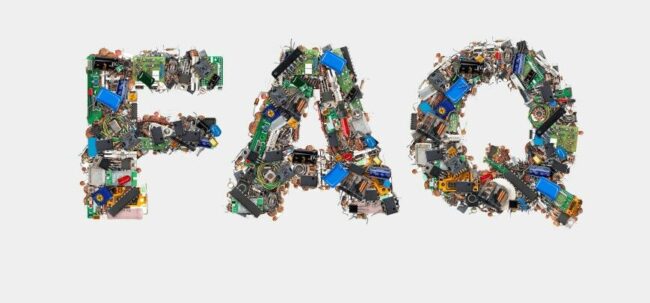
What are the main factors affecting the piezoresistive coefficient?
The piezoresistive coefficient, also known as the gauge factor (GF), is a critical parameter that characterizes the sensitivity of a piezoresistive material or sensor to mechanical strain or stress. It quantifies how much the electrical resistance of the material changes in response to applied mechanical deformation. Several main factors affect the piezoresistive coefficient:
- Material Properties:
- Material Type: Different materials exhibit varying piezoresistive behaviors. Semiconductors like silicon and germanium are commonly used due to their high gauge factors, but other materials like metals and polymers can also be used.
- Crystal Orientation: For single-crystal piezoresistors, the crystallographic orientation can significantly impact the gauge factor. Certain crystal orientations may have higher sensitivity to strain.
- Doping Level: The doping level of semiconductor materials can influence their piezoresistive properties. Higher doping levels often lead to higher gauge factors.
- Mechanical Strain Type:
- Uniaxial vs. Biaxial: The gauge factor can differ depending on whether the material experiences uniaxial (in one direction) or biaxial (in two perpendicular directions) strain. Some materials are more sensitive to one type of strain than the other.
- Operating Temperature:
- Temperature can affect the piezoresistive behavior of a material. The gauge factor may vary with temperature, and certain materials are better suited for specific temperature ranges.
- Stress Concentration:
- The distribution of stress within the material can impact the piezoresistive response. Stress concentration at specific points or interfaces can lead to nonlinear behavior or damage to the sensor.
- Manufacturing Process:
- The fabrication process of the piezoresistive sensor can influence the gauge factor. Factors such as the quality of the sensor’s structure, processing steps, and purity of the material can all play a role.
- Electrical Contacts:
- The electrical connections to the piezoresistive material can introduce additional resistance or alter the strain distribution, affecting the overall sensitivity.
- Aging and Environmental Effects:
- Long-term exposure to environmental factors such as humidity, radiation, and chemicals can degrade the piezoresistive properties of the material and reduce the gauge factor over time.
- Geometric Considerations:
- The geometry and dimensions of the piezoresistive element can also impact its gauge factor. For instance, the length, width, and thickness of a resistor can affect its sensitivity.
- Annealing and Post-Processing:
- Heat treatments and post-processing steps can be used to optimize the piezoresistive properties of the material and enhance its gauge factor.
It’s important to note that the gauge factor is a material-specific property, and the optimal choice of material and design considerations will depend on the specific application requirements. Engineers and researchers often perform characterization experiments and simulations to determine the best combination of materials and sensor design to achieve the desired sensitivity for a given application.
What is cds? What does CDS mean?
“CDS” can refer to several different things depending on the context. Here are some common meanings of “CDS”:
- Certificate of Deposit (CD): In the context of finance and banking, CDS can stand for “Certificate of Deposit.” A Certificate of Deposit is a financial product offered by banks where an individual deposits a sum of money for a specified period at a fixed interest rate. It’s a low-risk, interest-bearing savings account with a maturity date.
- Credit Default Swap (CDS): In the financial world, CDS can also stand for “Credit Default Swap.” A Credit Default Swap is a financial derivative contract that allows one party to protect against the risk of default on a particular debt instrument, such as a bond or loan, by transferring that risk to another party in exchange for regular payments.
