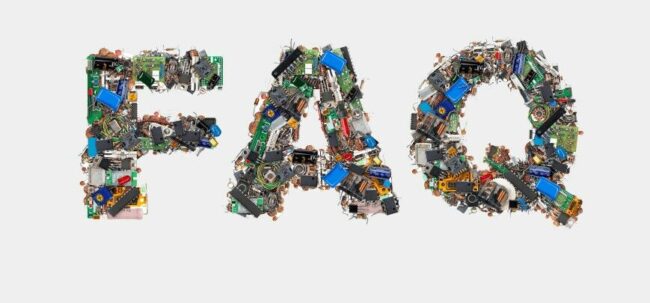
What is the main component of the computing component?
The main component of a computing system is the Central Processing Unit (CPU). The CPU is often referred to as the “brain” of the computer because it is responsible for executing instructions and performing calculations that drive the computer’s operation. It fetches, decodes, and executes program instructions and manages data processing tasks.
The CPU is typically composed of various subcomponents, including the Arithmetic Logic Unit (ALU), the Control Unit, and registers. The ALU performs mathematical and logical operations, while the Control Unit manages the execution of instructions and the flow of data within the CPU.
In addition to the CPU, other important components of a computing system include memory (RAM), storage devices (e.g., hard drives and SSDs), input/output devices (e.g., keyboard, mouse, monitor), and the motherboard, which connects and facilitates communication between these components. Together, these components work in tandem to enable a computer to perform various tasks and run software applications.
What is the LTC3440?
The LTC3440 is a specific integrated circuit (IC) or voltage regulator manufactured by Linear Technology, which is now a part of Analog Devices, Inc. The LTC3440 is designed to be a high-efficiency, low-noise, synchronous buck-boost DC-DC converter. It is primarily used to step up or step down voltage levels efficiently in various electronic applications.
Here are some key features and functions of the LTC3440:
- Voltage Regulation: The LTC3440 can regulate the output voltage to a specific level, which can be higher or lower than the input voltage, making it suitable for a wide range of power supply applications.
- Synchronous Operation: It employs synchronous rectification, which improves efficiency by reducing power loss during voltage conversion.
- Low Quiescent Current: The LTC3440 is designed to operate with very low quiescent current, making it suitable for battery-powered or energy-efficient devices.
- Wide Input Voltage Range: It can accept a wide range of input voltages, making it versatile for various power supply designs.
- Adjustable Output Voltage: Many versions of the LTC3440 allow you to adjust the output voltage to meet the specific requirements of your application.
- Protection Features: It often includes protection features like overcurrent protection, thermal shutdown, and undervoltage lockout to safeguard the circuit and connected components.
- Small Package: The LTC3440 typically comes in compact surface-mount packages, which is advantageous for space-constrained designs.
Please note that the specifications and features of specific ICs can vary depending on the model and version. If you are planning to use the LTC3440 in a project, it’s essential to refer to the datasheet for the specific version you are working with to understand its detailed characteristics and how to use it effectively in your application.
What are the main directives provided by ARM?
ARM, which stands for Advanced RISC Machines, is a company known for designing and licensing microprocessor and microcontroller architectures. ARM provides a set of architectural principles and directives that serve as the foundation for the design of their processors. Some of the main directives and principles provided by ARM include:
- RISC Architecture: ARM processors are based on the Reduced Instruction Set Computer (RISC) architecture. RISC emphasizes simplicity and a small set of instructions that can be executed in a single clock cycle, which leads to improved performance and power efficiency.
- Load-Store Architecture: ARM processors use a load-store architecture, which means that data processing operations are performed on registers, and memory operations (loads and stores) are separate instructions. This design simplifies instruction execution and enhances performance.
- Uniform Instruction Set: ARM processors maintain a uniform instruction set across different processor versions and architectures, making it easier for developers to write software that can run on a wide range of ARM-based devices.
- Pipeline Architecture: ARM processors often employ pipeline architectures, allowing multiple instructions to be processed simultaneously and improving overall throughput.
