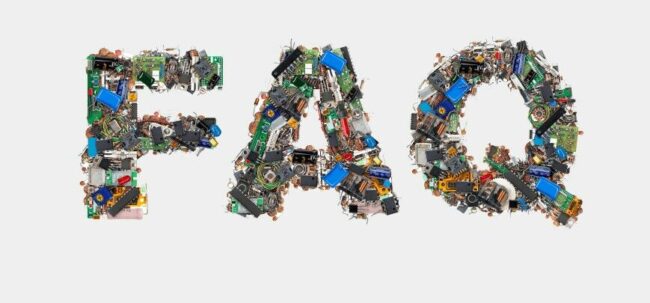
What are the steps to take with a smart card (taking a contact card as an example)?
Using a contact smart card typically involves a series of steps to access or manipulate data on the card. Here are the general steps you would take with a contact smart card:
- Acquire a Smart Card Reader: You’ll need a smart card reader to interface with the smart card. These readers can be built into devices like laptops or desktop computers, or they can be external USB devices. Ensure that the reader is compatible with your smart card and operating system.
- Install Smart Card Software: If your smart card reader requires drivers or specific software, make sure you have them installed on your computer. These drivers and software may be provided by the smart card manufacturer or the reader manufacturer.
- Insert the Smart Card: Carefully insert the smart card into the card reader slot. Be sure to insert it in the correct orientation; most smart cards have a specific way they should be inserted.
- Establish a Connection: Once the card is inserted, the reader should establish a connection with the card automatically. If not, you might need to open the appropriate software or application to initiate the connection.
- Authenticate: Depending on the purpose of your smart card (e.g., access control, identification, or payment), you will need to provide the necessary authentication. This typically involves entering a Personal Identification Number (PIN) associated with the card. The card will verify the PIN to ensure that the person using the card is authorized.
- Perform Actions: After authentication, you can perform various actions with the smart card, depending on its functionality. These actions might include:
- Accessing Data: You can read data from the card, such as personal information, certificates, or cryptographic keys.
- Digital Signatures: If the card is used for authentication or digital signatures, you can sign documents or transactions securely.
- Data Storage: Some smart cards allow you to store data securely.
- Payment Transactions: If it’s a payment card, you can make transactions by presenting the card to a payment terminal.
- Eject the Card: When you are done using the card, safely eject it from the smart card reader. This ensures that the card is not accidentally accessed by unauthorized individuals.
- Secure the Card: Smart cards contain sensitive information, so it’s crucial to keep them secure. Store your smart card in a safe place, and if it’s a contactless card, be aware of the risk of unauthorized scanning or data theft.
- Log Out or Disconnect: If you were using software or applications to access the card, make sure to log out or disconnect from the card to prevent unauthorized access.
- PIN Management: If necessary, manage your PIN by changing it periodically or in case you suspect it has been compromised.
It’s important to note that the exact steps and procedures may vary depending on the type of smart card, the card reader, and the specific applications or systems you are using the card with. Always follow the instructions provided by the card manufacturer and any relevant security guidelines to ensure the proper and secure use of your smart card.
What PWM channels does the ePWM module have?
The number of PWM (Pulse Width Modulation) channels in an ePWM (enhanced Pulse Width Modulation) module can vary depending on the specific microcontroller or microprocessor being used. The number of PWM channels is a hardware feature determined by the chip’s design, and it can differ between different manufacturers and even between different models within the same manufacturer’s product line.
To find out the number of PWM channels available in the ePWM module of a specific microcontroller or microprocessor, you should refer to the device’s datasheet, reference manual, or technical documentation provided by the manufacturer. These documents typically provide detailed information about the device’s features and capabilities, including the number and configuration of PWM channels in the ePWM module.
For example, common microcontroller families like the Texas Instruments Tiva C Series, STM32, and PIC32 may have different ePWM modules with varying numbers of PWM channels. Therefore, it’s essential to consult the documentation specific to the device you are using to determine the number of available PWM channels and how to configure and use them.
How can the Count Comparison (CC) module operate two comparison events?
