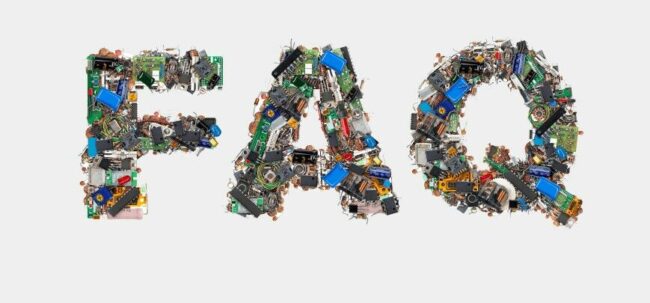
What are the technical characteristics of the CAN bus?
The Controller Area Network (CAN) bus is a widely used communication protocol in the automotive and industrial automation industries. It was originally developed by Bosch for automotive applications but has since found use in various other domains. Here are the key technical characteristics of the CAN bus:
- Topology: CAN bus supports a multi-master, multi-drop network topology. This means that multiple devices (nodes) can be connected to the same bus, and each node can both send and receive messages. There is no single central controller; all nodes are equal.
- Bitrate: CAN bus allows for different bitrate configurations, typically ranging from 10 kbps (kilobits per second) up to 1 Mbps (megabit per second) or even higher in some cases. The choice of bitrate depends on the specific application’s requirements for data transfer speed and distance.
- Message Format: CAN messages consist of two primary components: the identifier (or message ID) and the data. The identifier is used to determine the message’s priority, and the data contains the actual information being transmitted. CAN messages can be either standard (11-bit identifier) or extended (29-bit identifier), which allows for a large number of unique message identifiers.
- Message Frame: CAN uses two message frame formats: the Data Frame (CAN Data Frame) and the Remote Frame (CAN Remote Frame). The Data Frame contains actual data and is used for transmitting information. The Remote Frame is used to request data from another node and does not contain data itself.
- Error Handling: CAN is designed to be highly robust. It employs a sophisticated error detection and error handling mechanism. Error detection includes mechanisms like CRC (Cyclic Redundancy Check), and when an error is detected, the CAN controller can take corrective actions like retransmitting messages or logging error frames.
- Arbitration: CAN uses a priority-based arbitration mechanism. When multiple nodes try to transmit messages simultaneously, the one with the highest priority (determined by the identifier) gains access to the bus. This ensures that critical messages have a higher chance of being transmitted without collisions.
- Synchronization: CAN nodes synchronize their clocks to the edges of incoming bits. This is crucial for proper bit timing and helps in maintaining synchronization even in the presence of variations in clock frequencies.
- Message Broadcasting: Messages on a CAN bus are broadcasted to all nodes. Each node decides whether to accept or ignore a message based on its identifier. This broadcasting mechanism makes CAN efficient for sharing information across multiple nodes.
- Message Prioritization: CAN supports a fixed-priority message scheduling scheme. Messages with lower identifiers (higher priority) get transmitted before messages with higher identifiers (lower priority). This ensures that critical messages are not delayed by less critical ones.
- Low Overhead: CAN has relatively low overhead for message transmission. This makes it suitable for real-time applications where rapid communication is essential.
- Error Detection and Reporting: CAN provides error flags and counters that allow nodes to detect and report various types of errors, such as bit errors, frame errors, and acknowledge errors.
- Termination: CAN bus requires termination resistors at both ends of the bus to minimize signal reflections and ensure signal integrity.
Overall, the technical characteristics of the CAN bus make it a reliable and widely adopted protocol for communication in environments where robustness, real-time capabilities, and multi-node communication are essential, such as automotive systems, industrial automation, and more.
What are the conclusions of the test analysis?
(1) The level of the signal transmitted on the CAN bus of the body comfort system is consistent with the nominal value of the signal level defined by IS0. The data transmission rate is 62.5 kb/s, which belongs to Volkswagen’s second generation body comfort system.3) CAN bus In the case of analog bus faults related to CAN-H and CAN-L short circuit and open circuit, the signals on the CAN bus can be transmitted in a single line mode, and the bus works in single line mode.