- 32-bit and 64-bit Architectures: ARM provides both 32-bit and 64-bit architectures. The ARMv7-A and ARMv8-A architectures are commonly used for 32-bit and 64-bit applications, respectively.
- Thumb and Thumb-2 Instruction Sets: ARM processors often support the Thumb and Thumb-2 instruction sets, which are designed to reduce code size and improve code density for embedded and mobile applications.
- Power Efficiency: ARM has a strong focus on power efficiency, making their processors suitable for battery-powered devices and embedded systems where power consumption is critical.
- Scalability: ARM architectures are scalable, allowing for a wide range of processor cores with different performance levels and capabilities. This scalability makes ARM processors versatile for various applications, from simple microcontrollers to high-performance servers.
- Instruction Set Extensions: ARM architectures can include optional instruction set extensions, such as SIMD (Single Instruction, Multiple Data) and floating-point instructions, to enhance their capabilities for specific tasks.
- Compatibility: ARM architectures often maintain backward compatibility with earlier versions, ensuring that software developed for older ARM-based systems can still run on newer processors.
- Security Features: ARM processors may incorporate security features and extensions to address the growing concerns about system and data security.
It’s important to note that ARM provides architectural specifications and licenses its designs to various semiconductor companies, which then manufacture ARM-based processors. As a result, you can find ARM processors in a wide range of devices, from smartphones and tablets to embedded systems and servers, each tailored to specific applications and performance requirements.
How is the action-triggered application of power management implemented?
Action-triggered power management, often referred to as power management based on events or triggers, involves adjusting the power state of a device or component in response to specific events or conditions. This approach aims to optimize power consumption by powering down or adjusting the power levels of various hardware components when they are not actively needed, and then powering them up or restoring their power levels when required. The implementation of action-triggered power management typically involves the following steps:
- Event Detection and Monitoring:
- Identify the events or triggers that will drive power management decisions. These events can include user interactions, system activities, sensor data, timers, or other external inputs.
- Implement monitoring mechanisms to continuously track and detect these events or conditions. This may involve hardware interrupts, software polling, or event-driven programming.
- Power State Management:
- Define a set of power states for the device or its components. These power states may range from fully active (high power consumption) to various levels of sleep or low-power states.
- Determine the criteria for transitioning between power states. For example, a device might transition to a low-power state when it’s idle for a certain period or when specific sensors detect inactivity.
- Event-Triggered Actions:
- Implement actions or routines that respond to specific events or triggers. These actions should include instructions to change the power state of relevant hardware components.
- When an event is detected, the associated action is executed. This action may involve transitioning certain components to a lower-power state or powering them down completely.
- Wake-Up Mechanisms:
- Consider how the device or component will be awakened from a low-power state when needed. This might involve using wake-up timers, external interrupts, or communication from other devices or systems.
- When an event or user action requires the device’s functionality, the wake-up mechanism is triggered, and the device transitions back to an active state.
- Fine-Tuning and Optimization:
- Continuously monitor the power management system’s performance and power consumption patterns.
- Make adjustments and optimizations to the power management policies and algorithms as needed to strike a balance between power savings and responsiveness.
- Testing and Validation:
- Thoroughly test the power management system under various scenarios and conditions to ensure that it functions correctly and reliably.
- Validate that the power management actions align with the intended power-saving goals without sacrificing the user experience or system performance.
- Documentation and Logging:
- Maintain documentation of the power management policies, event-triggered actions, and their corresponding power state transitions.
- Implement logging and reporting mechanisms to track power management events and system performance over time for analysis and optimization.
The specific implementation of action-triggered power management can vary widely depending on the type of device, operating system, and hardware components involved. It is a critical aspect of designing energy-efficient systems, especially in battery-powered devices and systems where power conservation is a primary concern.
What is the basic working principle of RFID?