- Compact Disc (CD): In the context of technology and entertainment, “CD” refers to a “Compact Disc.” It is an optical storage medium used for audio, video, and data storage. CDs were widely used for music albums and software distribution before digital formats became more prevalent.
- Clinical Decision Support (CDS): In healthcare, “CDS” stands for “Clinical Decision Support.” It refers to computer systems, software, or tools that provide healthcare professionals with information and assistance in making clinical decisions. CDS systems can offer recommendations for diagnosis, treatment, and patient care based on medical knowledge and patient data.
- Circular Dichroism Spectroscopy (CDS): In scientific research, particularly in chemistry and biochemistry, “CDS” can stand for “Circular Dichroism Spectroscopy.” It is a technique used to study the structural characteristics of molecules, especially biomolecules like proteins and nucleic acids, by measuring their differential absorption of circularly polarized light.
- Current Developments Survey (CDS): In the context of surveys or research, “CDS” can be an abbreviation for “Current Developments Survey.” This may refer to a survey or study conducted to gather information on current trends, opinions, or developments in a particular field or industry.
The meaning of “CDS” can vary widely based on the specific domain or industry in which it is used. To understand its precise meaning in a given context, it’s essential to consider the context and the field in which it is used.
How to handle data transfer when SPI is set to host?
SPI (Serial Peripheral Interface) is a common communication protocol used for transferring data between microcontrollers, sensors, displays, and other peripheral devices. When SPI is set to be the host, it typically means that one device, such as a microcontroller or a master controller, is controlling and initiating data transfers with one or more slave devices. Here are the general steps to handle data transfer when SPI is set to the host:
- Initialize the SPI Interface:
- Configure the SPI hardware interface on the host device. This typically involves setting parameters like clock frequency, data format (e.g., data length, bit order), and control signals (e.g., chip select).
- Select the Target Slave Device:
- In a multi-device SPI setup, select the specific slave device you want to communicate with by activating its chip select (CS) signal. Deactivate CS for all other devices.
- Prepare Data for Transmission:
- Load the data you want to transmit into the SPI data buffer or register on the host device. Ensure that the data is properly formatted according to the chosen data format (e.g., MSB or LSB first, data length).
- Initiate Data Transfer:
- Trigger the SPI transfer by sending a clock signal (usually generated by the host) while simultaneously shifting the data out to the selected slave device.
- Wait for Transfer Completion:
- Depending on the SPI hardware and software configuration, you may need to wait for the transfer to complete. Many microcontrollers have flags or interrupts to indicate when the transfer is finished.
- Receive Data (If Necessary):
- If the SPI communication is bidirectional, you can read data received from the slave device after the transmission is complete. Ensure that you have configured the SPI interface to allow for data reception.
- Deactivate the Slave Device:
- After the data transfer is complete, deactivate the chip select (CS) signal for the current slave device. If you intend to communicate with another slave device, activate the appropriate CS for that device.
- Repeat for Additional Transactions:
- If you need to perform multiple SPI transactions with the same or different slave devices, repeat steps 2 to 7 for each transaction.
- Handle Errors and Exceptions:
- Implement error handling routines to manage communication errors, timeouts, or other exceptional conditions that may occur during SPI communication.
- Finalize SPI Communication:
- When you have completed all necessary SPI transactions, finalize the SPI communication by disabling or releasing the SPI hardware resources, as needed.
Remember that the specific implementation details, such as the programming language, hardware configuration, and API calls, may vary depending on the microcontroller or host device you are using. Consult the documentation and resources provided by the manufacturer of your host device and any connected slave devices for precise instructions on using SPI in your particular setup.
What are the characteristics of RFID technology?