What are the general analysis methods for control circuits?
Analyzing control circuits typically involves examining the electrical and logical components of a system to ensure it functions as intended. This is common in industrial automation, electronics, and electrical engineering. Here are some general analysis methods for control circuits:
- Visual Inspection: A visual inspection is the first step in analyzing a control circuit. It involves examining the circuit’s components, connections, and wiring to check for physical damage, loose connections, or other visible issues.
- Circuit Diagram Review: Review the circuit diagram or schematic to understand the logic and connections within the circuit. Ensure that the diagram matches the physical circuit and that there are no discrepancies.
- Functional Testing: Perform functional testing to verify that the control circuit performs its intended functions. This may involve activating switches, sensors, or other inputs to see if the circuit responds correctly.
- Voltage and Current Measurements: Use a multimeter or oscilloscope to measure voltage and current at various points in the circuit. This helps identify abnormalities, such as voltage drops or excessive current draw.
- Resistance Measurements: Measure the resistance of components like resistors, diodes, and coils to check if they are within their specified values. Out-of-spec resistance can indicate component failure.
- Signal Tracing: Trace the flow of signals through the circuit to identify any interruptions or unintended paths. This helps locate open or short circuits.
- Logic Analysis: In digital control circuits, use logic analyzers or oscilloscopes with logic analysis capabilities to capture and analyze digital signals. This is crucial for troubleshooting digital logic errors.
- Time-Domain Analysis: Use oscilloscopes or specialized time-domain analysis tools to analyze signal timing, pulse widths, and duty cycles, which can be critical in control circuits.
- Simulation: Utilize circuit simulation software to model and analyze the behavior of the control circuit. This can help identify potential issues and optimize circuit performance before implementation.
- Frequency Analysis: For circuits involving high-frequency signals or communication protocols (e.g., PWM or serial communication), perform frequency analysis to ensure signal integrity.
- Temperature Measurement: In some cases, control circuits may be affected by temperature variations. Measure the temperature of critical components or areas to check for overheating issues.
- Troubleshooting Tools: Employ various troubleshooting tools like continuity testers, signal injectors, and cable testers to identify and resolve circuit problems.
- Documentation Review: Review the documentation associated with the control circuit, including datasheets for components and equipment manuals, to ensure that components are used within their specified parameters.
- Environmental Analysis: Consider the environmental conditions in which the control circuit operates. Ensure that the circuit is designed to handle temperature, humidity, and other environmental factors.
- Safety Analysis: Assess the control circuit for compliance with safety standards and protocols. Ensure that safety interlocks and emergency shutdowns are functioning as intended.
- Data Logging: Use data loggers to record the performance of the control circuit over time. This can help identify intermittent issues or trends in circuit behavior.
These analysis methods are essential for diagnosing and resolving issues in control circuits, ensuring their reliability, and optimizing their performance for various applications. The specific methods and tools used will depend on the complexity of the circuit and the nature of the control system.
What are the components of a digital communication system?
A digital communication system is a complex system designed to transmit digital data (binary signals) from a sender to a receiver over a communication channel. It involves various components and stages to ensure reliable data transmission. Here are the key components of a digital communication system:
- Information Source: The information source is the origin of the data or message that needs to be transmitted. It could be a person, a computer, a sensor, or any device that generates digital data.
- Encoder: The encoder is responsible for converting the raw data from the information source into a suitable digital format for transmission. It often involves techniques like data compression and error correction coding to improve efficiency and reliability.
- Modulator: The modulator takes the digital signal from the encoder and converts it into an analog signal that can be transmitted over the communication channel. Common modulation techniques include Amplitude Shift Keying (ASK), Frequency Shift Keying (FSK), and Phase Shift Keying (PSK).
