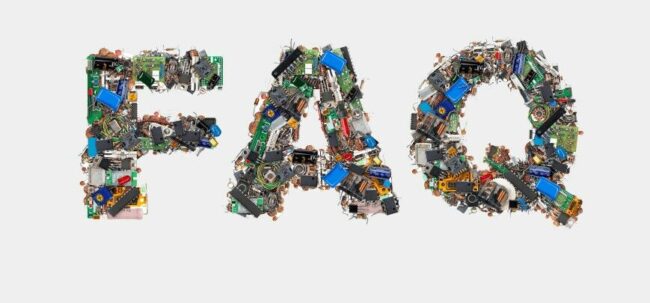
What are the characteristics of the three stepper motors?
Stepper motors are widely used in various applications where precise control of position and speed is required. There are three primary types of stepper motors, each with distinct characteristics:
- Permanent Magnet (PM) Stepper Motors:
- Construction: PM stepper motors have a permanent magnet rotor and a wound stator. The stator windings are energized in a sequence to generate magnetic poles and move the rotor step by step.
- Step Angle: They typically have step angles ranging from 1.8 degrees (200 steps per revolution) to 0.9 degrees (400 steps per revolution).
- Control: PM stepper motors are relatively easy to control and are commonly used in open-loop control systems. The rotor moves to a specific position with each pulse applied to the stator windings.
- Torque: PM stepper motors provide moderate to high holding torque, making them suitable for applications that require holding a load in place when not in motion.
- Efficiency: They are relatively efficient at low speeds but may lose torque and efficiency at high speeds.
- Applications: PM stepper motors are used in printers, CNC machines, 3D printers, robotics, and various motion control applications where precise positioning is essential.
- Variable Reluctance (VR) Stepper Motors:
- Construction: VR stepper motors have a rotor with soft iron or magnetic material, and a stator with salient poles. As the stator windings are energized sequentially, the rotor aligns itself with the stator poles.
- Step Angle: VR stepper motors typically have step angles ranging from 3.6 degrees (100 steps per revolution) to 15 degrees (24 steps per revolution).
- Control: VR stepper motors require more complex control compared to PM motors due to their variable reluctance design. They are often used in open-loop and closed-loop control systems.
- Torque: VR stepper motors generally provide lower holding torque compared to PM and hybrid stepper motors.
- Efficiency: They can be less efficient than PM and hybrid stepper motors, especially at high speeds.
- Applications: VR stepper motors are used in applications such as automotive systems (like idle control valves), where precision and cost-effectiveness are crucial.
- Hybrid Stepper Motors:
- Construction: Hybrid stepper motors combine features of both PM and VR stepper motors. They have a permanent magnet rotor and a stator with teeth, combining the advantages of both designs.
- Step Angle: Hybrid stepper motors have step angles ranging from 0.9 degrees (400 steps per revolution) to 0.36 degrees (1,000 steps per revolution), providing high precision.
- Control: Hybrid stepper motors are versatile and can be used in both open-loop and closed-loop control systems. They are known for their accuracy and ability to provide feedback for position verification.
- Torque: They offer a good balance between holding torque and step resolution, making them suitable for a wide range of applications.
- Efficiency: Hybrid stepper motors are efficient across a broad range of speeds, making them versatile for various applications.
- Applications: Hybrid stepper motors find applications in 3D printers, CNC machines, medical equipment, robotics, and other high-precision motion control systems where accuracy and reliability are essential.
In summary, each type of stepper motor has its own set of characteristics, making it suitable for specific applications. The choice of stepper motor depends on factors such as precision requirements, cost, torque, and the intended application’s control system.
What is diffusion?
Diffusion is a fundamental physical and chemical process that describes the movement of particles (atoms, molecules, ions) from an area of higher concentration to an area of lower concentration. This movement occurs spontaneously and continues until there is an equal distribution of particles throughout the available space, resulting in a state of dynamic equilibrium.