Radio-Frequency Identification (RFID) technology is a wireless communication technology that uses radio waves to identify, track, and manage various objects or entities. RFID systems consist of three main components: RFID tags, RFID readers, and a host computer system. The technology offers several characteristics and advantages:
- Contactless Operation: RFID operates without the need for physical contact between the RFID reader and the RFID tag. This non-contact nature is one of its primary advantages, as it allows for quick and automated data capture.
- Unique Identification: Each RFID tag typically has a unique identifier (ID) stored in its memory. This allows for the precise and individual identification of items, assets, or entities, making it useful for inventory management, tracking, and authentication.
- Read/Write Capabilities: Some RFID tags are read-only, meaning their data can only be read, while others are read-write, allowing for data to be both read from and written to the tag. This versatility enables updates to the information associated with an item.
- Data Storage: RFID tags can store varying amounts of data, from a simple identifier to more extensive information, such as product details, manufacturing date, or maintenance history.
- Auto-ID Technology: RFID is considered one of the Auto-ID (Automatic Identification) technologies, along with barcodes and QR codes. However, RFID offers advantages over these other methods, such as higher data capacity, faster reading, and the ability to read multiple tags simultaneously.
- Range and Frequencies: RFID systems operate in different frequency ranges, including low-frequency (LF), high-frequency (HF), ultra-high-frequency (UHF), and microwave. Each frequency range has its characteristics and is suitable for different applications. UHF RFID, for example, provides longer read ranges and is often used in supply chain and logistics.
- Read Range: The read range of RFID tags can vary from a few centimeters to several meters, depending on the frequency and the type of RFID technology (active or passive). Active RFID tags have their own power source and typically offer longer read ranges compared to passive tags.
- Real-Time Tracking: RFID technology allows for real-time tracking of assets or objects. When combined with a network of RFID readers and a central database, it enables businesses to monitor the movement and location of items continuously.
- Durability: Many RFID tags are designed to withstand harsh environmental conditions, including temperature extremes, moisture, and physical impacts. This makes them suitable for use in challenging environments such as manufacturing plants, warehouses, and outdoor applications.
- Security: RFID technology can provide varying levels of security and privacy features. For sensitive applications, encryption and access control can be implemented to protect data on the RFID tags and secure communications between readers and tags.
- Scalability: RFID systems can be easily scaled up to accommodate a large number of tags and readers, making them suitable for applications ranging from small-scale inventory management to large-scale supply chain operations.
- Integration: RFID technology can be integrated into existing systems and processes, including inventory management systems, access control systems, and asset tracking solutions.
- Efficiency and Automation: RFID technology can significantly improve operational efficiency by automating tasks such as inventory counts, asset tracking, and access control, reducing manual labor and human error.
- Cost-Effective: The cost of RFID technology has decreased over the years, making it more accessible for various applications. The cost-effectiveness is often evident in the long-term benefits of improved efficiency and reduced operational costs.
- Compatibility: RFID technology is compatible with various form factors, including RFID tags, labels, cards, and wristbands, making it versatile for different use cases.
It’s important to note that the specific characteristics and capabilities of RFID technology can vary depending on the type of RFID (passive or active), frequency range, and the particular application in which it is used. As a result, businesses and organizations should carefully choose the RFID solution that best fits their needs.
What can be produced with a grounded heat sink?
A grounded heat sink is typically used in electronic and thermal management applications to dissipate heat generated by electronic components or systems. Heat sinks are made of thermally conductive materials like aluminum or copper and are designed to transfer heat away from the heat-generating component to the surrounding environment. When properly grounded and integrated into a system, a heat sink can serve several purposes and be used in various applications:
- Temperature Regulation: Grounded heat sinks help maintain the operating temperature of electronic components within acceptable limits. By dissipating heat, they prevent overheating, which can lead to component failure or reduced performance.
- Cooling CPUs and GPUs: Heat sinks are commonly used to cool central processing units (CPUs) and graphics processing units (GPUs) in computers. They are mounted directly onto these components to transfer heat away from them, allowing for efficient and stable operation.