RFID, which stands for Radio-Frequency Identification, is a technology that uses radio waves to identify and track objects, animals, or people. The basic working principle of RFID involves three main components: RFID tags, RFID readers (also known as interrogators), and a computer system. Here’s how RFID works:
- RFID Tags:
- RFID tags are small electronic devices that contain information or data about an object, such as its unique identification number or other relevant data.
- These tags can be passive, active, or semi-passive (also called battery-assisted passive), each with its own power source and capabilities.
- Passive RFID tags do not have their power source and rely on the energy transmitted by the RFID reader to operate. Active tags have their power source (usually a battery) and can transmit signals independently. Semi-passive tags have a small battery to power certain features but still rely on the reader for communication power.
- RFID Readers:
- RFID readers are devices that emit radio frequency signals and receive responses from RFID tags.
- The reader sends out a radio frequency (RF) signal, which is also known as an “interrogation” or “query.”
- The RF signal contains a specific code or command that instructs nearby RFID tags to respond.
- Communication:
- When an RFID tag receives the RF signal from the reader, it uses the energy from the signal (in the case of passive tags) to activate its internal circuitry.
- The RFID tag then responds by transmitting its stored information back to the reader. This information may include the tag’s unique identification number or other data.
- The communication between the reader and the tag typically occurs at a specific radio frequency within the RFID spectrum.
- Data Processing:
- The RFID reader captures the data transmitted by the RFID tag.
- The reader can decode the data, which may include the tag’s identification number or other information, and send it to a computer system or software for further processing and interpretation.
- Database Lookup:
- The computer system, connected to the RFID reader, looks up the data received from the RFID tag in a database.
- The database provides context and information associated with the tagged object, such as its location, status, or history.
- Action or Decision:
- Based on the information retrieved from the RFID tag and the database, the computer system can trigger actions or decisions. This might involve updating inventory records, granting access, tracking the movement of goods, or any other relevant task.
In summary, RFID technology uses radio waves to enable wireless identification and tracking of objects or entities. RFID tags respond to RF signals from RFID readers, transmitting their stored data, which is then processed and used to make decisions or perform actions by computer systems. RFID has a wide range of applications, including asset tracking, access control, inventory management, and more.
What features does dynamic power management technology offer?
Dynamic Power Management (DPM) technology offers several features and capabilities that are designed to optimize the power consumption of electronic devices and systems, particularly in situations where power efficiency is crucial. These features may vary depending on the specific implementation and the hardware and software involved, but here are some common features offered by DPM technology:
- Voltage and Frequency Scaling:
- DPM allows for dynamic adjustment of the operating voltage and clock frequency of the processor or components based on the workload. This feature, known as Dynamic Voltage and Frequency Scaling (DVFS), helps save power when the device’s performance requirements are low.
- Idle States (Sleep Modes):
- DPM technology enables the device or individual components to enter low-power sleep states when they are not actively processing tasks. These idle states reduce power consumption while maintaining quick wake-up times.
- Task Scheduling:
- DPM can prioritize and schedule tasks to efficiently allocate processing resources. For example, it can group tasks together to allow the processor to enter a low-power state between bursts of activity.
- Peripheral Power Control:
- DPM can selectively power down or reduce the power consumption of peripheral devices, such as USB ports, Wi-Fi modules, or sensors, when they are not in use.
- Dynamic GPU Voltage and Frequency Scaling:
- In systems with dedicated graphics processing units (GPUs), DPM technology can adjust the GPU’s voltage and clock frequency to match the graphical workload, reducing power consumption during less demanding tasks.
- Adaptive Brightness and Display Management:
- DPM can adjust the screen brightness and resolution dynamically based on ambient light conditions and user preferences to save power on devices with displays.
- Sensor-Based Power Management:
- Devices equipped with sensors (e.g., motion, proximity, ambient light) can use DPM to respond to sensor inputs efficiently. For instance, a device can wake up when it detects motion and enter sleep mode when not in use.
- Temperature and Thermal Management:
- DPM technology can monitor and manage the device’s temperature by adjusting performance levels or even temporarily shutting down components if they become too hot to prevent damage.