Key characteristics of diffusion include:
- Random Motion: Diffusion relies on the random motion of particles. Even though individual particles move randomly, the net effect of this movement leads to a gradual spreading out of particles from regions of high concentration to regions of low concentration.
- Concentration Gradient: The driving force behind diffusion is the existence of a concentration gradient. Particles naturally move from areas with a higher concentration to areas with a lower concentration in an attempt to reach equilibrium.
- No External Energy: Unlike active transport processes that require energy input (such as ATP in biological systems), diffusion is a passive process that occurs spontaneously and does not require an external energy source.
- Time-Dependent: The rate of diffusion depends on several factors, including the size and shape of the particles involved, the temperature, and the nature of the medium through which diffusion occurs. Smaller particles and higher temperatures generally result in faster diffusion rates.
- Fick’s Laws: Fick’s laws of diffusion are mathematical equations that describe the rate and behavior of diffusion. Fick’s first law relates the rate of diffusion to the concentration gradient, while Fick’s second law describes how the concentration profile changes over time.
Diffusion is a ubiquitous process with numerous real-world applications, including:
- Gas Exchange in Biology: In respiration, oxygen and carbon dioxide diffuse across the alveolar membrane in the lungs and the cell membrane in tissues.
- Chemical Reactions: In chemistry, diffusion plays a critical role in the mixing of reactants in a solution, which is crucial for chemical reactions to occur.
- Food Preparation: Diffusion is involved in processes like marinating food, where flavors and spices diffuse into the food over time.
- Semiconductor Fabrication: Diffusion processes are used in the manufacturing of semiconductors to introduce dopant atoms into silicon wafers to alter their electrical properties.
- Environmental Science: Diffusion is a factor in the dispersion of pollutants in air and water, as well as the movement of nutrients in soil.
- Medicine: In pharmacology, diffusion affects the distribution of drugs within the body, influencing their effectiveness.
In summary, diffusion is the spontaneous movement of particles driven by a concentration gradient and is a fundamental process with widespread applications in the natural and physical sciences, as well as in everyday life.
The main steps of Linux kernel porting?
Porting the Linux kernel to a new platform or architecture involves adapting the kernel’s source code to run on hardware that it wasn’t originally designed for. This process can be complex and requires a good understanding of both the Linux kernel and the target platform. Here are the main steps involved in Linux kernel porting:
- Select the Target Platform:
- Identify the specific hardware or architecture you want to port the Linux kernel to. This could be a new CPU architecture, a different system-on-chip (SoC), or a custom hardware platform.
- Set Up the Development Environment:
- Ensure that you have a development environment set up for the target platform. This includes setting up cross-compilation tools, a toolchain, and any necessary debugging tools for the target architecture.
- Get the Kernel Source Code:
- Download the Linux kernel source code that corresponds to the version you want to port. You can get the source code from the official Linux kernel website (kernel.org) or a specific repository maintained by the platform or hardware vendor.
- Analyze the Hardware:
- Study the documentation for the target hardware or architecture to understand its specifications, memory layout, device interfaces, and any other relevant details. You may also need to access any reference manuals or datasheets provided by the hardware manufacturer.
- Create a New Configuration:
- Start by configuring the kernel for the target platform. Use the appropriate configuration tool (e.g.,
menuconfig
,nconfig
, orxconfig
) to set the kernel options, features, and architecture-specific settings.
- Start by configuring the kernel for the target platform. Use the appropriate configuration tool (e.g.,
- Adapt Device Drivers:
- Many hardware-specific components in the kernel are implemented as device drivers. You’ll need to adapt or create new device drivers for the target hardware. This may involve modifying existing drivers or writing entirely new ones.
- Platform Initialization Code:
- Implement the platform-specific initialization code required to bring up the hardware. This includes tasks like initializing memory, setting up the interrupt controller, configuring the bootloader, and initializing hardware peripherals.