The Count Comparison (CC) module is often used in microcontroller or microprocessor peripherals to generate events or trigger actions based on comparisons between a counter value and one or more predefined reference values. To operate two comparison events using the CC module, you typically need a CC module that supports multiple comparison registers and corresponding control logic. Here’s how you can set up a CC module to operate two comparison events:
- Check the Capabilities of the CC Module: First, ensure that the CC module in your microcontroller or microprocessor supports multiple comparison events. Not all CC modules are capable of this; it depends on the specific hardware design.
- Initialize the CC Module: Initialize the CC module by configuring its settings, such as the counter source, clock source, and other parameters, as needed for your application.
- Configure Multiple Comparison Registers: Most CC modules that support multiple comparison events have multiple comparison registers. Each comparison register stores a reference value against which the counter value will be compared. Configure at least two comparison registers for your two comparison events.
- Set Comparison Values: Set the comparison values in the configured comparison registers. These values will determine when the comparison events occur. You’ll typically write the values directly to the registers in your code.
- Configure Action on Comparison: For each comparison event, configure what action should be taken when the counter matches the comparison value. Common actions include generating interrupts, triggering external events, setting or clearing flags, or performing other tasks.
- Enable the CC Module: Enable the CC module to start comparing the counter value with the configured comparison values. This may involve setting control bits or flags to start the comparison operation.
- Monitor Comparison Events: Depending on your application, you may need to monitor the status of the CC module to detect when a comparison event occurs. This could involve checking status flags or handling interrupt requests generated by the CC module.
- Handle Comparison Events: When a comparison event occurs (i.e., when the counter matches one of the comparison values), execute the corresponding actions you configured in step 5. This might involve executing specific code or triggering other peripherals or modules.
- Repeat as Needed: If you need to operate more than two comparison events, configure additional comparison registers and actions as required, following the same principles outlined above.
The specific configuration and usage of the CC module can vary depending on the microcontroller or microprocessor architecture and the software development environment you are using. Always refer to the documentation and reference manual provided by the manufacturer for detailed information on configuring and using the CC module in your specific hardware platform.
What are the security system components of the smart card?
Smart cards are designed with various security features and components to ensure the protection of data and secure access. The security system components of a smart card typically include:
- Microcontroller/Processor: This is the heart of the smart card, responsible for executing commands, managing data, and implementing security protocols. The microcontroller often includes cryptographic hardware for secure operations.
- Secure Data Storage: Smart cards contain non-volatile memory to store sensitive data securely. This may include user data, cryptographic keys, certificates, and application-specific information.
- Cryptographic Hardware: Many smart cards have dedicated cryptographic co-processors to perform encryption, decryption, and hashing operations efficiently. These hardware-based cryptographic components enhance the security of the card.
- Operating System (OS): Smart cards run an embedded operating system that manages card functions, security features, and application execution. The OS plays a crucial role in protecting data and controlling access.
- Security Peripherals: Smart cards often include security peripherals like true random number generators (TRNGs) to generate cryptographic keys, and hardware-based tamper detection mechanisms to safeguard against physical attacks.
- Authentication Mechanisms: Smart cards use various authentication methods, such as Personal Identification Numbers (PINs), biometric data (fingerprint, iris, etc.), or even multi-factor authentication (PIN plus biometrics) to ensure that only authorized users can access the card’s contents.
- Cryptographic Keys: Smart cards store cryptographic keys securely and perform cryptographic operations within the card’s secure environment. These keys are used for secure authentication, data encryption, digital signatures, and more.
- Access Control: The smart card’s OS enforces access control policies, ensuring that only authorized applications can access specific data or functionality on the card. Access to sensitive data is typically restricted to prevent unauthorized access.
- Secure Communication Protocols: Smart cards use secure communication protocols (e.g., ISO 7816) to ensure that data exchanged between the card and external devices, such as card readers, is protected from eavesdropping and tampering.
- Physical Security Measures: Smart cards are designed to resist physical attacks, including tamper-evident packaging and coating, anti-cloning features, and anti-tearing mechanisms. Some cards also self-destruct if tampering is detected.
- Lifecycle Management: Smart cards often have built-in features for managing their lifecycle, including personalization, issuance, revocation, and retirement.
- Secure Application Environment: Smart cards support secure execution environments for applications, isolating them from one another to prevent one application from compromising the security of others on the same card.