- Channel: The channel is the physical medium through which the modulated signal is transmitted. It could be a wired medium (e.g., coaxial cable, optical fiber) or a wireless medium (e.g., radio waves, microwave).
- Demodulator: At the receiving end, the demodulator performs the reverse process of the modulator. It converts the analog signal received from the channel back into a digital signal.
- Decoder: The decoder reverses the encoding process performed at the transmitter. It corrects errors and decompresses the data, if necessary, to retrieve the original digital data.
- Destination: The destination is where the decoded digital data is ultimately delivered. It could be a display device, a storage device, a computer, or any equipment that needs the data.
- Noise and Interference: In any communication system, there is the presence of noise and interference that can corrupt the transmitted signal. Various techniques like error correction codes and signal processing are used to mitigate the effects of noise.
- Transmission Medium: The transmission medium refers to the physical path that the signal travels through. It may introduce various impairments such as attenuation, distortion, and signal loss, which need to be considered in system design.
- Transmitter: The transmitter includes components responsible for generating, encoding, and modulating the signal before it is sent over the channel. It typically consists of a signal source, encoder, and modulator.
- Receiver: The receiver includes components responsible for demodulating, decoding, and processing the received signal to recover the original data. It typically consists of a demodulator, decoder, and signal processing circuitry.
- Clock and Synchronization: To ensure proper timing and synchronization between the transmitter and receiver, clock signals and synchronization techniques are often employed.
- Control and Management: Control and management components may be present to monitor and manage the communication system, including error detection, system configuration, and network control.
- Protocols and Standards: Digital communication systems often rely on standardized communication protocols and standards to ensure interoperability between different systems and devices.
- Security Measures: In modern digital communication systems, security measures such as encryption and authentication are essential to protect data from unauthorized access and interception.
These components work together to enable the transmission of digital data reliably and efficiently over various communication channels, supporting a wide range of applications, including telecommunications, data networking, wireless communication, and more.
What kinds of maskless lithography based on charged particles can be divided into?
Maskless lithography based on charged particles is a technique used in semiconductor manufacturing and nanofabrication to pattern surfaces without the need for traditional photomasks. It involves using charged particles, such as electrons or ions, to directly write patterns onto a substrate. There are several types of maskless lithography based on charged particles, including:
- Electron Beam Lithography (e-beam lithography):
- Scanning Electron Beam Lithography (SEBL): This technique uses a focused electron beam that is scanned across the surface of the substrate to write patterns with high resolution. SEBL is widely used in research and semiconductor fabrication for its ability to create extremely fine features.
- Projection Electron Beam Lithography (PEBL): PEBL uses a projection system to create a patterned electron beam, which is then directed onto the substrate. It can be used for high-throughput lithography applications.
- Ion Beam Lithography (IBL):
- Focused Ion Beam Lithography (FIBL): FIBL uses a focused ion beam (typically gallium ions) to directly write patterns on the substrate. It is commonly used for semiconductor device modification, sample preparation for transmission electron microscopy (TEM), and nanofabrication.
- Electron Projection Lithography (EPL):
- Variable-Shaped Beam (VSB) EPL: In VSB EPL, a patterned electron beam is shaped into variable shapes to write patterns on the substrate. This technique is often used in maskless lithography for semiconductor manufacturing.
- Ion Projection Lithography (IPL):
- Maskless Ion Beam Lithography: IPL uses an array of ion sources and an aperture mask to pattern the ions before they are directed onto the substrate. It can be used for high-throughput lithography in semiconductor manufacturing.
- Nanoimprint Lithography (NIL):
- Electron Beam Nanoimprint Lithography (e-NIL): In e-NIL, an electron beam is used to create a pattern on a resist-coated substrate. After exposure, the resist is used as a mold for subsequent replication steps.
- Electron-Beam-Induced Deposition (EBID):
- Direct Write EBID: In this technique, a focused electron beam is used to induce chemical reactions on the substrate, depositing material selectively. It is often used for adding or repairing features in nanoscale devices.