- Battery Optimization:
- On battery-powered devices, DPM can help extend battery life by intelligently managing power consumption, including limiting background processes and optimizing connectivity.
- User Profiles and Power Modes:
- DPM can offer different power profiles or modes that users can select based on their preferences. These profiles may prioritize performance, power efficiency, or a balance between the two.
- Predictive Power Management:
- Some advanced DPM systems use predictive algorithms to anticipate future workload and power requirements, allowing for proactive power management.
- Energy-Aware Software:
- DPM technology often requires collaboration between hardware and software. Energy-aware software can adjust its behavior based on the device’s power management capabilities.
- Remote Management and Control:
- In networked or IoT (Internet of Things) devices, DPM can be remotely managed and controlled to optimize power consumption across a fleet of devices.
Overall, DPM technology plays a vital role in improving energy efficiency, extending battery life, and reducing heat generation in electronic devices and systems, making it essential for modern mobile devices, laptops, servers, and embedded systems.
What is the original generation of interference signals?
Interference signals, also known as interference or noise, can originate from various sources in electronic and communication systems. These signals can disrupt the intended transmission or processing of information. The original generation of interference signals typically occurs due to one or more of the following factors:
- Electromagnetic Interference (EMI):
- EMI results from electromagnetic fields generated by electronic devices and circuits. These fields can couple with nearby circuits or cables, inducing unwanted voltage and current in them. Common sources of EMI include switching power supplies, motors, radio transmitters, and electronic devices with rapidly changing currents.
- Radio-Frequency Interference (RFI):
- RFI is a subset of EMI that specifically involves interference in the radio frequency (RF) spectrum. This interference can come from various sources, including nearby radio transmitters, mobile phones, and other wireless communication devices.
- Crosstalk:
- Crosstalk occurs when signals from one circuit or transmission line unintentionally couple into adjacent circuits or lines. This can happen due to capacitive or inductive coupling, especially in tightly packed electronic systems or cables.
- Impulse Noise:
- Impulse noise consists of short-duration, high-amplitude spikes or transients in a signal. It can result from various events, such as lightning strikes, power surges, or sudden voltage changes in electrical circuits.
- Thermal Noise:
- Thermal noise, also known as Johnson-Nyquist noise, arises from the random motion of electrons in conductors at finite temperatures. It is a fundamental source of noise in electronic circuits and communication systems.
- Shot Noise:
- Shot noise is caused by the discrete nature of charge carriers (e.g., electrons) in electronic devices. It is particularly relevant in low-current or high-frequency applications.
- Phase Noise:
- Phase noise is a form of noise that affects the stability of oscillators and signal sources. It results in random fluctuations in the phase of an oscillating signal and can degrade the performance of communication systems.
- Intermodulation Distortion (IMD):
- IMD occurs when two or more signals at different frequencies mix in a non-linear component or system, producing unwanted sum and difference frequencies. These additional frequencies can interfere with desired signals.
- External Interference:
- External factors, such as natural phenomena (e.g., thunderstorms), nearby electrical equipment, or man-made sources (e.g., machinery), can introduce interference into electronic systems and communication channels.
- Intentional Jamming:
- In some cases, interference signals are generated intentionally to disrupt communication or electronic systems. This can be done for malicious purposes, such as jamming radio signals or interfering with wireless networks.
Mitigating interference signals is a critical consideration in the design and operation of electronic and communication systems. Techniques such as shielding, filtering, grounding, and error-correction coding are used to reduce the impact of interference and ensure reliable signal transmission and processing.
What are the methods of load management?
Load management refers to the strategies and techniques employed to efficiently control and distribute electrical power to meet the demand while optimizing energy use and avoiding grid overloads. Load management is crucial for maintaining the stability and reliability of electrical grids and reducing energy costs. There are several methods and approaches to load management:
- Peak Shaving:
- Peak shaving involves reducing energy consumption during periods of high electricity demand, typically during peak hours. This can be achieved by implementing demand response programs, shifting non-essential loads to off-peak hours, or using energy storage systems to provide power during peak periods.