- Power Electronics Cooling: Grounded heat sinks are essential in power electronic devices such as voltage regulators, power transistors, and rectifiers. They prevent these components from overheating and help maintain their reliability.
- LED Cooling: Light-emitting diodes (LEDs) can generate heat during operation. Heat sinks are used to dissipate this heat, ensuring that LEDs operate at their optimal temperature and maintain their lifespan.
- Amplifiers and Audio Equipment: In audio equipment, heat sinks are often used to cool power amplifiers and other heat-producing components. This ensures that the equipment can operate without distortion or damage due to excessive heat.
- Automotive Electronics: Grounded heat sinks are used in automotive electronics to cool components such as power management modules, LED headlights, and motor controllers.
- Industrial Machinery: Heat sinks are employed in various industrial applications, including motor drives, control systems, and process automation, to maintain the proper operating temperature of critical components.
- Aerospace and Avionics: In aerospace and avionics systems, heat sinks play a crucial role in managing the heat generated by electronic components in a high-temperature environment.
- Renewable Energy Systems: Grounded heat sinks are used in inverters and power electronics for renewable energy systems like solar inverters and wind turbine control systems to prevent overheating and ensure efficient energy conversion.
- Telecommunications: Heat sinks are used in telecommunications equipment, including data centers, servers, and network switches, to dissipate heat generated by processors and networking components.
- Medical Devices: Medical devices, such as diagnostic equipment, may use heat sinks to manage the thermal load generated by electronic components, ensuring the reliability of these critical systems.
- Consumer Electronics: Many consumer electronics, such as laptops, gaming consoles, and audio amplifiers, incorporate heat sinks to maintain safe operating temperatures and prevent thermal throttling.
The specific design and size of a grounded heat sink will vary depending on the application’s thermal requirements, available space, and thermal management goals. Additionally, in some applications, heat sinks may be combined with fans or other cooling solutions for more efficient heat dissipation. Proper grounding ensures the safety and functionality of the heat sink in electronic systems.
Which of the following functions does the MAC sublayer mainly accomplish?
The MAC (Media Access Control) sublayer mainly accomplishes the following functions in a network communication system:
- Frame Encapsulation and Addressing: The MAC sublayer encapsulates data frames received from the higher-layer protocols, adding MAC addresses (hardware addresses) to identify the source and destination devices on the local network. This addressing allows for the correct delivery of data within a local network segment.
- Frame Distribution: The MAC sublayer is responsible for controlling access to the shared communication medium, such as an Ethernet segment. It uses various media access control methods, including Carrier Sense Multiple Access with Collision Detection (CSMA/CD) in Ethernet, to ensure that multiple devices on the same network segment can take turns transmitting data without causing collisions.
- Frame Framing: It defines the frame format, which includes the structure of the data frame, frame header, and frame trailer. This format provides synchronization and error detection capabilities.
- Frame Error Detection: The MAC sublayer includes error detection mechanisms, such as Frame Check Sequence (FCS) or CRC (Cyclic Redundancy Check), to identify and discard frames with transmission errors. This helps maintain data integrity.
- Frame Buffering and Prioritization: It manages frame buffering and prioritization in case multiple devices are contending for access to the communication medium. This ensures that higher-priority frames (e.g., real-time data) get transmitted with minimal delay.
- Frame Fragmentation and Reassembly: In some cases, the MAC sublayer can handle frame fragmentation and reassembly. It breaks large frames into smaller fragments for transmission and reassembles them at the receiving end. This is particularly relevant in wireless communication systems with size restrictions on data frames.
- Collision Handling: In Ethernet networks (particularly in the context of older standards like Ethernet with CSMA/CD), the MAC sublayer detects collisions and initiates collision resolution procedures to avoid data packet collisions.
- Flow Control: While the primary responsibility for flow control often falls on higher-layer protocols (e.g., TCP at the transport layer), the MAC sublayer can play a role in local flow control within a network segment. It may implement mechanisms to manage the rate of incoming frames to prevent network congestion.