- Electron Beam Direct Write (EBDW):
- Maskless EBDW: EBDW systems use electron beams to directly write patterns on the substrate, similar to e-beam lithography but without the need for masks. It is commonly used in research and prototyping applications.
- Gas Field Ion Beam (GFIB) Lithography:
- Helium and Neon GFIB Lithography: GFIB systems use helium or neon ions to pattern the substrate. Helium GFIB is particularly useful for high-resolution lithography due to its smaller interaction volume.
These maskless lithography techniques based on charged particles offer advantages such as high resolution, flexibility, and the ability to create custom patterns without the need for physical masks. They are crucial for advanced semiconductor manufacturing, nanofabrication, and research in fields like nanotechnology and materials science.
What tools do you need to prepare for the entire process of making an antenna?
Creating an antenna involves several steps, from design and simulation to fabrication and testing. The tools you need can vary depending on the complexity of the antenna design and the resources available to you. Here’s a general overview of the tools you might need for the entire process of making an antenna:
1. Antenna Design and Simulation:
- Antenna Design Software: Software tools like CST Studio Suite, HFSS (High-Frequency Structure Simulator), FEKO, or similar electromagnetic simulation software for designing and analyzing antenna structures.
- Computer-Aided Design (CAD) Software: CAD software like AutoCAD or SolidWorks for creating mechanical drawings if your antenna design includes structural components.
2. Materials and Components Selection:
- Material Selection Tools: Knowledge of electromagnetic properties of materials, as well as access to databases and material selection guides.
- Antenna Components: Purchase or access to components like coaxial cables, connectors, baluns, and mounting hardware, depending on your antenna design.
3. Fabrication and Assembly:
- Soldering Equipment: Soldering iron, soldering station, solder, and flux for connecting components.
- Mechanical Tools: Depending on your antenna design, you may need tools for cutting, drilling, bending, and shaping materials.
- Measurement Tools: Calipers, rulers, and other measurement tools to ensure precise construction.
- Workbench: A well-organized workspace with adequate lighting and ventilation.
4. Testing and Measurement:
- Network Analyzer: An RF network analyzer for measuring antenna impedance, VSWR (Voltage Standing Wave Ratio), and return loss.
- Spectrum Analyzer: For measuring the radiation pattern and gain of the antenna.
- Signal Generator: To provide the input signal for testing.
- Oscilloscope: For visualizing and measuring waveforms.
- Antenna Measurement Chamber: An anechoic chamber or a controlled environment for accurate antenna testing.
- Antenna Measurement Equipment: Rotating mounts, positioners, and other equipment for positioning and orienting the antenna during testing.
5. Troubleshooting and Optimization:
- Smith Chart: A graphical tool for impedance matching and tuning.
- Antenna Analyzer: Portable devices for quick on-site antenna measurements and adjustments.
- Simulation Software: Continue to use electromagnetic simulation software for optimizing your antenna design based on real-world testing results.
6. Documentation and Analysis:
- Documentation Tools: A lab notebook or electronic documentation system to record design parameters, measurements, and observations.
- Data Analysis Software: Software like MATLAB, Python, or specialized antenna analysis software for processing and analyzing measurement data.
7. Safety Equipment:
- Safety gear such as safety glasses, gloves, and appropriate clothing for working with materials and equipment.
8. Knowledge and Expertise:
- Knowledge of antenna theory, electromagnetic principles, and RF engineering.
- Familiarity with antenna design and simulation software.
- Troubleshooting skills for identifying and addressing issues during the design and testing phases.
It’s important to note that the specific tools and equipment you need may vary depending on the type of antenna (e.g., wire antenna, patch antenna, horn antenna, phased array, etc.) and the frequency range you’re working with. Additionally, access to a well-equipped RF laboratory or fabrication facility may simplify the process and provide access to specialized equipment.
What are the circuit design of the data acquisition module?