- Bootloader Integration:
- Integrate the Linux kernel with the bootloader used on the target platform. Ensure that the bootloader can load and execute the kernel image correctly. You may need to modify the bootloader configuration or scripts as necessary.
- Cross-Compile the Kernel:
- Use the cross-compilation tools and toolchain you set up earlier to build the kernel image for the target platform. Pay attention to architecture-specific compiler flags and options.
- Testing and Debugging:
- Test the kernel on the target hardware. Debug any issues that arise during the boot process or while running Linux on the platform. Utilize debugging tools, such as GDB and printk messages, to diagnose and fix problems.
- Optimization and Fine-Tuning:
- Optimize the kernel for performance and resource usage on the target platform. This may involve configuring kernel options, removing unnecessary features, or fine-tuning device drivers.
- Documentation and Maintenance:
- Document the porting process, including any hardware-specific configurations and driver modifications. Keep track of changes and ensure that the kernel remains up to date with mainline releases to benefit from ongoing kernel development.
- Community Involvement (Optional):
- If you are working on a platform or architecture that may benefit the Linux community, consider upstreaming your changes to the mainline kernel source tree. This involves collaborating with the Linux kernel community to integrate your work into the official kernel source.
Linux kernel porting is a complex and specialized task that requires expertise in both kernel development and the target platform’s hardware. It often involves a significant amount of testing and debugging to ensure the kernel runs smoothly on the new platform. Collaboration with the open-source community can be valuable for long-term maintenance and broader adoption of the ported kernel.
What is a periodic self-test?
A periodic self-test, also known as a self-check or self-diagnostic test, is a routine process or built-in mechanism in a device, system, or software application designed to assess its functionality and identify any potential issues or failures. The purpose of periodic self-tests is to ensure that the system or device continues to operate correctly over time, detecting and addressing problems before they lead to more significant failures or malfunctions.
Here are some key points about periodic self-tests:
- Scheduled Intervals: Periodic self-tests are typically conducted at predetermined intervals, which can vary depending on the specific system or device. These intervals may be based on time (e.g., daily, weekly, monthly), usage (e.g., after a certain number of operating hours or cycles), or other relevant factors.
- Automated Process: These tests are automated and do not require manual intervention. They are programmed into the system’s firmware, software, or hardware, allowing them to run autonomously.
- Functional Checks: Periodic self-tests often involve checking the functionality of various components or subsystems within the device or system. For example, in a computer, self-tests may assess the integrity of the memory, storage devices, and input/output ports.
- Diagnostic Routines: The self-tests may include diagnostic routines that generate test patterns, simulate specific conditions, or run algorithms to verify the correct operation of hardware or software components.
- Error Detection: If a problem or error is detected during a periodic self-test, the system may respond by logging the issue, notifying the user or administrator, attempting to correct the problem, or entering a safe mode to prevent further damage or data loss.
Examples of Periodic Self-Tests:
- Computer Systems: Many computer systems, including servers, workstations, and embedded systems, perform regular self-tests during the boot-up process. These tests can include checking memory (RAM) for errors, verifying the integrity of the file system, and testing hardware components such as the CPU, disk drives, and network interfaces.
- Automotive Systems: Modern vehicles often conduct self-tests of various onboard systems, such as the engine control module (ECM), transmission control module (TCM), and anti-lock braking system (ABS). These tests help identify issues that could affect vehicle performance or safety.
- Medical Devices: Medical equipment, like MRI machines or infusion pumps, may run periodic self-tests to ensure that they are operating within specified parameters. This is critical for patient safety and accurate diagnosis and treatment.
- Consumer Electronics: Devices like smartphones and smart TVs may perform self-diagnostic checks during startup to identify issues with hardware or software components.
Periodic self-tests are an important part of proactive maintenance and troubleshooting, as they help prevent unexpected system failures and improve overall reliability. These tests are especially valuable in critical systems where the consequences of failure can be significant, such as medical devices, aerospace systems, and industrial automation.
What entities are included in the VHDL program?