- Medium Arbitration: In shared-medium networks like Ethernet, the MAC sublayer uses arbitration mechanisms to determine which device can transmit data next. This prevents multiple devices from trying to transmit simultaneously, which can result in collisions.
The MAC sublayer primarily operates at the Data Link Layer (Layer 2) of the OSI model and is essential for establishing communication within a local network segment. Different network technologies may have variations in how the MAC sublayer functions, but its core responsibilities are consistent across various LAN (Local Area Network) technologies.
What are the characteristics of the thermistor?
Thermistors are specialized resistors that exhibit distinct electrical resistance characteristics in response to changes in temperature. These characteristics make thermistors valuable in a wide range of temperature-sensing and control applications. The key characteristics of thermistors include:
- Non-Linear Resistance-Temperature Relationship: The most significant characteristic of thermistors is their non-linear resistance-temperature relationship. Unlike standard resistors, which have a linear resistance change with temperature, thermistors’ resistance varies exponentially with temperature. This non-linearity makes them particularly useful for precise temperature measurements and control over specific temperature ranges.
- High Sensitivity: Thermistors are highly sensitive to temperature changes, which means that even small temperature variations can result in significant resistance changes. This sensitivity is especially beneficial in applications requiring precise temperature monitoring.
- Negative Temperature Coefficient (NTC) and Positive Temperature Coefficient (PTC): There are two main types of thermistors: NTC and PTC.
- NTC Thermistors: Negative Temperature Coefficient thermistors exhibit a decrease in resistance as temperature increases. They are commonly used in applications like temperature sensing, compensation, and control.
- PTC Thermistors: Positive Temperature Coefficient thermistors experience an increase in resistance with rising temperature. PTC thermistors are often used in applications where temperature-related protection or self-regulation is needed.
- Broad Temperature Range: Thermistors are available in a wide range of temperature ratings, from extremely low temperatures (e.g., cryogenic applications) to very high temperatures (e.g., industrial heating systems). The choice of thermistor type and characteristics depends on the specific temperature range of interest.
- Rapid Response Time: Thermistors have a rapid response time to changes in temperature due to their high sensitivity. This feature is advantageous in applications where quick temperature monitoring and control are essential.
- Compact Size: Thermistors are small and compact, making them suitable for integration into various electronic devices and systems without taking up much space.
- Wide Resistance Range: Thermistors are available with a broad range of resistance values, allowing them to be tailored to specific application requirements.
- High Accuracy and Precision: When properly calibrated and characterized, thermistors can provide high levels of accuracy and precision in temperature measurements and control.
- Low Cost: Thermistors are relatively inexpensive compared to some other temperature sensing technologies, making them cost-effective for many applications.
- Variety of Shapes and Configurations: Thermistors come in various shapes and configurations, including bead, disc, and chip form factors, allowing for flexibility in design and installation.
- Self-Heating: One potential drawback of thermistors is that they generate heat when current flows through them. This self-heating effect can be a consideration in some applications and may require compensation or mitigation measures.
- Application-Specific Selection: Choosing the right thermistor for an application often involves considering factors such as temperature range, sensitivity, resistance values, and electrical characteristics. NTC and PTC thermistors have distinct applications, and selecting the appropriate type is crucial.
In summary, thermistors are specialized temperature-sensing devices with non-linear resistance-temperature characteristics, high sensitivity, and rapid response times. Their versatility, combined with their ability to provide precise temperature measurements and control, makes them valuable in a wide range of applications, including temperature compensation, thermal protection, and temperature control systems.
What FPGA products does Xilinx currently have?
As of my last knowledge update in September 2021, Xilinx offers a range of FPGA (Field-Programmable Gate Array) products for various applications, including data centers, networking, automotive, industrial, aerospace, and more. However, product offerings in the technology industry can change frequently, so it’s essential to check the latest information on Xilinx’s official website or other reliable sources for the most up-to-date product details.