- Audit and Logging: Some smart cards maintain audit logs of security-related events, allowing administrators to review card activity and detect potential security breaches.
- Secure Channel Establishment: Smart cards can establish secure channels with external systems, ensuring that data exchanged during card operations is protected from interception or manipulation.
- Physical Tamper Resistance: Smart cards are often designed to be tamper-resistant. They can include protective measures like epoxy coatings, meshed metal layers, and other physical barriers to deter physical attacks.
It’s important to note that the specific security components and features of a smart card can vary depending on the card’s intended use case and security requirements. Different industries, such as finance, healthcare, government, and access control, may have specific standards and security guidelines for smart card implementations to ensure data protection and user security.
What are the characteristics of metal strain gauge sensors?
Metal strain gauge sensors, also known as strain gauges or resistance strain sensors, are widely used in engineering and industrial applications to measure strain or deformation in materials. These sensors operate on the principle that the electrical resistance of a metallic wire or foil changes in response to mechanical strain. Here are some key characteristics of metal strain gauge sensors:
- Sensitivity to Strain: Metal strain gauges are highly sensitive to minute changes in strain or deformation in the material to which they are attached. This sensitivity makes them suitable for measuring very small displacements or deformations.
- Linear Response: Within their specified range, metal strain gauges exhibit a linear relationship between the mechanical strain applied to the material and the change in electrical resistance. This linearity simplifies calibration and data interpretation.
- Wide Range of Applications: Metal strain gauges are versatile and can be used to measure strain in various materials, including metals, composites, plastics, and more. They are commonly employed in structural health monitoring, load cells, and stress analysis.
- Temperature Sensitivity: The electrical resistance of metal strain gauges is temperature-sensitive, which can be both an advantage and a challenge. Special compensation techniques or temperature-compensated strain gauges are used to minimize temperature-related errors.
- Temperature Compensation: To mitigate temperature effects on the accuracy of measurements, some strain gauges are equipped with a second set of resistors (thermistors) for temperature compensation. This helps maintain measurement accuracy over a wide temperature range.
- Wheatstone Bridge Configuration: Strain gauges are typically arranged in a Wheatstone bridge configuration to measure the small changes in resistance accurately. This bridge setup improves the sensitivity and precision of measurements.
- Accuracy: Metal strain gauges can provide highly accurate measurements when calibrated properly. The accuracy depends on factors such as the gauge’s quality, temperature compensation, and calibration techniques.
- Strain Gauge Factors: Different materials used in strain gauges have different strain gauge factors (also known as gauge factors or sensitivity factors). These factors determine the magnitude of resistance change for a given strain and are specific to the strain gauge material.
- Wiring and Signal Conditioning: To obtain meaningful measurements, the output signal from the strain gauge bridge needs to be conditioned and amplified. Signal conditioning techniques include amplification, filtering, and noise reduction.
- Mounting and Adhesion: Proper mounting and adhesion of strain gauges to the material under investigation are critical to accurate measurements. Incorrect mounting can introduce measurement errors.
- Fatigue Resistance: Some strain gauges are designed for applications involving cyclic loading and high-frequency vibrations. These gauges have improved fatigue resistance and durability.
- Environmental Protection: In harsh or corrosive environments, strain gauges may require additional protective coatings or housings to ensure long-term reliability.
- Strain Range: Metal strain gauges are available in various models with different strain measurement ranges. The choice of strain gauge depends on the expected strain levels in the application.
- Cost: The cost of metal strain gauges varies depending on factors like sensitivity, accuracy, and environmental robustness. High-precision gauges designed for demanding applications tend to be more expensive.
- Integration: Strain gauges can be integrated into custom-designed structures or affixed to existing structures using adhesives or welding, making them suitable for a wide range of applications.
- Calibration: Proper calibration is crucial for accurate measurements. Calibration involves applying known strains to the gauge and recording the corresponding electrical resistance changes.
Overall, metal strain gauge sensors are essential tools for measuring mechanical strain in a wide variety of materials and structures, playing a vital role in fields such as civil engineering, aerospace, automotive, and material testing.
What are the characteristics of a two-dimensional barcode?