In VHDL (VHSIC Hardware Description Language), a hardware description language used for designing digital circuits and systems, programs or descriptions are organized into various entities and architectures. These entities and architectures work together to define the behavior and structure of a digital system. Here are the main components of a VHDL program:
- Library Declarations:
- VHDL programs typically begin with library declarations. Libraries contain predefined and user-defined packages that provide reusable functions and components. Common VHDL libraries include the standard IEEE library.
- Entity Declarations:
- An entity is a high-level description of a digital component or system. It defines the interface of the component, including input and output ports. The entity declaration specifies the name of the entity and its ports, along with their types and directions (in, out, or inout).
- Architecture Declarations:
- An architecture declaration defines the internal behavior and structure of an entity. Multiple architectures can be associated with a single entity, allowing different implementations or configurations of the same component. Each architecture declaration specifies the name of the associated entity, the architecture’s name, and the internal logic or behavior of the entity.
- Signal Declarations:
- Signals are used to model internal connections and data flow within architectures. They represent wires or nodes that carry data between different parts of the design. Signal declarations include the signal name, type, and optionally an initial value.
- Component Declarations:
- Components allow you to reuse existing entities within your design. They serve as templates for instantiating entities within an architecture. Component declarations specify the name of the component, its entity, and the generic map (if any) that configures the component.
- Process Statements:
- Processes are used to describe the behavior of digital circuits. They contain a series of sequential or concurrent statements that define how signals and variables change over time. Processes are often used for describing combinational and sequential logic.
- Sequential Statements:
- Sequential statements describe actions that occur one after the other in a specific order. Examples include assignments, conditional statements (if-then-else), and loops (for and while).
- Concurrent Statements:
- Concurrent statements describe actions that can occur concurrently or simultaneously. VHDL supports concurrent signal assignments, conditional signal assignments (when-else), and instantiation of components within architectures.
- Configuration Declarations (Optional):
- Configuration declarations specify how different entities and architectures are connected and instantiated within a design. They are used when you have multiple architectures for the same entity, and you want to specify the particular configuration to use.
- Testbench (Optional):
- A testbench is a separate VHDL program used for simulating and testing the behavior of the design. It typically includes stimulus generation, simulation control, and assertions for verifying the correctness of the design.
In VHDL, the combination of an entity declaration and an associated architecture declaration defines a complete component or module. Multiple modules can be interconnected to create complex digital systems. The language’s hierarchical structure and modularity make it suitable for modeling and simulating digital designs, ranging from simple logic gates to sophisticated processors and systems-on-chip (SoCs).
Why does the knob position deviation cause the range to be inaccurate?
The deviation in the knob position can cause inaccuracies in various mechanical and electrical systems that rely on position or angle control. This phenomenon is often referred to as “knob position error” or “position deviation error,” and it can have several underlying causes, leading to inaccuracies in the system’s range. Here’s why this occurs:
- Mechanical Tolerances:
- Manufacturing processes have tolerances, which means that there can be slight variations in the dimensions and alignments of mechanical components, including knobs, shafts, gears, and linkages. Even small deviations in these components can result in inaccuracies in the knob’s position.
- Backlash:
- Backlash is a mechanical phenomenon where there is a small gap or play between components in a mechanical system. When you turn a knob, there might be a brief movement of the knob before it engages and starts to turn the connected component. This initial play can lead to position errors.
- Wear and Tear:
- Over time, mechanical components can wear down, leading to increased play or imprecise movement. This wear and tear can result in position deviations when the knob is turned.
- Control System Design:
- The design of the control system itself can contribute to position errors. If the control algorithm does not account for mechanical variations or does not provide adequate feedback and correction mechanisms, it may not accurately control the position of the system.
- Sensor Accuracy:
- In systems that use sensors to measure position or angle, the accuracy and precision of the sensors play a crucial role. If the sensor itself has inaccuracies or if it is not calibrated correctly, it can introduce position errors.
