (EMI) and electromagnetic compatibility (EMC) filtering might be integrated.
- Authentication and Security: In some cases, security measures might be implemented to prevent unauthorized or potentially harmful devices from charging or accessing the device.
It’s important to note that the specific protection scheme can vary based on the design, capabilities, and intended use of the portable device. Manufacturers often prioritize safety, efficiency, and compliance with industry standards when designing the charging circuit protection scheme.
What are the characteristics of the ARM1176JZF-S processor?
The ARM1176JZF-S is a microprocessor core designed by ARM Holdings. It was a part of ARM’s ARM11 family of processors, which are widely used in various applications, including embedded systems, mobile devices, and consumer electronics. Here are some key characteristics of the ARM1176JZF-S processor:
- Architecture and Performance: The ARM1176JZF-S is based on the ARMv6 architecture. It features an in-order pipeline with a five-stage integer pipeline and a separate floating-point pipeline. Its performance is relatively modest compared to more recent architectures, making it suitable for low-power and embedded applications.
- Clock Speed: The clock speed of the ARM1176JZF-S processor can vary depending on the specific implementation and the intended application. It was commonly found in devices operating at speeds of a few hundred megahertz to around 1 GHz.
- Instruction Set: The processor supports the ARM and Thumb instruction sets, allowing for a balance between performance and code density. Thumb instructions are 16-bit compressed instructions that help conserve memory space.
- Floating-Point Unit (FPU): The processor includes a floating-point unit for handling floating-point operations, which is important for applications requiring numerical computations.
- Memory Management: It supports ARM’s Memory Management Unit (MMU), which allows for virtual memory and memory protection, enabling more advanced operating systems and multitasking.
- Caches: The processor typically features separate instruction and data caches, which help improve memory access speeds and overall performance.
- Vector Floating Point (VFP): Some implementations of the ARM1176JZF-S include the VFP extension, which provides improved floating-point performance for tasks such as multimedia processing.
- Jazelle Technology: The “J” in “JZF” stands for Jazelle technology, which allows for the execution of Java bytecode directly on the processor core.
- Multimedia Support: The ARM1176JZF-S processor includes features for multimedia processing, making it suitable for applications such as mobile phones, media players, and other devices requiring multimedia capabilities.
- Power Efficiency: The ARM1176JZF-S is designed with power efficiency in mind, making it suitable for battery-powered and portable devices.
It’s worth noting that the ARM1176JZF-S processor is an older architecture, and more recent ARM processor designs have surpassed its capabilities in terms of performance, energy efficiency, and feature set. However, during its time, it was widely used in a variety of devices and played a significant role in the embedded and mobile industries.
The working principle and use of the fuse:
A fuse is an electrical safety device designed to protect electrical circuits and devices from excessive current by breaking the circuit when the current exceeds a predetermined threshold. The working principle and use of a fuse are as follows:
Working Principle:
A fuse consists of a thin wire or strip of a material that has a low melting point, typically made of materials like copper, silver, or an alloy with a specific melting characteristic. The fuse is placed in series with the circuit that needs protection. When the current flowing through the circuit exceeds the rated current of the fuse, the heat generated by the excessive current causes the fuse wire to melt or blow, effectively breaking the circuit and interrupting the current flow.
The key principle behind this operation is the Joule heating effect: when electric current flows through a resistance (in this case, the fuse wire), heat is generated. If the current is too high, this heat can cause the fuse wire to melt, open the circuit, and prevent further current flow.
Use of Fuses:
- Overcurrent Protection: Fuses are primarily used to protect electrical circuits and devices from overcurrent situations. These situations can occur due to short circuits (low-resistance connections) or overloads (excessive current due to increased load). By breaking the circuit when such conditions occur, fuses prevent damage to equipment, fires, and potential hazards to people.
- Device and Component Protection: Fuses can be integrated into electronic devices and components to safeguard them from excessive current. For example, a power supply unit might have a fuse that protects the internal components from short circuits or overloads.