Two-dimensional (2D) barcodes are a type of matrix or symbology barcode that can store and represent data in two dimensions, as opposed to the traditional one-dimensional (1D) barcodes that store data in a horizontal sequence of lines. Here are the key characteristics of a two-dimensional barcode:
- Data Capacity: One of the most significant advantages of 2D barcodes is their high data capacity. They can store a substantial amount of information, including alphanumeric characters, binary data, and special characters. The exact data capacity varies depending on the specific type of 2D barcode.
- Compact Size: Despite their high data capacity, 2D barcodes are compact and can be printed or displayed on a relatively small surface area. This compact size makes them suitable for applications where space is limited.
- Structured Data: 2D barcodes store data in a structured grid or matrix format. Data is organized into rows and columns, allowing for more complex data structures compared to 1D barcodes.
- Error Correction: Many 2D barcode formats incorporate error correction techniques, which means they can still be read accurately even if the code is partially obscured or damaged. This error correction ensures robust data retrieval.
- Versatile Data Types: 2D barcodes can encode a wide range of data types, including text, numbers, URLs, contact information (vCards), Wi-Fi network credentials (QR codes), and more. This versatility makes them suitable for various applications, from product labeling to mobile device interactions.
- High-Speed Scanning: Modern 2D barcode scanners and smartphone apps can quickly and accurately read 2D barcodes, making them suitable for applications where speed and efficiency are essential.
- Application-Specific: Different types of 2D barcodes are designed for specific applications or industries. For example, QR codes are commonly used in marketing and mobile applications, while Data Matrix codes are often used in manufacturing and logistics.
- Customizable: Many 2D barcode formats allow for customization of colors, sizes, and additional graphical elements. This can be helpful for branding and visual recognition.
- Security: Some 2D barcode formats support encryption and digital signatures, enhancing data security when transmitting sensitive information.
- Readable from Various Angles: 2D barcodes can be scanned from different angles, making them more flexible in terms of scanning orientation compared to 1D barcodes.
- Encoding Methods: There are various encoding methods used in 2D barcodes, including binary, alphanumeric, and Kanji character encoding. The choice of encoding method depends on the data to be stored.
- Widely Supported: Many 2D barcode formats are widely supported by software and hardware across different platforms, making them accessible and easy to integrate into various applications.
- Scalability: 2D barcodes can be printed or displayed at different sizes while still retaining their data capacity and readability. This scalability allows for flexibility in design and usage.
Common examples of 2D barcodes include QR codes, Data Matrix codes, PDF417, and Aztec codes. Each of these formats has specific characteristics and advantages that make them suitable for particular use cases.
What is a transmit buffer?
A transmit buffer, also known as a transmit buffer register or transmit buffer memory, is a data storage area in a computer or communication system used for temporarily holding data that is intended to be transmitted from one device or component to another. Transmit buffers are commonly used in various hardware components, including network interface cards (NICs), serial communication ports (such as UARTs), and storage devices (e.g., hard drives or SSDs). Here are the key characteristics and functions of a transmit buffer:
- Data Temporary Storage: The primary purpose of a transmit buffer is to provide temporary storage for data before it is transmitted from one device to another. It holds the data that is queued up for transmission.
- FIFO (First-In-First-Out) Operation: Transmit buffers typically operate on a FIFO basis, meaning that the data is stored in the buffer in the order it was received and is transmitted in the same order. This ensures that data is transmitted sequentially and maintains the integrity of the data stream.
- Flow Control: Transmit buffers can play a role in flow control mechanisms to prevent data overflow or loss during transmission. For example, when transmitting data over a network connection, if the transmit buffer becomes full, it can signal to the sender to pause or slow down data transmission until the buffer has space available.
- Hardware Abstraction: Transmit buffers abstract the lower-level hardware details of the transmission process. This allows the higher-level software or protocols to interact with the transmit buffer rather than dealing directly with the hardware components responsible for data transmission.
- Buffer Size: The size of the transmit buffer can vary depending on the hardware and its intended use. Larger buffers can accommodate more data but may introduce additional latency due to the time required to fill or empty the buffer.
- DMA (Direct Memory Access) Support: In some systems, DMA controllers can be used to transfer data directly between memory and the transmit buffer without involving the CPU, which can improve data transfer efficiency.