- Environmental Factors:
- Environmental conditions such as temperature variations and humidity can affect the dimensions and materials of mechanical components, potentially leading to changes in position accuracy.
- Play in Linkages:
- In systems with multiple mechanical linkages or couplings, there can be play or flexibility in the linkages, which can cause position deviations when the knob is turned.
- Vibration and Shock:
- External factors like vibration and shock can affect the stability of mechanical components and introduce position errors, particularly in sensitive systems.
To mitigate knob position errors and improve the accuracy of systems that rely on knob-controlled positioning, manufacturers and engineers employ various strategies, including:
- Designing and manufacturing components to tighter tolerances.
- Using high-quality materials and coatings to reduce wear and friction.
- Implementing control algorithms that incorporate feedback mechanisms to correct for errors.
- Regular maintenance and calibration of the system to account for wear and environmental effects.
- Using precision sensors and encoders to directly measure and correct for position.
In summary, knob position deviation can cause inaccuracies in a system’s range due to a combination of mechanical factors, control system design, and environmental influences. Addressing these factors through careful design, maintenance, and calibration is essential to minimize position errors and maintain accurate control.
What are the components of the clock system structure of the LPC2000 series ARM?
The LPC2000 series microcontrollers from NXP Semiconductors (formerly Philips Semiconductors) are based on the ARM7TDMI-S core and feature a clock system structure that is essential for controlling the timing and operation of the microcontroller. The key components of the clock system structure in the LPC2000 series ARM microcontrollers include:
- Main Oscillator (Main Crystal Oscillator):
- The main oscillator is an external crystal oscillator or ceramic resonator connected to the microcontroller. It provides the primary clock source for the CPU and other peripherals. The crystal or resonator frequency can typically range from a few MHz to tens of MHz, depending on the specific LPC2000 microcontroller variant.
- Phase-Locked Loop (PLL):
- The PLL is a crucial component that multiplies the frequency of the main oscillator to generate a higher-frequency clock source. This higher-frequency clock is often referred to as the CPU clock (CCLK) and is used to clock the CPU core and other internal peripherals. The PLL allows for the adjustment of the system clock frequency to meet the specific performance requirements of the application.
- Peripheral Clocks:
- The LPC2000 series microcontrollers feature a clock distribution network that provides clock signals to various on-chip peripherals, including UARTs, timers, GPIO ports, and other modules. These peripheral clocks are derived from the CPU clock and are typically configurable, allowing you to control the clock frequencies for specific peripherals.
- Memory Clocks:
- The microcontroller includes separate clocks for the Flash memory and RAM. These clocks are derived from the CPU clock and allow for precise timing control when accessing memory. The memory clocks ensure that read and write operations to memory are synchronized correctly.
- Watchdog Timer (WDT) Clock:
- The WDT clock is a dedicated clock source for the watchdog timer module. The watchdog timer is used for system reset or other recovery mechanisms in case of software or hardware failures.
- Real-Time Clock (RTC) Clock (Optional):
- Some LPC2000 microcontrollers include a real-time clock module with its own clock source. The RTC clock is used for timekeeping and calendar functions and is often driven by a low-frequency external crystal.
- Peripheral Clock Enable/Disable Control:
- The microcontroller typically provides control registers that allow you to enable or disable clocks for specific peripherals. This feature helps conserve power when certain peripherals are not in use.
- Clock Source Selection and Configuration Registers:
- The LPC2000 series microcontrollers include registers that enable you to configure clock sources, PLL parameters, and other clock-related settings. These registers allow you to customize the clock system to meet the requirements of your application.
- Power Management Unit (PMU) (Optional):
- Some LPC2000 microcontrollers feature a power management unit that allows you to control power modes and clock gating to optimize power consumption based on the application’s needs.