The circuit design of a data acquisition module (DAQ) can vary widely depending on the specific application and requirements. However, here is a general overview of the key components and considerations typically found in a DAQ module’s circuit design:
- Signal Conditioning Circuitry:
- Input Protection: Protect the DAQ inputs from overvoltage, static discharge, and noise. This may involve using diodes, transient voltage suppressors (TVS), or optoisolators.
- Amplification and Attenuation: Depending on the input signal level, you may need amplifiers to boost weak signals or attenuators to reduce strong signals to a measurable range.
- Analog-to-Digital Converter (ADC):
- High-Resolution ADC: Select an ADC with the appropriate resolution (number of bits) to suit your application’s measurement accuracy requirements.
- Sample Rate: Choose an ADC with a sample rate that can accurately capture the signal dynamics of your application.
- Voltage Reference: Provide a stable and accurate voltage reference for the ADC to ensure precise analog-to-digital conversion.
- Digital Signal Processing (DSP):
- If required, include digital signal processing components for filtering, noise reduction, and digital calibration.
- Microcontroller or FPGA:
- Integrate a microcontroller or FPGA to control the DAQ module, process digital data, and communicate with a host system (e.g., PC).
- Implement communication interfaces (e.g., USB, Ethernet, SPI, I2C) for data transfer and configuration.
- Clock Generation and Synchronization:
- Generate stable clock signals for the ADC and other components requiring synchronized timing.
- Implement clock synchronization methods to ensure accurate sampling.
- Power Supply:
- Design a stable and clean power supply circuit to provide power to all components.
- Implement voltage regulation, filtering, and isolation as needed to minimize noise and interference.
- Input and Output Connectors:
- Include appropriate connectors for input signals, sensor connections, and output data.
- Consider compatibility with standard sensor interfaces (e.g., BNC, SMA) if applicable.
- Isolation and Grounding:
- Implement isolation techniques to prevent ground loops and improve noise immunity.
- Use isolation amplifiers or digital isolators as necessary.
- Calibration and Self-Test:
- Include circuitry for self-calibration and self-testing to ensure accurate measurements and diagnose hardware issues.
- Memory:
- If needed, incorporate memory for data buffering, storing calibration constants, or storing configuration settings.
- Protection Circuitry:
- Implement protection circuitry to safeguard the DAQ module against faults and overvoltage conditions.
- Fuse protection and overvoltage protection devices can be used.
- Indicator LEDs or Display:
- Include status indicators or a display to provide visual feedback on the module’s operation and status.
- Environmental Considerations:
- Depending on the application, consider environmental factors such as temperature, humidity, and vibration, and design the circuit to meet these requirements.
- Compliance and Safety:
- Ensure that the DAQ module complies with relevant industry standards and safety regulations.
- Software Interface:
- Develop or integrate software drivers and a user interface to configure the DAQ module, acquire data, and perform data analysis.
- Documentation and Labeling:
- Document the circuit design thoroughly, including schematics, component values, and specifications.
- Provide clear labeling for connectors, controls, and indicators.
- Testing and Validation:
- Rigorously test and validate the DAQ module to ensure it meets the specified performance and accuracy requirements.
- Scalability:
- Design the DAQ module with scalability in mind, allowing for expansion or the addition of multiple input channels if needed.
The specific components and circuitry in a DAQ module will depend on the application’s requirements, such as the type of signals being acquired (analog or digital), the measurement accuracy needed, the desired sample rate, and environmental factors. Tailor the design accordingly to meet the unique needs of your data acquisition system.
What constitutes a non-resonant piezoelectric deflagration sensor?