- Circuit and System Protection: Fuses are commonly used in electrical distribution panels to protect entire circuits or sections of a building’s electrical system. These fuses prevent overloads that could otherwise cause damage to wiring, appliances, or even the entire electrical network.
- Automotive Protection: Fuses are widely used in vehicles to protect various electrical systems, such as lights, radios, and other components. In case of a fault, the fuse will blow, preventing damage to the vehicle’s wiring or the components themselves.
- Industrial Applications: Fuses are essential in industrial settings to protect machinery, equipment, and systems from electrical faults. They ensure safe and reliable operation of industrial processes.
- Safety and Compliance: Fuses are part of safety measures required by electrical codes and standards. They play a role in ensuring that electrical systems are designed and operated safely.
It’s important to note that after a fuse blows due to an overcurrent situation, it needs to be replaced to restore circuit functionality. Modern circuit protection methods often include circuit breakers, which can be reset after they trip, unlike fuses, which need replacement.
What are the characteristics of the AT command set?
The features are simple, efficient, uniform command format, and easy to verify, but the disadvantage is that too much equipment details are involved, and more stringent timing requirements are usually required.
What are the channel interferences that degrade performance?
(1) In the case of a specific model of the frequency selective channel and the power line channel, the non-coherent demodulation of the maximum envelope detection is not optimal.
(2) Narrowband noise can cause a large envelope, and an error occurs at the output of the demodulator.(3) Impulse noise has a broadband characteristic, which may result in multiplication of large envelopes.
What is an AC motor?
An AC motor, or alternating current motor, is a type of electric motor that operates using alternating current as its power source. AC motors are widely used in various applications due to their efficiency, simplicity, and versatility. They work by converting electrical energy from an AC power source into mechanical energy, which can be used to drive various types of machinery, equipment, and devices.
There are several types of AC motors, but two of the most common categories are:
- Synchronous AC Motors: Synchronous AC motors operate at a fixed speed that is synchronized with the frequency of the AC power supply. They maintain a constant speed regardless of the load applied. Synchronous motors are often used in applications where precise speed control is important, such as in industrial machinery, synchronous clocks, and some types of fans.
- Asynchronous (Induction) AC Motors: Asynchronous AC motors, also known as induction motors, are the most common type of AC motor. They operate at a speed that is slightly less than the synchronous speed. Induction motors are self-starting and do not require any additional components to achieve rotation. They are known for their reliability, ruggedness, and ability to handle varying loads.
Key features and components of AC motors include:
- Stator: The stationary part of the motor that contains the primary winding. The stator’s magnetic field interacts with the rotor to induce motion.
- Rotor: The rotating part of the motor that can be either wound (squirrel-cage) or wound with coils (wound rotor). The rotor’s interaction with the stator’s magnetic field causes it to turn and generate mechanical output.
- Stator Windings: These windings are connected to the AC power supply and produce a rotating magnetic field when the motor is energized. The interaction between this field and the rotor’s magnetic properties generates torque and rotational movement.
- Rotor Bars (Squirrel-Cage Rotor): In a squirrel-cage rotor, the rotor consists of short-circuited bars made of conductive material. These bars interact with the rotating magnetic field, inducing currents that produce torque.
- Slip: The difference between the synchronous speed and the actual rotor speed in induction motors. Slip is necessary for generating the torque needed for the motor to operate.
- End Bells and Bearings: These components enclose the motor and support the rotor’s shaft. Bearings allow smooth rotation and reduce friction.
- Cooling: AC motors may have cooling mechanisms such as fans or vents to dissipate heat generated during operation.
AC motors are used in a wide range of applications, including industrial machinery, pumps, compressors, fans, conveyors, household appliances, HVAC systems, electric vehicles, and more. Their ability to efficiently convert electrical energy into mechanical motion makes them a fundamental component in modern technology and infrastructure.
What features are integrated in the ISL8601?
The ISL8601 also integrates a MOSFET driver circuit with built-in overcurrent, overvoltage, undervoltage, and overtemperature protection.