The specific details of the clock system structure may vary slightly between different LPC2000 microcontroller variants, but the fundamental components mentioned above are common to most devices in the series. Configuring and managing the clock system is a critical aspect of programming LPC2000 microcontrollers to ensure proper timing and efficient operation of your embedded applications. Be sure to refer to the device datasheet and reference manual for the specific LPC2000 microcontroller you are using to understand its clocking features and registers in detail.
What is the precision chip Resistors?
Precision chip resistors, also known as precision surface-mount resistors or precision SMD (Surface Mount Device) resistors, are a type of electronic component designed to provide highly accurate and stable resistance values in various electronic circuits. These resistors are used when precision and reliability are essential, particularly in applications like analog signal processing, voltage dividers, and instrumentation.
Key features and characteristics of precision chip resistors include:
- Tight Tolerance: Precision chip resistors are manufactured with very tight tolerance values, typically in the range of ±0.1%, ±0.05%, or even ±0.01%. This means that the actual resistance of the resistor closely matches its specified nominal value.
- Low Temperature Coefficient: These resistors have a low temperature coefficient of resistance (TCR), which means that their resistance remains stable over a wide temperature range. Low TCR values ensure that changes in temperature do not significantly affect the resistor’s accuracy.
- High Stability: Precision chip resistors are designed for long-term stability. They exhibit minimal drift in resistance over time, ensuring that their initial accuracy is maintained over the life of the circuit.
- Small Size: These resistors are compact and come in standard surface-mount package sizes, such as 0402, 0603, 0805, and 1206, making them suitable for densely populated circuit boards.
- Low Noise: Precision chip resistors are known for their low noise characteristics, which make them suitable for applications involving sensitive analog signals.
- Wide Range of Resistance Values: They are available in a broad range of resistance values, from ohms to megaohms, allowing them to be used in a variety of applications.
- High Power Handling: Precision chip resistors can typically handle relatively high power levels, with ratings ranging from 0.1 watts to several watts, depending on their size and construction.
- Various Construction Materials: Precision chip resistors may use different materials for their resistive elements, including thin-film, thick-film, and metal foil. The choice of material can impact their performance characteristics.
- Low Inductance and Capacitance: These resistors are designed with low parasitic inductance and capacitance, which is crucial for high-frequency and high-speed applications.
- Laser Trimmed: Some precision chip resistors are laser trimmed to achieve their precise resistance values, ensuring that they meet the specified tolerance.
Precision chip resistors are commonly used in applications where precise voltage or current division, gain control, feedback, or filtering is required. Examples of such applications include analog-to-digital converters (ADCs), digital-to-analog converters (DACs), operational amplifiers (op-amps), precision voltage references, and calibration circuits.
When selecting a precision chip resistor for a specific application, it’s essential to consider factors such as the required resistance value, tolerance, power rating, and environmental conditions to ensure that the resistor meets the desired level of accuracy and stability.
How to input offset voltage?
Input offset voltage (also known as input offset voltage, Vos) is a parameter in electronic circuits, particularly in operational amplifiers (op-amps), that represents a small voltage difference between the inverting and non-inverting inputs when the op-amp is in its ideal or balanced state (i.e., when both inputs are theoretically at the same voltage). This offset voltage can lead to inaccuracies in amplification or signal processing. To compensate for input offset voltage or minimize its effects, you can use several methods:
- Offset Voltage Adjustment (Trimmer Potentiometer):
- Many op-amp ICs, especially those designed for precision applications, have offset pins (often labeled as “Offset Null” or “Offset Adjust”) that allow you to connect an external resistor or trimmer potentiometer. By adjusting the resistance, you can nullify or minimize the offset voltage.
- Differential Input Configuration:
- When using an op-amp in applications like amplification, consider employing a differential input configuration. This involves using both the inverting and non-inverting inputs for your signal. Any offset voltage present on both inputs will have a reduced effect as it is common to both inputs and does not contribute to the differential output.
- Chopper Stabilized Amplifiers:
- Chopper-stabilized op-amp ICs are designed to minimize input offset voltage. They use internal circuitry to periodically nullify the offset voltage, making them ideal for high-precision applications.