- Demand Response Programs:
- Demand response programs allow utility companies to communicate with consumers or automated systems to curtail electricity usage during peak demand times. Customers are incentivized to reduce their electricity consumption temporarily in exchange for lower rates or other benefits.
- Load Shedding:
- Load shedding is a controlled reduction of electrical load during times of high demand or grid instability. It involves disconnecting non-critical loads to prevent blackouts or brownouts. Load shedding can be manual or automated, depending on the system’s design.
- Time-of-Use (TOU) Pricing:
- TOU pricing encourages consumers to shift their electricity usage to off-peak hours when electricity rates are lower. This approach incentivizes users to perform energy-intensive tasks, such as laundry or charging electric vehicles, during times of reduced demand.
- Load Leveling:
- Load leveling aims to maintain a more constant and predictable load profile by spreading out electricity consumption more evenly over time. This can be achieved by using energy storage systems or scheduling processes to avoid sharp spikes in demand.
- Energy Storage:
- Energy storage systems, such as batteries or flywheels, can store excess electricity during periods of low demand and discharge it during peak demand times. This helps stabilize the grid and reduce the need for additional power generation.
- Distributed Generation:
- Distributed generation refers to the production of electricity at or near the point of consumption. This can include renewable energy sources like solar panels or small-scale gas generators. Distributed generation can reduce the strain on the grid during peak demand.
- Load Profiling and Monitoring:
- Load profiling involves analyzing historical electricity usage patterns to identify opportunities for load management. Advanced monitoring and analytics tools can help businesses and utilities optimize their energy consumption.
- Smart Grid Technologies:
- Smart grid technologies incorporate advanced sensors, communication systems, and automation to monitor and control electricity flow in real-time. This allows for more precise load management and integration of renewable energy sources.
- Voltage Regulation:
- Maintaining stable voltage levels can improve the efficiency of electrical equipment and reduce energy consumption. Voltage optimization systems adjust voltage levels to match the actual requirements of connected devices.
- Load Balancing:
- Load balancing involves evenly distributing electrical loads across different phases of the grid to prevent phase imbalances and reduce energy losses.
- Energy Efficiency Measures:
- Implementing energy-efficient technologies and practices, such as LED lighting, HVAC system upgrades, and insulation improvements, can reduce overall energy consumption and the need for load management.
The specific methods of load management chosen will depend on the goals of the utility or organization, the available infrastructure, and the local regulatory environment. Effective load management can help reduce energy costs, minimize environmental impact, and enhance grid reliability.
How do dual LD0 chips achieve the goal of reducing power consumption?
Dual LD0 chips (Low-Dropout Voltage Regulators) are typically used in electronic circuits to help reduce power consumption by providing efficient voltage regulation for low-power devices. These chips, often referred to as “dual” because they have two voltage regulator outputs, can help save power in several ways:
- Voltage Regulation:
- Dual LD0 chips are primarily designed to provide stable and regulated voltage outputs. By ensuring that the voltage supplied to the connected devices remains constant and within the required range, they prevent overvoltage or undervoltage conditions that can lead to power wastage or damage to sensitive components.
- Low Dropout Voltage:
- LD0 regulators are known for their low dropout voltage, which means they can operate with a very small voltage difference between the input and output. This feature is especially useful when the input voltage is close to the desired output voltage, as it minimizes power dissipation within the regulator.
- Efficiency:
- Dual LD0 chips are designed to be highly efficient. They can convert a higher input voltage to a lower output voltage with minimal power loss in the form of heat. This efficiency is achieved through the use of low-dropout voltage designs and efficient circuit topologies.
- Reduced Standby Power:
- In many applications, devices spend a significant amount of time in standby or sleep modes. Dual LD0 chips can help reduce power consumption during these idle periods by regulating voltage levels efficiently. When the device is not actively drawing power, the regulator minimizes its own power consumption.