As of my last update, some of Xilinx’s FPGA product families included:
- Virtex UltraScale and Virtex UltraScale+ FPGAs: These are high-performance FPGAs designed for demanding applications such as data centers, networking, and wireless communication. They offer features like high-speed transceivers, large FPGA fabric, and advanced processing capabilities.
- Kintex UltraScale and Kintex UltraScale+ FPGAs: These are mid-range FPGAs that provide a balance between performance and power efficiency. They are often used in applications like 5G wireless, video processing, and aerospace.
- Artix-7 FPGAs: Artix-7 FPGAs are cost-effective, low-power devices suitable for a wide range of applications, including industrial automation and automotive.
- Zynq-7000 SoCs: These are System-on-Chip (SoC) devices that combine ARM Cortex-A9 processing cores with FPGA fabric. They are used in applications requiring both embedded processing and programmable logic, such as automotive, industrial automation, and medical devices.
- Zynq UltraScale+ MPSoCs: These are more advanced SoC devices with ARM Cortex-A53 and Cortex-R5 processing cores, along with FPGA fabric. They are used in applications like autonomous vehicles and advanced driver-assistance systems (ADAS).
- Spartan-7 FPGAs: Spartan-7 FPGAs are low-cost, low-power devices suitable for applications with cost constraints, such as consumer electronics and IoT devices.
- Versal ACAPs (Adaptive Compute Acceleration Platforms): Versal is a newer family of devices from Xilinx that combines FPGA fabric with specialized processing engines to accelerate various workloads, including AI/ML, networking, and 5G.
- Alveo Accelerator Cards: Xilinx offers Alveo accelerator cards powered by various FPGA families, designed for accelerating workloads in data centers and cloud environments, including AI inference, data analytics, and video transcoding.
- Vivado Design Suite: Xilinx provides the Vivado Design Suite, which includes tools for FPGA design, synthesis, implementation, and debugging.
- Vitis Unified Software Platform: This platform combines development tools and libraries for both hardware (FPGA) and software development, making it easier to develop applications for Xilinx FPGAs and SoCs.
Please note that Xilinx’s product lineup may have evolved or expanded since my last update in September 2021. To get the latest information on Xilinx’s FPGA products, features, and availability, visit the official Xilinx website or consult with Xilinx distributors and representatives. Additionally, Xilinx has been acquired by AMD, so future product developments may be influenced by AMD’s strategy and roadmap.
What is a hub?
A hub, in the context of networking and data communication, is a basic networking device that connects multiple devices in a local area network (LAN). Its primary function is to serve as a central point for connecting network cables and facilitating communication among devices. Hubs operate at the physical layer (Layer 1) of the OSI (Open Systems Interconnection) model and are one of the simplest networking devices. There are mainly two types of hubs:
- Passive Hub: A passive hub is a basic, unpowered device that simply connects network cables together. It doesn’t amplify or regenerate the signals passing through it. As a result, the signal strength weakens as it travels from one device to another, and the maximum distance between devices is limited. Passive hubs are rarely used in modern networks.
- Active Hub (or Network Hub): An active hub, often referred to as a network hub, is a powered device that not only connects cables but also regenerates and amplifies the incoming electrical signals before transmitting them to all connected devices. This ensures that the signals can travel longer distances and maintain their integrity. Active hubs are equipped with multiple ports (typically 4, 8, 12, or 24 ports) to accommodate multiple network connections.
Here are some key characteristics and features of hubs:
- Broadcasting: Hubs operate in a broadcast mode, meaning that when a device connected to a hub sends data, the hub forwards that data to all other devices connected to it, regardless of whether the data is intended for them. This broadcasting can lead to network congestion and inefficient use of network bandwidth.