What are the characteristics of the three-axis accelerometer?
A three-axis accelerometer is a sensor that measures acceleration in three perpendicular axes: X, Y, and Z. It’s commonly used to detect changes in motion, orientation, and tilt. Here are the key characteristics and features typically associated with a three-axis accelerometer:
- Measurement Axes: A three-axis accelerometer measures acceleration in three mutually perpendicular directions: X, Y, and Z. This allows it to capture movement in three-dimensional space.
- Acceleration Range (Full Scale Range – FSR): This refers to the maximum acceleration magnitude that the sensor can accurately measure without saturation. It’s typically expressed in units of acceleration, such as “g” (gravity). For example, an FSR of ±2g means the sensor can measure accelerations up to 2 times the acceleration due to gravity in both positive and negative directions.
- Resolution: Resolution determines the smallest change in acceleration that the sensor can detect. It’s usually specified in terms of bits or a unit of acceleration, such as millig (mg). Higher resolution allows for more accurate detection of small movements.
- Sensitivity: Sensitivity refers to the change in sensor output per unit change in acceleration. It’s often expressed as mV/g (millivolts per gravity) or mV/mg (millivolts per milligravity).
- Output Type: Three-axis accelerometers can output analog voltage, analog current, or digital signals (such as I2C or SPI) representing the acceleration values.
- Bandwidth: Bandwidth is the range of frequencies over which the accelerometer’s response is accurate. It’s important for capturing fast changes in acceleration.
- Noise: Noise levels in the sensor’s output affect its ability to accurately measure small changes in acceleration. Lower noise levels result in more accurate measurements.
- Cross-Axis Sensitivity: Sometimes the measurement axes of an accelerometer aren’t perfectly orthogonal. Cross-axis sensitivity indicates how much acceleration along one axis might be measured on another axis.
- Digital Interface: If the accelerometer has a digital output, it will typically have an interface like I2C or SPI for communicating with microcontrollers or other devices.
- Temperature Range: The range of temperatures within which the accelerometer can operate effectively without significant drift or errors.
- Power Consumption: The amount of power the accelerometer consumes during operation, which is important for battery-powered applications.
- Form Factor and Mounting: The physical size and mounting options of the accelerometer can influence its integration into various systems.
- Built-in Features: Some three-axis accelerometers include additional features like built-in temperature sensors, self-test capabilities, and interrupt outputs that trigger based on specific acceleration thresholds.
- Accuracy and Calibration: The accuracy of the accelerometer’s measurements can vary. Some accelerometers might require calibration to correct for inaccuracies.
- Application Suitability: The accelerometer’s characteristics determine its suitability for different applications, such as automotive safety systems, industrial equipment, consumer electronics, navigation systems, motion detection, and more.
Remember that specific three-axis accelerometers from different manufacturers might have varying specifications and capabilities. When selecting an accelerometer for a particular application, it’s important to consider the characteristics that align with the requirements of your project. Always refer to the manufacturer’s datasheet for accurate and detailed information about the sensor’s features.
What is the role of the inverter?
An inverter is an electrical device that converts direct current (DC) to alternating current (AC). It plays a crucial role in various applications where AC power is needed, especially in situations where the power source provides DC voltage. The primary function of an inverter is to change the electrical characteristics of the power supply to meet the requirements of AC-powered devices and systems. Here are some key roles and applications of inverters:
- Power Conversion for AC Devices: Many electrical devices and appliances, such as household appliances, industrial machines, and electronic equipment, require AC power to operate. Inverters allow DC sources, like batteries, solar panels, or rectified AC (such as from generators), to power these devices by converting the DC voltage to AC voltage.
- Solar Power Systems: In photovoltaic (PV) solar power systems, solar panels generate DC electricity from sunlight. Inverters are used to convert this DC power into grid-compatible AC power that can be used by homes, businesses, and the utility grid.
- Wind Power Systems: Similar to solar power, wind turbines generate DC power that needs to be converted to AC power using inverters for use in the electrical grid.