- Auto-Zeroing Amplifiers:
- Some op-amp ICs have built-in auto-zeroing circuits that periodically correct the input offset voltage, ensuring that it remains low and stable over time and temperature variations.
- Trimming at the Design Stage:
- During the design phase, you can select op-amp ICs with low input offset voltage specifications to minimize the need for external compensation.
- Software Calibration (Digital Signal Processing):
- In some cases, particularly in digitally controlled systems, you can use digital signal processing techniques to measure and compensate for input offset voltage. This may involve measuring the offset voltage during a calibration phase and then subtracting it from subsequent measurements or calculations.
- Component Matching:
- If your circuit involves multiple op-amps or amplifier stages, you can select or match op-amps with similar input offset voltages to reduce differences in offset between stages.
- Temperature Compensation:
- Consider using temperature-compensated components or techniques if temperature variations significantly affect the offset voltage. Some precision circuits employ thermally stable resistors and components to minimize drift.
- External Compensation Circuitry:
- In some cases, you may design external circuitry, such as a compensation network, to nullify the offset voltage. This might involve using capacitors, resistors, or specialized components.
It’s important to note that the method you choose to address input offset voltage depends on the specific requirements of your circuit and the available components. When selecting or designing for low input offset voltage, consider factors such as cost, complexity, power consumption, and the required level of precision. Additionally, consult the datasheets and application notes provided by the manufacturer of the op-amp or amplifier IC you are using, as they often provide guidance on offset voltage compensation techniques for their specific devices.
What is the working principle of the voltage comparator?
A voltage comparator is an electronic circuit or component that compares two input voltage signals and produces an output that indicates which input is greater in magnitude. The primary function of a voltage comparator is to perform binary comparisons, determining whether one voltage is greater than or less than another. These devices are commonly used in various applications, including analog-to-digital converters, voltage level detection, window comparators, and trigger circuits. The working principle of a voltage comparator can be summarized as follows:
- Inputs:
- A voltage comparator typically has two input terminals, referred to as the inverting (-) input and the non-inverting (+) input.
- Voltage Comparison:
- The comparator continuously compares the voltage at the inverting input to the voltage at the non-inverting input.
- Output States:
- The output of the voltage comparator is a digital signal with two possible states:
- When the voltage at the non-inverting input (+) is higher than the voltage at the inverting input (-), the output is in a “high” state (usually close to the positive supply voltage, Vcc).
- When the voltage at the inverting input (-) is higher than the voltage at the non-inverting input (+), the output is in a “low” state (usually close to the negative supply voltage, GND).
- The output of the voltage comparator is a digital signal with two possible states:
- Threshold Voltage:
- The comparator has an internal threshold voltage (reference voltage) that determines the point at which it switches its output state. This threshold voltage is often set at the midpoint between the supply voltage (Vcc) and ground (GND).
- Hysteresis (Optional):
- Some voltage comparators include hysteresis, which introduces a small amount of positive feedback to prevent rapid oscillations when the input voltages are close to each other. Hysteresis ensures stable and noise-immune switching.
- Response Time:
- Voltage comparators have very fast response times, making them suitable for high-speed applications.
- Power Supply:
- Voltage comparators require a power supply voltage (Vcc) for their operation. The output voltage levels depend on the supply voltage and the internal circuitry of the comparator.
- Output Driver:
- The output of the voltage comparator is typically connected to a driver stage that provides sufficient current to drive external circuitry, such as microcontrollers, logic gates, or other digital devices.
In summary, the working principle of a voltage comparator involves continuously comparing two input voltage signals and producing a digital output that indicates the relationship between these voltages (greater than or less than). The comparator’s threshold voltage determines the switching point, and optional hysteresis helps ensure stable operation. This simple yet versatile device plays a crucial role in many electronic systems, facilitating tasks such as signal conditioning, signal level detection, and decision-making in various applications.
COMMENTS