- Interrupt Generation: Transmit buffers can generate interrupts or other signals to notify the system or software when data transmission is complete or when the buffer needs attention (e.g., it’s full or empty).
- Error Handling: Transmit buffers may include error-checking mechanisms to detect and report data transmission errors or issues, ensuring data integrity during transmission.
- Synchronization: In multi-threaded or multi-process environments, transmit buffers can be used to synchronize data transmission among multiple threads or processes to prevent conflicts and ensure orderly data delivery.
- Customization: Some transmit buffers may allow for customization or configuration of parameters, such as buffer size, interrupt thresholds, or flow control settings, to adapt to specific system requirements.
- Real-Time Systems: Transmit buffers are crucial in real-time systems where precise timing and control over data transmission are essential. They help ensure that data is transmitted and received within specified timeframes.
In summary, a transmit buffer serves as an intermediate storage location for data before it is transmitted from one component or device to another. It plays a vital role in managing data flow, improving efficiency, and maintaining the reliability of data transmission in various computer and communication systems.
What are the operators of VHDL?
VHDL (VHSIC Hardware Description Language) is a powerful language commonly used for modeling and simulating digital circuits, including field-programmable gate arrays (FPGAs) and application-specific integrated circuits (ASICs). VHDL provides a range of operators for performing various operations on signals and variables within your digital designs. Here are some of the key operators in VHDL:
- Arithmetic Operators:
+
(Addition): Adds two operands.-
(Subtraction): Subtracts the right operand from the left operand.*
(Multiplication): Multiplies two operands./
(Division): Divides the left operand by the right operand.**
(Exponentiation): Computes the left operand raised to the power of the right operand.
- Relational Operators:
=
(Equal to): Tests if two operands are equal./=
(Not equal to): Tests if two operands are not equal.<
(Less than): Tests if the left operand is less than the right operand.<=
(Less than or equal to): Tests if the left operand is less than or equal to the right operand.>
(Greater than): Tests if the left operand is greater than the right operand.>=
(Greater than or equal to): Tests if the left operand is greater than or equal to the right operand.
- Logical Operators:
and
(Logical AND): Performs a bitwise AND operation.or
(Logical OR): Performs a bitwise OR operation.nand
(Logical NAND): Performs a bitwise NAND operation.nor
(Logical NOR): Performs a bitwise NOR operation.xor
(Logical XOR): Performs a bitwise XOR (exclusive OR) operation.xnor
(Logical XNOR): Performs a bitwise XNOR (equivalence) operation.not
(Logical NOT): Performs a bitwise NOT (inversion) operation.
- Shift Operators:
sll
(Shift Left Logical): Shifts the bits of the left operand to the left by the number of positions specified in the right operand.srl
(Shift Right Logical): Shifts the bits of the left operand to the right by the number of positions specified in the right operand.sla
(Shift Left Arithmetic): Similar tosll
, but preserves the sign bit during shifting.sra
(Shift Right Arithmetic): Similar tosrl
, but preserves the sign bit during shifting.
- Concatenation Operator:
&
(Concatenation): Combines two or more operands into a single composite operand.
- Type Conversion Operators:
to
anddownto
: Specify the range of indices for arrays and vectors.(type)
ortype'()
(Type casting): Converts one data type to another, for example, from integer to bit-vector or vice versa.
- Others:
=>
(Association Operator): Associates values with named parameters in records or as part of port mapping in entity instantiations.when
(Conditional Operator): Used for conditional signal assignment or data selection.report
andassert
: Used for verification and debugging by issuing messages and assertions in the VHDL code.
These operators are essential for describing digital logic and creating complex designs in VHDL. When working with VHDL, it’s important to understand how these operators can be used to model and simulate the behavior of your digital circuits accurately.
What are the three working modes of the LTCl709?
- PWM (Pulse-Width Modulation) Mode:
- In this mode, the LTC1709 operates as a pulse-width modulation (PWM) voltage regulator.
- The duty cycle of the high-frequency switching signal is adjusted to control the output voltage.
- PWM mode is typically used for high-efficiency regulation when the load varies over a wide range.
- Power Save Mode:
- In power save mode, the LTC1709 operates as a pulse-frequency modulation (PFM) voltage regulator.