- No Intelligence: Hubs lack the intelligence and decision-making capabilities found in more advanced networking devices like switches and routers. They do not have the ability to make forwarding decisions based on MAC (Media Access Control) addresses or IP addresses.
- Collision Domain: In a hub-based network, all devices connected to the hub share the same collision domain. This means that if two devices transmit data simultaneously, causing a collision, all devices connected to the hub are affected. Collision domains can lead to network performance issues and are a characteristic of shared Ethernet networks.
- Limited in Modern Networks: Due to their limitations, hubs have largely been replaced by more advanced networking devices like switches. Switches offer better performance, more efficient use of bandwidth, and the ability to create separate collision domains for connected devices.
In summary, a hub is a basic networking device used to connect multiple devices in a LAN. It operates at the physical layer and is mainly responsible for connecting cables and forwarding data to all connected devices. While hubs were once common in Ethernet networks, they have largely been replaced by switches and other advanced networking equipment that offer better performance and manageability.
What other technologies are available to achieve system level control?
System-level control, also known as systems control or supervisory control, involves managing and coordinating the operation of various components within a complex system to achieve specific goals or objectives. There are several technologies and techniques available to achieve system-level control, depending on the type of system and its requirements. Here are some of the key technologies and approaches:
- Programmable Logic Controllers (PLCs): PLCs are industrial digital computers specifically designed for controlling manufacturing processes, machinery, and systems. They are commonly used in manufacturing, process automation, and industrial control applications.
- Distributed Control Systems (DCS): DCS is a control system architecture designed for large-scale industrial processes, such as those in power plants, chemical plants, and refineries. DCSs consist of multiple control units distributed throughout the system, often communicating over a network, to provide centralized control and monitoring.
- Supervisory Control and Data Acquisition (SCADA): SCADA systems are used for monitoring, controlling, and managing industrial processes and critical infrastructure. They often include human-machine interface (HMI) software for operators to interact with the system and make decisions.
- Industrial Internet of Things (IIoT): IIoT involves connecting sensors, devices, and equipment to the internet to gather data and enable remote monitoring and control. Cloud-based IIoT platforms can provide system-level control and analytics for various industries.
- Building Automation Systems (BAS): BAS are used to control and monitor building systems such as HVAC (heating, ventilation, and air conditioning), lighting, security, and access control. They help optimize energy usage and provide occupant comfort.
- Automated Control Systems: In various domains, automated control systems use software and algorithms to make real-time decisions and adjustments based on sensor data. Examples include autonomous vehicles, industrial robots, and smart grid systems.
- Energy Management Systems (EMS): EMSs are used in the energy sector to optimize the generation, distribution, and consumption of electrical energy. They enable utilities to manage their grids more efficiently.
- Process Control Systems: These systems are used in industries such as chemical manufacturing, oil and gas, and food processing to monitor and control complex processes. They often use advanced control algorithms and feedback loops.
- Model Predictive Control (MPC): MPC is an advanced control strategy that uses mathematical models of a system to make predictions and optimize control actions. It is used in various industries, including automotive, aerospace, and process control.
- Artificial Intelligence (AI) and Machine Learning (ML): AI and ML techniques are increasingly used for system-level control in applications like autonomous vehicles, smart grids, and predictive maintenance. These technologies enable systems to adapt and make decisions based on data patterns.
- Real-Time Operating Systems (RTOS): RTOSs provide a platform for developing and running real-time and embedded control systems. They are commonly used in applications where timing and response are critical, such as automotive control units and robotics.
- Custom Control Software: In some cases, custom control software is developed to meet specific system control requirements. This software can be tailored to the unique characteristics of the system and its operational goals.
The choice of technology and approach for achieving system-level control depends on factors such as the nature of the system, its complexity, the required level of automation, the industry or application, and the specific goals of control (e.g., optimization, safety, energy efficiency). Additionally, many modern control systems use a combination of these technologies to achieve efficient and effective system-level control.
COMMENTS