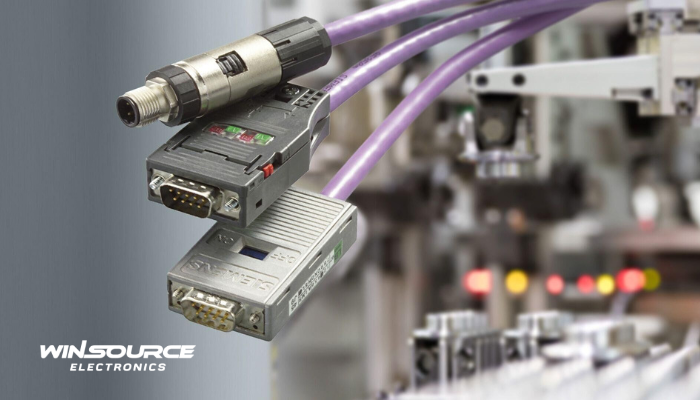
* Question
The design of the PROFIBUS protocol meets the two basic requirements of media control?
* Answer
PROFIBUS (Process Field Bus) is a widely used fieldbus network standard for industrial control systems. It was designed to efficiently manage communication between automation devices. The design of PROFIBUS meets two fundamental requirements of media control, crucial for any industrial communication system:
1. Deterministic Data Exchange
PROFIBUS provides deterministic data exchange, which is essential for real-time industrial automation processes. Deterministic communication means that the messages are guaranteed to be delivered within a specified time frame. This is critical in process control and manufacturing environments where timing and synchronization of data are necessary for coordinating complex machine actions.
– Token Passing for Media Access Control: PROFIBUS uses a token-passing method in the case of PROFIBUS DP (Decentralized Peripherals) and a hybrid of master-slave/token-passing techniques in PROFIBUS PA (Process Automation). This method ensures that only one device (the one holding the token) can transmit at any one time, thereby preventing data collision and ensuring that data is sent in a predictable and orderly fashion.
2. Robustness and Reliability
Robustness and reliability are critical for industrial environments, which often have harsh conditions that can affect communication.
– Redundancy: PROFIBUS supports redundant configurations to enhance system reliability. For example, in critical applications, redundant cabling and duplicated controllers can be used to ensure that the failure of a single component does not bring down the entire network.
– Error Detection and Diagnostic Capabilities: PROFIBUS includes comprehensive error detection and diagnostic mechanisms. It uses checksums for error detection in data transmissions to ensure data integrity. Moreover, the protocol supports extensive diagnostic messages that help in identifying and isolating faults, thus facilitating quick recovery and maintenance.
These two foundational principles of media control in PROFIBUS are complemented by its flexible topology and support for a variety of data rates (up to 12 Mbps), making it suitable for a wide range of industrial applications, from simple sensor communication to complex networked automation systems. This makes PROFIBUS a reliable choice for industrial settings where coordination, timing, and system uptime are crucial.
COMMENTS