- The switching frequency decreases as the load decreases, which improves efficiency under light load conditions.
- Power save mode is used to reduce quiescent current and improve efficiency when the load is light, helping to extend battery life in battery-powered applications.
- Burst Mode:
- Burst mode is a variation of power save mode designed for even higher efficiency at very light loads.
- In burst mode, the LTC1709 goes into a low-power state between bursts of switching activity.
- This mode is used when the load is very light, and the goal is to minimize power consumption and extend battery life as much as possible.
The specific behavior and transition between these modes may depend on the external components and configuration used with the LTC1709, such as the values of external resistors, capacitors, and the input voltage. The device is designed to automatically transition between these modes based on the load and other operating conditions to optimize efficiency and performance.
Please note that semiconductor devices may receive updates or revisions over time, and new features or operating modes may be introduced in later versions of the LTC1709 or similar devices. For the most accurate and up-to-date information on the LTC1709’s operating modes and features, it’s essential to refer to the datasheet or technical documentation provided by the manufacturer or Analog Devices, Inc.
What are the possible options for indoor coverage after the integration of the three networks?
The integration of three different networks (e.g., cellular networks) to provide indoor coverage typically involves combining resources and technologies to enhance connectivity and ensure comprehensive coverage. The possible options for indoor coverage after such integration may include:
- Distributed Antenna Systems (DAS):
- DAS solutions involve deploying a network of antennas strategically throughout the indoor area, including buildings, malls, stadiums, and airports.
- Each antenna is connected to a central controller, allowing for efficient signal distribution and management.
- DAS can support multiple frequency bands and technologies, including 2G, 3G, 4G LTE, and 5G, making it a versatile choice for network integration.
- Small Cells:
- Small cells are low-power, short-range cellular base stations that can be deployed indoors to improve network coverage and capacity.
- They are particularly effective in dense urban areas, large office buildings, and public venues.
- Small cells can support various cellular technologies and frequency bands, contributing to network integration efforts.
- Wi-Fi Offload:
- Integrating Wi-Fi networks alongside cellular networks can help offload indoor traffic and improve coverage.
- Many smartphones and devices support Wi-Fi calling and data offloading, allowing users to connect to Wi-Fi networks for voice and data services indoors.
- Femtocells:
- Femtocells are small, low-power cellular base stations designed for home or small office use.
- They can enhance indoor coverage and capacity in residential areas, addressing network integration at the individual subscriber level.
- Multi-Operator Neutral Host Systems:
- Neutral host systems are designed to accommodate multiple mobile operators on a single infrastructure.
- They can be deployed in indoor venues, such as sports stadiums and shopping centers, to provide coverage for multiple networks, reducing the need for each operator to build separate infrastructure.
- Signal Boosters/Repeaters:
- Signal boosters or repeaters capture and amplify existing outdoor signals and rebroadcast them indoors.
- They are relatively cost-effective solutions for improving indoor coverage, especially in residential settings.
- In-Building Wireless (IBW) Solutions:
- IBW solutions encompass a range of technologies and strategies for enhancing indoor wireless coverage.
- These solutions may include a combination of DAS, small cells, Wi-Fi, and other technologies tailored to the specific needs of a building or venue.
- 5G NR Indoor Solutions:
- With the deployment of 5G networks, indoor coverage solutions are evolving to support 5G New Radio (NR) technology.
- Indoor 5G solutions may include small cells, DAS, and other technologies optimized for high-speed, low-latency 5G connectivity indoors.
- HetNets (Heterogeneous Networks):
- HetNets combine various network elements, including macrocells, microcells, picocells, and femtocells, to provide seamless indoor and outdoor coverage.
- They optimize network resources based on user demand and location.
- Cloud RAN (C-RAN):
- C-RAN architecture centralizes the baseband processing functions, making it easier to deploy and manage indoor coverage solutions.
- It allows for greater flexibility and scalability in supporting multiple networks and technologies.
The choice of indoor coverage solution or combination of solutions depends on factors such as the specific integration requirements, the density of users, the building’s size and structure, budget constraints, and the technologies and frequencies used by the integrated networks. Customized solutions that leverage a mix of these options are often deployed to meet the unique indoor coverage needs of each scenario.
COMMENTS