- Uninterruptible Power Supplies (UPS): Inverters are a key component of UPS systems, which provide temporary backup power during utility power outages. The inverter converts stored DC power (from batteries) into AC power to keep critical devices and systems running.
- Electric Vehicles (EVs): Electric vehicles use inverters to convert the DC power from the vehicle’s battery into AC power for the electric motor. This allows precise control of the motor’s speed and torque.
- Motor Drives and Control: Inverters are used in motor drives to control the speed and direction of AC motors. They convert fixed-frequency AC power to variable-frequency AC power, enabling efficient motor control and energy savings.
- Grid Interconnection: Inverters are used to connect renewable energy sources (such as solar panels and wind turbines) to the utility grid. Grid-tied inverters synchronize the generated AC power with the grid’s frequency and voltage levels.
- Frequency Conversion: Inverters can be used to change the frequency of the output AC power. This is particularly useful in situations where different regions use different AC frequencies (e.g., 50 Hz or 60 Hz).
- Inductive Load Compatibility: Inverters can provide clean and stable AC power that is better suited for powering sensitive electronics and devices that are sensitive to voltage fluctuations.
- Emergency Power: In emergency situations, inverters can be used to convert power from backup sources (such as generators) into usable AC power.
Inverters come in various types, such as square wave, modified sine wave, and pure sine wave inverters, which differ in terms of the quality and characteristics of the AC waveform they produce. The specific type of inverter chosen depends on the application’s requirements and the devices being powered.
Which events can also clear the flag of the CPU interrupt flag register?
In a microcontroller or microprocessor, the CPU interrupt flag register (also known as the Interrupt Status Register or similar names depending on the architecture) keeps track of pending interrupts. Clearing the interrupt flag is essential to acknowledge that the interrupt request has been handled by the CPU. Besides explicitly clearing the flag in the interrupt service routine (ISR), several events or conditions can also clear the flag automatically:
- Hardware Interrupt Acknowledgment: When the CPU acknowledges an external hardware interrupt, it typically clears the corresponding interrupt flag in the interrupt flag register.
- Timer or Counter Overflow: Many microcontrollers have built-in timers or counters. These modules can generate interrupts when they overflow from their maximum value back to zero. Acknowledging this interrupt often clears the corresponding interrupt flag.
- Input Capture: In microcontrollers with input capture functionality, an interrupt can be generated when a specific edge (rising or falling) is detected on an input signal. Acknowledging this interrupt can clear the flag.
- UART or Serial Communication: When data is received or transmitted via a UART (Universal Asynchronous Receiver-Transmitter), an interrupt can be generated. Acknowledging the interrupt typically clears the flag.
- ADC (Analog-to-Digital Converter) Conversion Complete: In microcontrollers with ADC modules, an interrupt can be triggered when an analog-to-digital conversion is complete. Clearing this interrupt often clears the corresponding flag.
- DMA (Direct Memory Access) Transfer Completion: In systems with DMA controllers, an interrupt can be generated when a DMA transfer is complete. Acknowledging the interrupt usually clears the flag.
- Communication Protocols (I2C, SPI, etc.): Similar to UART, other communication protocols like I2C or SPI can generate interrupts when data is received or transmitted. Acknowledging the interrupt often clears the flag.
- Comparator Events: In microcontrollers with analog comparator modules, events like a specific voltage level being reached can generate interrupts. Acknowledging the interrupt can clear the corresponding flag.
- Watchdog Timer Reset: In systems with watchdog timers, if the timer reaches its timeout value, it can generate a reset or an interrupt. Acknowledging this interrupt can clear the flag.
- External Reset or Power-On Reset: When the microcontroller resets, it might clear some or all of the interrupt flags, depending on the architecture and configuration.
It’s important to note that the specific behavior can vary depending on the microcontroller or microprocessor architecture. Always refer to the device’s datasheet or reference manual to understand the exact behavior of the interrupt flag register and the conditions under which flags are cleared.
COMMENTS