A non-resonant piezoelectric deflagration sensor is a specialized type of sensor designed to detect and measure the pressure or shockwave generated by a deflagration, which is a subsonic combustion wave characterized by a subsonic flame front. These sensors are typically used in applications where rapid detection of deflagrations, such as explosions or combustion events, is critical for safety and monitoring purposes. Here are the key components and characteristics that constitute a non-resonant piezoelectric deflagration sensor:
- Piezoelectric Element: The core component of the sensor is a piezoelectric crystal or ceramic material. Piezoelectric materials generate an electrical charge when subjected to mechanical stress or pressure changes. In the case of a deflagration sensor, the piezoelectric element is designed to respond to the pressure waves generated by a deflagration event.
- Housing or Casing: The piezoelectric element is typically housed in a protective casing or housing that is designed to withstand the environmental conditions and potential shockwaves associated with deflagration events. The housing may be made of materials such as stainless steel or other durable materials.
- Mounting Arrangement: The sensor is often equipped with a mounting arrangement that allows it to be securely attached to the structure or equipment being monitored for deflagrations. Proper mounting ensures that the sensor can effectively detect and transmit pressure changes.
- Electrical Connections: The sensor has electrical connections for transmitting the generated electrical charge to external monitoring and data acquisition equipment. This may include wires or connectors that allow for the sensor’s signal to be processed and analyzed.
- Signal Processing Circuitry: In some cases, signal processing circuitry may be integrated with the sensor to condition and amplify the generated electrical signal. This helps improve the sensitivity and reliability of the sensor.
- Non-Resonant Design: Unlike resonant sensors, which operate at a specific resonant frequency, non-resonant piezoelectric deflagration sensors are designed to operate over a broad frequency range. This design allows them to detect a wide range of pressure wave frequencies associated with deflagration events.
- Sensitivity and Threshold Adjustments: Depending on the application, the sensor may allow for sensitivity and threshold adjustments to customize its response to different deflagration scenarios. This helps minimize false alarms and optimize detection accuracy.
- Safety Features: Deflagration sensors are often designed with safety features, such as overpressure protection, to prevent damage to the sensor in the event of a particularly intense deflagration.
- Compatibility with Monitoring Systems: The sensor should be compatible with data acquisition and monitoring systems that can receive and analyze the sensor’s output. This may involve analog or digital signal interfaces.
- Calibration and Maintenance: Periodic calibration and maintenance may be necessary to ensure the sensor’s continued accuracy and reliability.
Non-resonant piezoelectric deflagration sensors are commonly used in industrial settings, such as refineries, chemical plants, and manufacturing facilities, to detect and respond to potential combustion or explosion hazards. Their ability to rapidly detect pressure changes makes them valuable tools for safety and process monitoring.
What is the use of the inverter?
An inverter is an electronic device or circuit that converts direct current (DC) power into alternating current (AC) power. Inverters serve various purposes in different applications, and their primary use is to enable the efficient conversion and management of electrical power. Here are some common uses of inverters:
- Power Conversion in Renewable Energy Systems:
- Solar Inverters: Convert DC electricity generated by solar panels into AC power for use in homes or to feed back into the grid.
- Wind Inverters: Convert the variable DC output from wind turbines into stable AC power suitable for household or grid use.
- Uninterruptible Power Supplies (UPS):
- Inverters are a key component of UPS systems, providing backup AC power in the event of a mains power failure. They ensure continuous power to critical devices, such as computers, servers, and medical equipment, preventing data loss and downtime.
- Off-Grid and Backup Power Systems:
- Inverters are used in off-grid and backup power systems, such as standalone solar or wind power setups, to convert stored DC energy from batteries into AC power for appliances and devices.
- Motor Control:
- Variable Frequency Drives (VFDs) use inverters to control the speed and torque of AC motors by varying the frequency and voltage of the AC power supplied to the motor. This is common in industrial applications and HVAC systems.
- Consumer Electronics:
- Inverters are used in various consumer electronics, including laptops and smartphones, to convert DC power from batteries into AC power for charging and operation.
- RVs and Boats:
- Inverters are employed in recreational vehicles (RVs) and boats to convert battery power into AC electricity for appliances and devices while off-grid or on the move.