- Low Quiescent Current:
- LD0 regulators often have low quiescent or ground current, which is the current drawn by the regulator when no load is connected. This helps minimize power wastage when the connected device is in standby or low-power modes.
- Dual Output Flexibility:
- The dual output feature of these chips allows for the regulation of two different voltage levels simultaneously. This can be beneficial in applications where multiple voltage rails are required, such as powering both digital and analog components or providing different voltage levels for different parts of a circuit. This reduces the need for additional voltage regulators and associated losses.
- Thermal Protection:
- Many LD0 regulators have built-in thermal protection mechanisms that prevent the chip from overheating. This not only enhances reliability but also helps maintain efficiency by preventing excessive power dissipation due to heat.
- Load Balancing:
- In dual LD0 configurations, it’s possible to balance the load between the two outputs. This can help distribute power more efficiently and prevent one regulator from working significantly harder than the other, which can improve overall efficiency.
In summary, dual LD0 chips reduce power consumption by providing efficient and stable voltage regulation for electronic devices, particularly in low-power applications. They achieve this by minimizing dropout voltage, operating with high efficiency, and offering features like low quiescent current and thermal protection. These characteristics make them valuable components for power management in battery-powered devices, portable electronics, and low-power systems.
Which modules does the reader consist of?
An RFID (Radio-Frequency Identification) reader typically consists of several modules and components that work together to communicate with RFID tags and retrieve data. The specific modules and components can vary depending on the reader’s type and capabilities, but here are some common modules and their functions:
- RFID Antenna:
- The RFID antenna is a critical component that emits radio frequency signals (RF signals) and receives responses from RFID tags. The antenna’s design and size affect its read range and efficiency.
- RFID Transceiver:
- The transceiver is responsible for transmitting RF signals generated by the reader to the RFID tags and receiving signals from the tags. It modulates the signals for transmission and demodulates received signals for data extraction.
- Microcontroller or Processor:
- A microcontroller or processor is the brain of the RFID reader. It controls the overall operation of the reader, manages communication protocols, processes data, and interfaces with other peripherals.
- Memory:
- Some RFID readers have built-in memory for storing tag data, configuration settings, and other information. This memory can be used for buffering data before transmitting it to an external system.
- Power Supply:
- The power supply module provides the necessary electrical power to operate the reader and its components. Depending on the application, RFID readers may be powered by batteries, AC power sources, or PoE (Power over Ethernet).
- Interface Ports:
- RFID readers often feature various interface ports for connecting to external devices or networks. Common interface options include USB, Ethernet, RS-232, RS-485, and GPIO (General Purpose Input/Output) pins.
- Control and Display Unit:
- In some RFID readers, there may be a control unit with a user interface, such as a touchscreen, buttons, or an LED display. This allows users to configure the reader, initiate operations, and view status information.
- Communication Protocols:
- The reader may support various communication protocols to interface with external systems, such as RFID middleware, databases, or control software. Common protocols include TCP/IP, HTTP, MQTT, and custom data formats.
- Firmware/Software:
- RFID readers are often equipped with firmware or software that controls their behavior, manages data, and handles communication. Some readers can be configured and updated using software tools.
- Synchronization and Timing:
- Timing and synchronization modules ensure that the reader’s operations are properly timed and synchronized with tag responses, especially in multi-tag environments.
- Security Features:
- Depending on the application, RFID readers may include security modules to protect against unauthorized access, data encryption, and authentication.
- Antenna Multiplexer (for Multiple Antennas):
- In RFID systems with multiple antennas, an antenna multiplexer is used to switch between antennas or use them simultaneously. This can improve read efficiency and coverage.
- Environmental Sensors (Optional):
- Some specialized RFID readers may include environmental sensors to monitor conditions like temperature, humidity, or motion in the vicinity of the reader.
The specific modules and features of an RFID reader can vary widely based on its intended use case, frequency range (e.g., LF, HF, UHF, or NFC), and complexity. RFID readers are employed in various applications, including asset tracking, access control, inventory management, and logistics, each requiring different capabilities and configurations.
COMMENTS