- Transportation:
- Electric vehicles (EVs) and hybrid vehicles use inverters to convert DC power from their batteries into AC power to drive electric motors and provide regenerative braking.
- Grid Stability and Power Quality:
- Inverters are utilized in grid-tied renewable energy systems (e.g., solar farms) to feed excess power back into the grid, improving grid stability and supporting power quality.
- Induction Heating:
- Inverters are employed in induction heating applications for processes such as metal melting, welding, and cooking.
- Emergency Lighting and Backup Systems:
- Inverters power emergency lighting systems and backup generators, ensuring that essential lighting and equipment remain operational during power outages.
- Telecommunications:
- Inverters provide AC power backup for telecommunication equipment, such as cell towers and data centers, to maintain uninterrupted communication services.
- Medical Equipment:
- Medical devices often use inverters to ensure a stable supply of AC power, critical for the proper functioning of diagnostic and treatment equipment.
Inverters come in various types and sizes, including sine wave inverters (which produce a smooth AC waveform similar to the grid), modified sine wave inverters (which produce a stepped approximation of AC), and square wave inverters (which produce a square waveform). The choice of inverter depends on the specific application and the quality of AC power required.
What are the main features of the LTC4008?
The LTC4008 is a high-performance, standalone battery charger controller IC designed by Linear Technology (now a part of Analog Devices). It offers a range of features and capabilities suitable for charging various types of rechargeable batteries, including lithium-ion (Li-ion), lithium-polymer (LiPo), and other battery chemistries. Below are some of the main features of the LTC4008:
- Battery Chemistry Flexibility: The LTC4008 supports a wide range of battery chemistries, making it versatile for charging different types of batteries with varying voltage and current requirements.
- Input Voltage Range: It can operate with input voltages as low as 4V, making it suitable for a variety of input sources, including USB ports, wall adapters, and solar panels.
- High Efficiency: The LTC4008 is designed for high efficiency, helping to maximize the energy transferred to the battery during charging while minimizing power dissipation and heat generation.
- Programmable Charge Current: Users can configure the charge current according to the requirements of the battery and the application. This feature allows for flexibility in charging different battery capacities.
- Constant Voltage/Constant Current (CV/CC) Charging: The device implements a two-stage charging process with constant voltage and constant current stages, ensuring efficient and safe charging for different battery chemistries.
- Battery Temperature Monitoring: It features battery temperature monitoring, which helps prevent overcharging or charging in extreme temperature conditions that may be harmful to the battery.
- Battery Detection and Fault Indication: The LTC4008 can detect various battery states, such as battery presence, charge termination, and fault conditions. It provides indication outputs for these states.
- Timer-Based Charging: The device supports timer-based charging, allowing users to set a maximum charging duration to prevent overcharging in case the battery is not fully charged.
- Input Current Limiting: To protect the input power source, the LTC4008 can limit the input current, which is especially useful when charging from a USB port or other sources with limited current capabilities.
- Input Voltage Regulation: It provides input voltage regulation, ensuring stable charging performance even when the input voltage varies or is noisy.
- Safety Features: The IC includes various safety features, such as overvoltage protection, overcurrent protection, and thermal shutdown, to protect the charger and the battery from potential damage.
- Status Indication: The LTC4008 can provide status information through indicator pins, allowing for easy monitoring of the charging process.
- Low Quiescent Current: In standby or shutdown modes, the LTC4008 consumes very low quiescent current, which is beneficial for battery-powered devices.
- I2C Interface (Optional): Some variants of the LTC4008 offer an I2C interface, allowing for digital communication and control of charging parameters, as well as real-time monitoring and reporting of charging status.
- Small Package: The LTC4008 is available in compact packages, making it suitable for portable and space-constrained applications.
Please note that specific features and capabilities may vary depending on the exact variant or version of the LTC4008. Therefore, it’s essential to refer to the datasheet and documentation provided by Analog Devices for the particular device you are using to ensure accurate information and proper usage.
COMMENTS